THE ARMY IS HELPI THE TYRE POSITION
Page 26
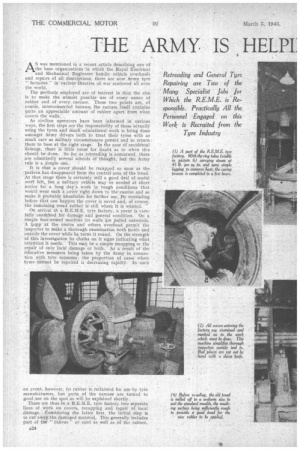
Page 27
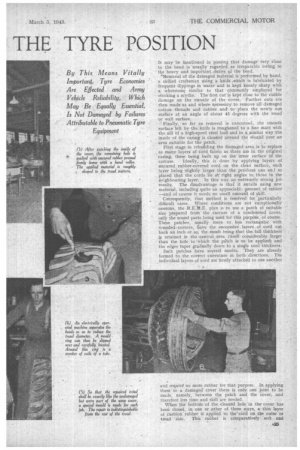
Page 28
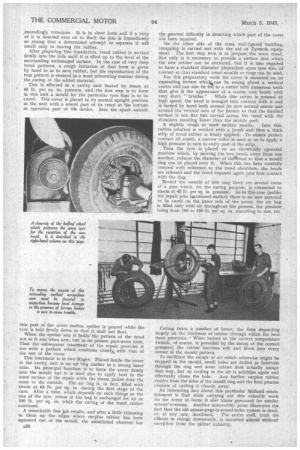
If you've noticed an error in this article please click here to report it so we can fix it.
AS was mentioned in a recent article.describing one of the base organizations in which the Royal Electrical and Mechanical Engineers handle vehicle overhauls and repairs of all descriptions, there are now Army tyre "
factories" in various theatres of war scattered all over the world.
The methods employed are of interest in that the aim is to make the utmost possible use of every ounce of °rubber and of every carcase. These two points are, of comic, interconnected because the carcase itself contains 'quite an appreciable-amount. of rubber apart from what
covers the' walls.. •
M civilian operators have been informed in various ways, the first steps are the responsibility of those actually using the tyres and friuCh.ecluCational work is being done amongst As-my drivers both to treat their tyres with as ?. much care as military circurnStances permit and to return them to base at the right stage. In the case of accidelital dainage, there is little mon/ for doubt as to when this should be done. So far as _retreading is Concerned, there are admittedly several schools of thought, but the Army
rule is a simple one. "
It is that a cover should be recapped so soon as the -pattern has disappeared from the central area Of the tread. At that stage there is certainly still a good "deal of useful west Teft, but a military vehicle may be needed at short notice for a long day's work in rough conditions that would wear such a cover right down to the'canvas and so make it probably unsuitable for further use, By retreading before that can happen the cover is saved and, of course, the remaining tread rubber is still where it is wanted.
On arrival a:t. a R.E.M.E, tyre factory, a cover is carefully examined for damage and genetal condition. On a simple four-armed machine its walls are pulled outwards. A lampat the centre and others overhead permit the inspector to make a thorough examination both inside and 'outside the cover while he turns it round. On the strength of this investigation he chalks on it signs indicating what attention it needs. This may be a simple recapping or the repair of only local damage or both. As a result of the educative measures being taken by the Army in connection with tyre economy, the proportion of cases where tyres Cannot be repaired is decreasing rapidl. In such an event, however, its rubber is reclaimed for use tyre
manufacturers, but parts of the carcase are turned to good use on the spot as will be estplained shortly. There are thus in a R.E.M.E. tyre factory two separate lines of work on covers, recapping and repair of local damage. Considering the latter first, the initial step is to cut away the damaged material, This generally includes part Of the " canvas' or cord as well as of the rubber. It may be mentioned in passing that damage very close to the bead is usually regarded as irreparable owing to the heavy and inapo'rtnnt.duties of the bead.
4Removal of the damaged material is performed by hand, a skilled craftsman using a knife .which is lubricated by frequent dippings in water and is kept keenly sharp with a whetstone 'similar to that commonly employed for stroking a scythe. The first cut is kept close to the visible damage on the outside of the cover. Further cuts are then made as and where necessary to remove all damaged cotton threads and rubber and to place the newly cut surface at an angle of about 45 degrees with the tread or wall surface.
Finally, so far as removal is concerned, the smooth surface left by the knife is roughened to a fine matt with the aid of a high-speed steel buff and in a similar way the inside of the casing is cleaned around the Wound over an area suitable for the patch.
First stage in rebuilding the damaged area is to replace as many layers of Cord, fabric as there are in the original casing, these being built up on the inner surface of the carcase. Ideally, this is done by applying layers of .uncured rubber-covered cord on the clean surface, each layer being slightly larger than the previous one anl so placed that the cords lie at right angles to, those in the . neighbouring layer. In this way an extremely strong job results. The disadvantage is thaf it entails using new material, including quite an appreciabh 9.mount of rubber —and of course it needs no small amount of skill.
