These vast costs can be reduced
Page 40
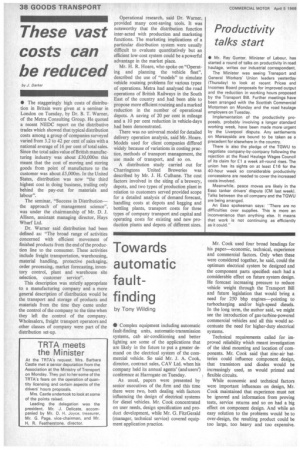
If you've noticed an error in this article please click here to report it so we can fix it.
by J. Darker
• The staggeringly high costs of distribution in Britain were given at a seminar in London on Tuesday, by Dr. B. T. Warner, of the Metra Consulting Group. He quoted a recent NEDC report on the distributive trades which showed that typical distribution costs among a group of companies surveyed varied from 3.2 to 42 per cent of sales with a national average of 16 per cent of total sales. Since the total sales value of British manufacturing industry was about £30,000m this meant that the cost of moving and storing goods from point of manufacture to the customer was about £5,000m. In the United States, distribution was now "the third highest cost in doing business, trailing only behind the pay-out for materials and labour".
The seminar, "Success in Distribution— the approach of management science", was under the chairmanship of Mr. D. J. Allison, assistant managing director, Hays Wharf Ltd.
Dr. Warner said distribution had been defined as: "The broad range of activities concerned with efficient movement of finished products from the end of the production line to the consumer. These activities include freight transportation, warehousing, material handling, protective packaging, order processing, market forecasting, inventory control, plant and warehouse site selection, customer service".
This description was strictly appropriate to a manufacturing company and a more general description of distribution would be the transport and storage of products and materials from the time they came under the control of the company to the time when they left the control of the company. Wholesalers, freight transport operators and other classes of company were part of the distribution set-up. Operational research, said Dr. Warner, provided many cost-saving tools. It was noteworthy that the distribution function inter-acted with production and marketingfunctions. The marketing implications of a particular distribution system were usually difficult to evaluate quantitatively but an efficient low-cost system could be a powerful advantage in the market place.
Mr. H. R. Hoare, who spoke on "Operating and planning the vehicle fleet", described the use of "models" to simulate vehicle routeing problems for various types of operations. Metra had analysed the road operations of British Railways in the South East of the country and had been able to propose more efficient routeing and a marked reduction in the number of operational depots. A saving of 20 per cent in mileage and a 10 per cent reduction in vehicle-days had been demonstrated.
There was no universal model for detailed delivery operation analysis, said Mr. Hoare. Models used for client companies differed widely because of variations in costing practice, methods of transport management, the use made of transport, and so on.
A distribution study carried out for Charringtons United Breweries was described by Mr. J. H. Culhane. The cost factors involved in the siting of a brewery, depots, and two types of production plant in relation to customers served provided scope for a detailed analysis of demand forecast, handling costs at depots and kegging and bottling plants, transport costs for three types of company transport and capital and operating costs for existing and new production plants and depots of different sizes.