Twice the Work if the Labour
Page 48
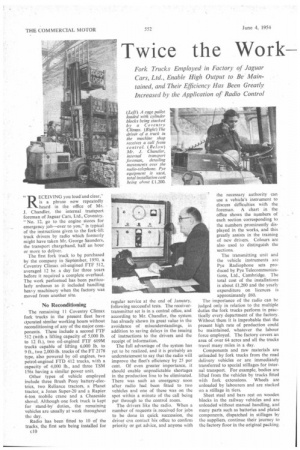
Page 49
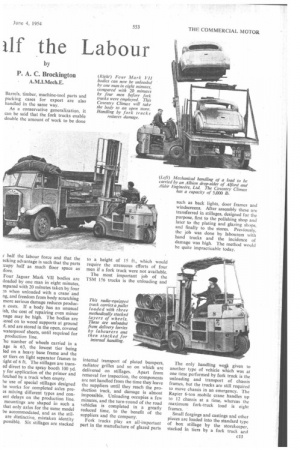
Page 50
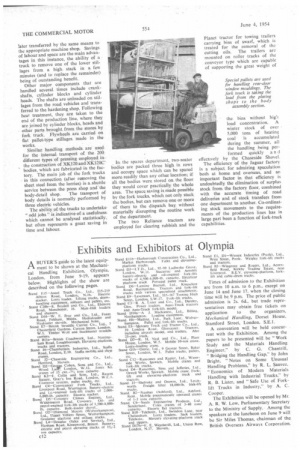
If you've noticed an error in this article please click here to report it so we can fix it.
Fork Trucks Employed in Factory of Jaguar Cars, Ltd., Enable High Output to Be Maintained, and Their Efficiency Has Been Greatly Increased by the Application of Radio Control
by P. A. C. Brockington
" ECEIVING you loud and clear."
is a phrase now repeatedly
heard in the office of Mr. J. Chandler, the internal transport foreman of Jaguar Cars, Ltd., Coventry. " No. 12, go to the engine stores for emergency job—over to you," is typical of the instructions given to the fork-lift truck drivers by radio which formerly might have taken Mr. George Saunders, the transport chargehand, half an hour or more to deliver. The first fork truck to be purchased by the company. in September, 1950, a Coventry Climax oil-engined FTF 512, averaged 12 hr. a day for three years before it required a complete overhaul. The work performed has been particularly arduous as it included handling heavy machinery when the factory was moved from another site.
No Reconditioning
The remaining 11 Coventry Climax fork trucks in the present fleet have d?erated similar working hours without reconditioning of any of the major components. These include a second FTF 512 (with a lifting capacity of 5,000 lb. to 12 ft.), two oil-engined FTF 609M trucks capable of lifting 6,000 lb. to 9 ft., two 2,000-lb. trucks of the FT 2178 type, also powered by oil engines, two petrol-engined FTD 412 trucks, with a capacity of 4,000 lb., and three TSM 156s having a similar power unit
Other types of vehicle employed include three Brush Pony battery-eketries, two Reliance tractors, a. Planet tractor, a Jones Super-20 and a Rapier 6-ton mobile crane and a Chaseside shovel. Although one fork truck is kept for stand-by duties,, the remaining vehicles are usually at work throughout the day.
Radio has been fitted to 10 of the trucks, the first sets being installed for c 10 regular service at the end of January, following successful tests. The receivertransmitter set is in a central office, and according to Mr. Chandler, the system has already shown its great value in the avoidance of misunderstandings, in addition to saving delays in the issuing of instructions to the drivers and the receipt of information.
The full advantage of the system has yet to be realized, and it is probably an understatement to say that the radio will improve the fleet's efficiency by 25 per cent, Of even greater importance, it should enable unpredictable shortages in the production line to be eliminated. There was such an emergency soon after radio had been fitted to two vehicles and one of these was on the spot within a minute of the call being put through to the control room.
The drivers like the radio. When a number of requests is. received for jobs to be done in quick succession, the driver can contact his office to confirm priority or get advice, and anyone with the necessary authority can use a vehicle's instrument to discuss difficulties with the foreman. A chart in the office shows the numbers of each section corresponding to the numbers prominently displayed in the works, and this greatly assists in the training of new drivers. Colours are also used to distinguish the sections.
The transmitting unit and the vehicle instruments are Pye Radiophone sets produced by Pye Telecommunications, Ltd., Cambridge. The total cost of the installations is about £1,200 and the yearly expenditure on licences is approximately £60.
The importance of the radio can be judged only in relation to the multiple duties the fork trucks perform in practically every department of the factory. Without them it is improbable that the present high rate of production could be maintained, whatever the labour force employed. The factory covers an area of over 64 acres and all the trucks travel many miles in a day.
