SPEEDIER HANDLING MECHANICAL WAY
Page 54
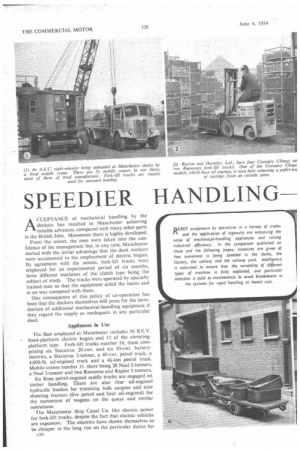
Page 55
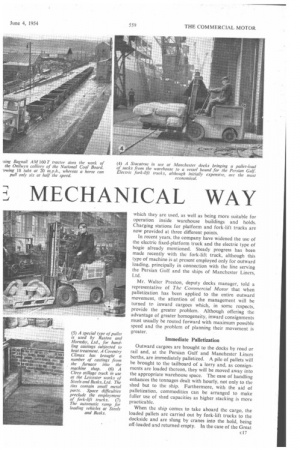
Page 56
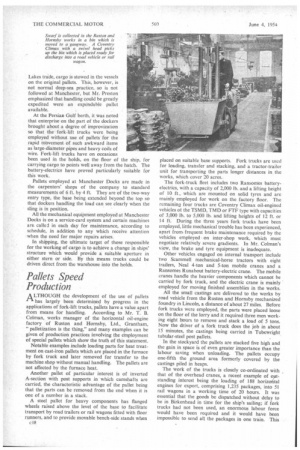
Page 59
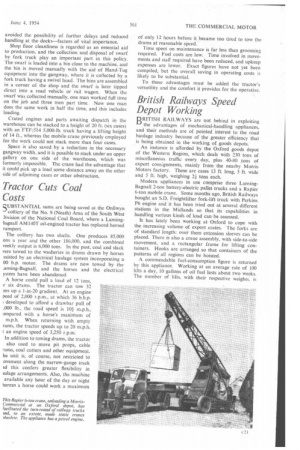
Page 60
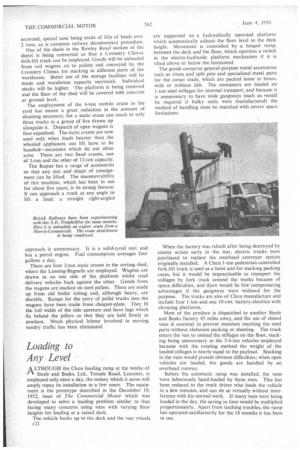
If you've noticed an error in this article please click here to report it so we can fix it.
ACCEPTANCE of mechanical handling by the dockers has resulted in Manchester achieving notable advances, compared with many other ports in the British Isles. Movement there is highly developed.
From the outset, the men were taken into the confidence of the management but, in any case, Manchester started with the initial advantage that the dock workers were accustomed to the employment of electric bogies. By agreement with the unions, fork-lift trucks were employed for an experimental period of six months, three different machines of the clutch type being the subject of study. The trucks were operated by specially trained men so that the equipment aided the teams and in no way competed with them.
One consequence of this policy of co-operation has been that the dockers themselves will press for the introduction of additional mechanical-handling equipment if they regard the supply as inadequate in any particular shed.
Appliances in Use
The fleet employed at Manchester includes 30 B.E.V. fixed-platform electric bogies and 12 of the elevatingplatform type. Fork-lift trucks number 16, these comprising six Stacatruc 20-cwt. and six 30-cwt. batteryelectrics, a Stacatruc 2-tonner, a 40-cwt. petrol truck, a 4,000-lb. oil-engined truck and a 4i-ton petrol truck. Mobile cranes number 31, there being 28 Neal 2-tonners, a Neal 3-tonner and two Ransome and Rapier 3-tonners.
Six Ross petrol-engined saddle trucks are engaged on timber handling. There are also four oil-engined hydraulic loaders for trimming bulk cargoes and nine shunting tractors (five petrol and four oil-engined) for the movement of wagons on the quays and similar operations.
The Manchester Ship Canal Co. like electric power for fork-lift trucks, despite the fact that electric vehicles are expensive. The electrics have shown themselves to be cheaper in the long run on the particular duties for et 6 which they are used, as well as being more suitable for operation inside warehouse buildings and holds. Charging stations for platform and fork-lift trucks are now provided at three different points.
In recent years, the company have widened the use of the electric fixed-platform truck and the electric type of bogie already mentioned. Steady progress has been made recently with the fork-lift truck, although this type of machine is at present employed only for outward loading, principally in connection with the line serving the Persian Gulf and the ships of Manchester Liners, Ltd.