Consequently, that method is reserved for particularly difficult cases. Where conditions are not exceptionally' onerous, the .R.E.M.E. plan is to use a patch of suitable size prepared from the carcase of a condemned cover, °ma'y the sound parts being used for this purpose, of course. These patches, usually ,more or less rectangular with rounded-corners, have the successive layers of cord cut back an inch or so, the result being that the full thickness is retained in the central area (itself considerably larger than the hole. to which the pitch is to be applied) and the edges taper gradually down to a single cord thickness.
Such patches have several merits. They are already formed to the correct curvature in both directions. The .individual layers of cord are firmly attached to one another
and require no more rubber for that purpose. In applying them to a damaged cover there is only one joint to be made, namely, between the patch and the cover, and therefore less time and skill are needed.
When the bottom .of the cleaned hole in the cover has beee closed, in one or other of these ways, a thin layer of cushion rubber is applied to the` cord on the outer or tread side. This rubber is comparatively soft and
,exceedingly tenacious. It is in sheet form, and if a strip of it is doubled over on to itself the join is immediately so strong that a determined attempt to separate it will result only in tearing the rubber.
After preparing this foundation, tread rubber is worked firmly into the hole until it is filled up to the level of the surrounding undamaged surface. In the case of very deep tread patterns, a rough imitation of that form is given by hand so as to save. rubber, but the reproduction, of the true pattern is ensured ina most interesting' manner during
the curing of the added material.
This is effected in a cavity unit heated by steam at 85 lb. per sq. in. pressure, and .the first step is to form in this unit a mould for the particular tyre that is to be cured. This cover is placed_ in its normal upright position in the unit with a sound part of its tread at the bottom or operative part of thle device. Into the spach outside this part of the cover molten spelter is poured while the tyre is held firmly down so that it shall not float. '
When the ,spelter sets it holds'the pattern of the tread not as it was when new, but in its present part-worn form. Thus the subsequent treatment of the repair provides it too with a pattern which conforms closely,. with that of the rest of the cover.
This treatment is in two' Stages. Placed inside the cover in the cavity unit is an air 'hag similar to a Strong inner tube. Its principal function is to force the cover firmly into the mould but it is used also to apply heat to the inner surface of the repair while the steam jacket does the same to the outside. The air bag is, in fact, filled with steam at 66 lb. per sq. in. during the first stage of the cure. After a time, which depends on such things as the size of •the tyre, steam in the bag is" exchanged for air at 100 lb. per sq. in. while the curing of the tread rubber continues.
A remarkably fine job results, and after a little trimming to clean up the edges where surplus rubber has been squeezed out of the mould, the uninitiated observer has the greatest difficulty in detecting which part of the cover has been repaired.
On the other side of the Same well-lighted building, recapping is carried out with the aid of Tyresole equipment. The first step here is to prepare_ the worn tread. Not only is it necessary to provide a surface into which the new rubber can be anchored, but it is also required to have a standard diameter (dependent upon tyre size, of course) so that standard tread moulds or rings can be used. For this preparatory work the cover is mounted on an . expanding fixture whiccan be swung about a vertical centre and can also be fed to a cutter with numerous teeth that give it the appearance of a coarse wire brush with very short " bristles." While this cutter is rotated at high speed, the tread is brought into contact With it and is tarried by hand both around its own normal centre and around the vertical axis of the fixture so that the finished surface is not flat but curved across the tread with the shoulders standing lower than the middle part. A slightly rough or matt surface results. Into this, rubber solution is worked with a brush and then a thick sttip of tread rubber ts firmly applied: To ensure perfect contact all round, a narrow roller is used so as to apply a high pressure in turn to every.part of the strip.
Then the tyre is placed on an electrically operated machine which, by moving the two beads away from one another, reduces the diameter of thestread so that a mould ring can be placed over it. When this has been carefully centred with reference to the tread shoulders, the beads are released and the tread expands again ioto firm contact with the ring.
Round -the outside of this ring there are several turns of a pipe which, for the curing purpose, is connected to steam at 45 lb. per sq. in. pressure. As in this case (unlike the repair jobs nentioned earlier) there is no new material to be cured on the inner side of the cover, the air bag is filled only with air throughout the process, the pressure being from 100 to 150 lb. per sq in. according to size, etc Curing takes a number of hours, the time depending largely on the thickness of rubber through which the heat must penetrate.— When heated to 'the correct temperature (which, of course, is provided by the Steam at the correct pressure) the rubber becomes soft and flows into every corner of the mould pattern.
To facilitate the escape of air which otherwise might be trapped in the mould, small holes are drilled at intervals through the ring and some rubber doe § actually escape that way, but on cooling in the air it solidifies again and effectually closes, the hole. Any further surplus rubber exudes from the sides of the mould ring and the final process consists of cutting it cleanly away.
An interesting fact about this particular Midland establishment is that while carrying out this valuable work for the Army at home it also trains personnel for similar serviceoverseas. Another noteworthy point illustrates the fact that the old square-pegs-in-round-holes system is dead, or, at any rate, moribund. The entire staff, from the officers in charge downwards, is recruited almost without exception from the rubber industry.