Components and raw materials are unloaded by fork trucks from the road delivery vehicles or are immediately transferred to special stillages. for internal transport. For example, bodies arc lifted from the vehicles by trucks fitted with fork extensions. Wheels are unloaded by labourers and are stacked on a stillage in tiers.
Sheet steel and bars rest on wooden blocks in the railway vehicles and are unloaded without manual handling, and many parts such as batteries and plated components, dispatched in stillages by the suppliers, continue their journey to the factory floor in the original packing. Barrels, timber, machine-tool parts and packing cases for export are also handled in the same way.
As a conservative generalization, it can be said that the fork trucks enable double the amount of work to be done IF half the labour force and that the acking advantage is such that the parts :cupy half as much floor space as lore.
Four Jaguar Mark VII bodies are !loaded by one man in eight minutes, mpared with 20 minutes taken by four m when unloaded with a crane and ng, and freedom from body scratching more serious damage reduces produc n costs. If a body has an unusual ish, the cost of repairing even minor nage may be high. The bodies are fered on to wood supports at ground A, and are stored in the open, covered waterproof sheets, until required for production line.
he number of wheels carried in a age is 63, the lowest tier being led on a heavy base frame and the er tiers on light separator frames to :ight of 6 ft. The stillages are transed direct to the spray booth 100 yd. y for application of the primer and fetched by a truck when empty.
he use of special stillages designed he works for completed axles preas mixing different types and conent delays on the production line. mountings are shaped in such a that only axles for the same model be accommodated, and as the stilare distinctive, mistaken identity possible. Six stillages are stacked
to a height of 15 ft., which would require the strenuous efforts of four men if a fork truck were not available.
The most important job of the TSM 156 trucks is the unloading and internal transport of plated bumpers, radiator grilles and so on which are delivered on stillages. Apart from removal for inspection, the components are not handled from the time they leave the suppliers until they reach the production track, and damage is almost impossible. Unloading occupies a few minutes, and the turn-round of the road vehicles is completed in a greatly reduced time, to the benefit of the suppliers and the company.
Fork trucks play an all-important part in the manufacture of glazed parts such as back lights, door frames and windscreens. After assembly these are transferred in stillages, designed for the purpose, first to the polishing shop and later to the plating and glazing shops, and finally to the stores. Previously, the job was done by labourers with hand trucks and the incidence of damage was high. The method would be quite impracticable today.
The only handling wolk. given to another type of vehicle which was at one time performed by fork truck is the unloading and transport of chassis frames, but the trucks arc still required to move chassis in an emergency. The Rapier 6-ton mobile crane handles up to 12 chassis at a time, whereas the maximum fork-truck load is eight frames. '
Small forgings and castings and other pieces are loaded into the standard type of box stillage by the storekeeper, stacked in tiers by a fork truck and
later transferred by the same means to the appropriate machine shop. Savings of labour and space are the main advantages in this instance, the ability of a truck to remove one of the lower stillages from a high stack in a few minutes (and to replace the remainder) being of outstanding benefit. Other major components that are handled several times include crankshafts, cylinder blocks and cylinder heads. The shafts are unloaded on stillages from the road vehicles and transferred to the hardening shop. Following heat treatment, they are taken to the end of the production line, where they are joined by cylinder blocks, heads and other parts brought from the stores by fork truck. Flywheels are carried on flat pallet-type stillages made in the works.
Similar handling methods. are used for the internal transport of the 200 different types of pressing employed in the construction of XK120 and XK120Cbodies, which arc fabricatedin the factory. The main job of the fork trucks in this connection (after removing the sheet steel from the lorries) is a shuttle service between the press shop and the
body-detail shop. The transport of body details is normally performed by three electric vehicles.
Theability of the trucks to undertake. "odd jobs" is indicative of a usefulness which cannot be analysed statistically, but often represents a great saving in time and labour. In the spares department, two-scater bodies are packed three high in rows and occupy space which can be spared more readily than any other location; if all the bodies were stored on the floor they would cover practically the whole area. The space saving is made possible by the fork trucks, which not only stack the bodies, but can remove one or more of them to the dispatch bay, without materially disrupting the routine work of the department.
The two Reliance tractors are employed for clearing rubbish and the Planet tractor for towing trailers carrying bins of swarf, which is treated for the removal of the cutting oils, The trailers are mounted on roller tracks of the conveyor type which are capable of supporting the great weight of the bins without hiei load concentration. A winter stock of over 5,000 tons of heating coal is accumulated during the summer, all the handling being performed quickly a n d effectively by the Chaseside Shovel.
The efficiency of the Jaguar factory is a subject for admiring speculation both at home and overseas, and an important factor in that efficiency is undoubtedly the elimination of surplus stock from the factory floor, combined with the accurate timing of road deliveries and, of stock transfers from one department to another. Co-ordinating stock movements to the requirements of the production lines has in large part been a function of fork-truck capabilities.