Mr. Walter Preston, deputy docks manager, told a representative of The Commercial Motor that when palletization has been applied to the entire outward movement, the attention of the management will he turned to inward cargoes which, in some respects, provide the greater problem. Although offering the advantage of greater homogeneity, inward consignments must usually be routed forward with maximum possible speed and the problem of planning their movement is greater.
Immediate Palletization Outward cargoes are brought to the docks by road or rail and, at the Persian Gulf and Manchester Liners berths, are immediately palletized. A pile of pallets will be brought to the tailboard of a lorry and, as consignments are loaded thereon, they will be moved away into the appropriate warehouse space. The ease of handling enhances the tonnages dealt with hourly, not only to the shed but to the ship. Furthermore, with the aid of palletization. commodities can be arranged to make fuller use of shed capacities as higher stacking is more practicable.
When the ship comes to take aboard the cargo, the loaded pallets are carried out by fork-lift trucks to the dockside and are slung by cranes into the hold, being off-loaded and returned empty. In the ease of the Great Lakes trade, cargo is stowed in the vessels on the original pallets. This, however, is not normal deep-sea practice, so is not followed at Manchester, but Mr. Preston emphasized that handling could be greatly expedited were an expendable pallet available.
At the Persian Gulf berth, it was noted that enterprise on the part of the dockers brought about a degree of improvization so that the fork-lift trucks were being employed without use of pallets for the rapid movement of such awkward items as large-diameter pipes and heavy coils of wire. Fork-lift trucks have on occasions been used in the holds, on the floor of the ship, for carrying cargo to points well away from the hatch, The battery-electrics have proved particularly suitable for this work.
Pallets employed at Manchester Docks are made in the carpenters' shops of the company to standard measurements of 6 ft. by 4 ft. They are of the two-way entry type, the base being extended beyond the top so that dockers handling the load can see clearly when the sling is in position.
All the mechanical equipment employed at Manchester Docks is on a service-card system and certain machines are callei in each day for maintenance, according to schedule, in addition to any which receive attention when the need for major repairs arises.
In shipping, the ultimate target of those responsible for the working of cargo is to achieve a change in ships' structure which would provide a suitable aperture in either stern or side. By this means trucks could be driven direct from the warehouse into the holds.
Pallets Speed Production
A LTHOUGH the development of the use of pallets 4-1 has largely been determined by progress in the applications of fork-lift trucks, pallets have a value apart from means for handling. According to Mr. T. B. Colman, works manager of the horizontal oil-engine factory of Ruston and Hornsby, Ltd., Grantham, " palletization is the thing," and many examples can be given of production practices involving the employment of special pallets which show the truth of this statement.
Notable examples include loading parts for heat treatment on cast-iron pallets which are placed in the furnace by fork truck and later removed for transfer to the machine shop without manual handling. The pallets are not affected by the furnace heat.
Another pallet of particular interest is of inverted A-section with post supports in which camshafts are carried, the characteristic advantage of the pallet being that the parts can be removed from the end when it is one of a number in a stack.
A steel pallet for heavy components has flanged wheels raised above the level of the base to facilitate transport by road trailers or rail wagons fitted with floor runners, and to provide movable bench-side stands when c18 placed on suitable base supports. Fork trucks are used for loading, transfer and stacking, and a tractor-trailer unit for transporting the parts longer distances in the works, which cover 20 acres.
The fork-truck fleet includes two Ransomes batteryelectrics, with a capacity of 2,000 lb. and a lifting height of 10 ft , which are mounted on solid tyres and are mainly employed for work on the factory floor. The remaining four trucks are Coventry Climax oil-engined vehicles of the TSMD, TM D or FTF type with capacities of 3,000 lb. to 5,000 lb. and lifting heights of 12 ft. or 14 ft. During the three years fork trucks have been employed, little mechanical trouble has been experienced, apart from. frequent brake maintenance required by the vehicles employed on inter-shop work, which must negotiate relatively severe gradients. In Mr. Colman's view, the brake and tyre equipment is inadequate.
Other vehicles engaged on internal transport include two Scammell mechanical-horse tractors with eight trailers, Neal 4-ton and 5-ton mobile cranes and a Ransomes Runabout battery-electric crane. The mobile cranes handle the heavier components which cannot be carried by fork truck, and the electric crane is mainly employed for moving finished assemblies in the works.
All the small castings are delivered to the works by road vehicle from the Ruston and Hornsby mechanized foundry in Lincoln, a distance of about 27 miles. Before fork trucks were employed, the parts were placed loose on the floor of the lorry and it required three men working eight hours to remove and stack a load of 5 tons. Now the driver of a fork truck does the job in about 15 minutes, the castings being carried in Tubewright tubular-steel post pallets.
In the stockyard the pallets are stacked five high and the gain in space is of even greater importance than the labour saving when unloading. The pallets occupy one-fifth the ground area formerly covered by the castings piled in heaps.
The work of the trucks is closely co-ordinated with that of the overhead cranes, a recent example of outstanding interest being the loading of 188 horizontal engines for export, comprising 1,235 packages, into 51 rail wagons in a working time of 20 hours. It was essential that the goods be dispatched without delay to be in Birkenhead in time for the ship's sailing; if fork trucks had not been used, an enormous labour force would have been required and it would have been impossible to send all the packages in one train. This
avoided the possibility of further delays and reduced handling at the docks—factors of vital importance.
Shop floor cleanliness is regarded as an essential aid to production, and the collection and disposal of swarf by fork truck play an important part in this policy. The swarf is loaded into a bin close to the machine, and the bin is moved manually with the aid of Hand-Tug equipment into the gangway, where it is collected by a fork truck having a swivel head. The bins are assembled in a corner of the shop and the swarf is later tipped direct into a road vehicle or rail wagon. When the swarf was collected manually, one man worked full time on the job and three men part time. Now one man does the same work in half the time, and this includes loading.
Crated engines and parts awaiting dispatch in the warehouse can be stacked to a height of 20 ft. (six cases) with an FTF/51 4 5,000-lb. truck having a lifting height of 14 ft., whereas the mobile crane previously employed for the work could not stack more than four cases.
Space is also saved by a reduction in the necessary gangway width, and it is possible to stack under an upper gallery on one side of the warehouse, which was formerly impossible. The crane had the advantage that it could pick up a load some distance away on the other side of adjoining cases or other obstruction.
Tractor Cuts Coal Costs
QUBSTANTIAL sums are being saved at the OnlIwyn. colliery of the No. 9 (Neath) Area of the South West 3ivision of the National Coal Board, where a Lansing3agnall AMI4OT oil-engined tractor has replaced horsed ransport.
The colliery has two shafts. One produces 85,000 ons a year and the other 186,000, and the combined veekly output is 6,000 tons. In the past, coal and slack vere towed to the washeries in drams drawn by horses .ssisted by an electrical haulage system incorporating a 00 h.p. motor. The drams are now towed by the .ansing-Bagnall, and the horses and the electrical ystem have been abandoned.
A horse could pull a load of 12 tons, r six drams. The tractor can tow 32 3ns up a 1-in-20 gradient. At an engine peed of 2,000 r.p.m., at which 36 b.h.p. developed to afford a drawbar pull of ,000 lb., the road speed is 10i m.p.h., cnripared with a horse's maximum of m.p.h. When returning with empty rams, the tractor speeds up. to 20 m.p.h. I an engine speed of 3,250 r.p.m. In addition to towing drams, the tractor also used to move pit props, cable RIMS, coal cutters and other equipment. he unit is, of course, not restricted to ovement along the narrow-gauge track id this confers greater flexibility in tillage arrangements. Also, the machine available any hour of the day or night tiereas a horse could work a maximum
of only 12 hours before it became too tired to tow the drams at reasonable speed.
Time spent on maintenance is far less than grooming required. Fuel costs are low. Time involved in movements and staff required have been reduced, and upkeep expenses are lower. Exact figures have not yet been compiled, but the overall saving in operating costs is likely to be substantial.
To these advantages must be added the tractor's versatility and the comfort it provides for the operative.
British Railways Speed Depot Working
pRITISH RAILWAYS are not behind in exploiting
the advantages of mechanical-handling appliances, and their methods are of pointed interest to the road haulage industry because of the greater efficiency that is being obtained in the working of goods depots: An instance is afforded by the Oxford goods depot of the Western Region, which deals with 230 tons of miscellaneous traffic every day, plus 40-80 tons of export consignments, mainly from the nearby Morris Motors factory. These are cases 13 ft. long, 5 ft. wide and 5 ft. high, weighing 2 tons each.
Modern appliances in use comprise three LansingBagnall 2-ton battery-electric pallet trucks and a Rapier 6-ton mobile crane. Some months ago, British Railways bought an S.D. Freightlifter fork-lift truck with Perkins P6 engine and it has been tried out at several different stations in the Midlands so that its capabilities in handling various kinds of load can.be assessed.
It has lately been working at Oxford to cope with the increasing volume of export crates. The forks are of standard length: over them extension sleeves can be placed. There is also a crane assembly, with side-to-side movement, and a rectangular frame for lifting containers. Hooks are arranged so that containers of the patterns of all regions can be hoisted.
A commendable fuel-consumption figure is returned by this appliance. Working at an average rate of 100 lifts a day, 10 gallons of oil fuel lasts about two weeks. The number of lifts, with their respective weights, is
recorded, special note being made of lifts of loads over 2 tons, as is common railway documentary procedure. One of the sheds in the Rewley Road section of the depot is being converted so that a Coventry Climax fork-lift truck can be employed. Goods will be unloaded from rail wagons on to pallets and conveyed by the Coventry Climax for stacking in different parts of the warehouse. Better use of the storage facilities will be made and warehouse capacity increased. Individual stacks will be higher. The platform is being removed and the floor of the shed will be covered with concrete at ground level. The employment of the 6-ton mobile crane in the yard has meant a great reduction in the amount of shunting necessary, for a static crane can reach to only three trucks in a group of five drawn up alongside it. Dispatch of open wagons is thus expedited. The static cranes are now used only when loads heavier than the wheeled appliances can lift have to be handled—occasions which do not often arise. There are two fixed cranes, one of 3-ton and the other of 12-ton capacity.
The Rapier has a range of accessories so that any size and shape of consignment can be lifted. The manceuvrability of this machine, which has been in use for about five years, is its strong feature. It can approach a truck at any angle to lift a load: a straight right-angled approach is unnecessary. It is a solid-tyred unit and has a petrol engine. Fuel consumption averages four gallons a day.
There are four 2-ton static cranes in the sorting shed, where the Lansing-Bagnalls are employed. Wagons are drawn in on one side of the platform whilst road delivery vehicles back against the other. Goods from the wagons are stacked on steel pallets. These are made up from old boiler tubing and, although heavy, are durable. Ramps for the entry of pallet trucks into the wagons have been made from chequer-plate. They fit the full width of the side aperture and have lugs which fix behind the pillars so that they are held firmly in position. Much physical labour involved in moving sundry traffic has been eliminated.
Loading to Any Level
A LTHOUGH the Cleco loading ramp at the works of r-s• Steels and Busks, Ltd., Temple Road, Leicester, is employed only once a day, the money which it saves will amply repay its installation in a few years. The equipment is the prototype described in the December 19, 1952, issue of The Commercial Motor which was developed to solve a loading problem similar to that facing many concerns using vans with varying floor heights for loading at a raised deck.
The vehicle backs up to the deck and the rear wheels c22 are supported on a hydraulically operated platform which automatically adjusts the floor level to the deck height. Movement is controlled by a hinged ramp, between the deck and the floor, which operates a switch in the electro-hydraulic platform mechanism if it is tilted above or below the horizontal.
The goods comprise general-purpose metal accessories such as rivets and split pins and specialized metal parts for the corset trade, which are packed loose in boxes, with or without lids. The containers are loaded on 1-ton steel stillages for internal transport, and because it is unnecessary to have wide gangways (such as would be required if bulky units were manufactured) the method of handling must be matched with severe space limitations.
When the factory was rebuilt after being destroyed by enemy action early in the war, electric trucks were purchased to replace the overhead conveyor system originally installed. A Cleco 1-ton pedestrian-controlled fork-lift truck is used as a hoist and for stacking packing cases, but it would be impracticable to transport the stillages by fork truck around the works because of space difficulties, and there would be few compensating advantages if the gangways were widened for the purpose. The trucks are also of Cleco manufacture and include four 1-ton and one 10-cwt. battery-electrics with elevating platforms, Most of the produce is dispatched to another Steels and Busks factory 45 miles away, and the use of closed vans it essential to prevent moisture reaching the steel parts without elaborate packing or sheeting. The truck enters the van to unload the stillages on the floor, stacking being unnecessary in the 5-6-ton vehicles employed because with the existing method the weight of the loaded stillages is nearly equal to the payload. Stacking in the vans would present obvious difficulties; when open vehicles are loaded, the goods are handled by an overhead runway.
Before the automatic ramp was installed, the vans were laboriously hand-loaded by three men. This has been reduced to the truck driver who loads the vehicle in a iew minutes, and can do so virtually without interference with his normal work. If many vans were being loaded in the day, the saving in time would be multiplied proportionately. Apart from teething troubles, the ramp has operated satisfactorily for the 18 months it has been in use.