Automatic adjust cuts fitters' check
Page 64
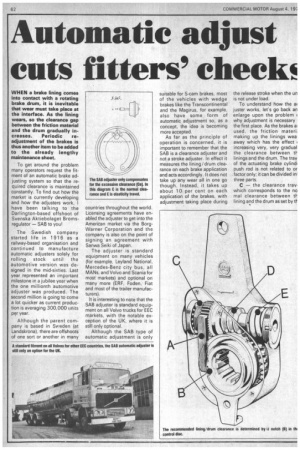
Page 65
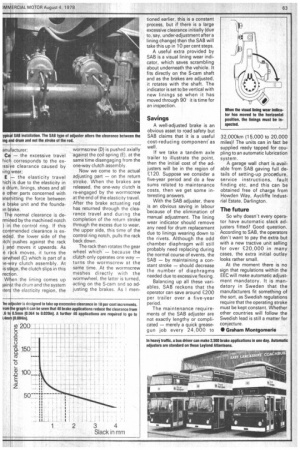
If you've noticed an error in this article please click here to report it so we can fix it.
WHEN a brake lining comes into contact with a rotating brake drum, it is inevitable that wear must take place at the interface. As the lining wears, so the clearance gap between the friction material and the drum gradually increases. Periodic readjustment of the brakes is thus another item to be added to the already lengthy maintenance sheet.
To get around the problem many operators request the fitment of an automatic brake adjusting system so that the required clearance is maintained constantly. To find out how the market is currently developing and how the adjusters work, I have been talking to the Darlington-based offshoot of Svenska Aktiebolaget Brorrisregulator — SAB to you!
The Swedish company started life in 1916 as a railway-based organisation and continued to manufacture automatic adjusters solely for
rolling stock until the automotive version was designed in the mid-sixties. Last year represented an important milestone in a jubilee year when the one millionth automotive adjuster was produced. The second million is going to come a lot quicker as current production is averaging 300,000 units per year.
Although the parent company is based in Sweden (at Landskrona), there are offshoots of one sort or another in many
countries throughout the world. Licensing agreements have enabled the adjuster to get into the American market via the BorgWarner Corporation and the company is also on the point of signing an agreement with Sanwa Seiki of Japan.
The adjuster is standard equipment on many vehicles (for example, Leyland National, Mercedes-Benz city bus, all MANs, and Volvo and Scania for most markets) and optional on
many more roden, Fiat and most of the trailer manufacturers).
It is interesting to note that the SAB adjuster is standard equipment on all Volvo trucks for EEC markets, with the notable exception of the UK, where it is still only optional.
Although the SAB type of automatic adjustment is only suitable for S--cam brakes, most of the vehicles with wedge brakes like the Transcontinental and the Magirus, for example, also have some form of automatic adjustment so, as a concept, the idea is becoming more accepted.
As far as the principle of operation is concerned, it is important to remember that the SAB is a clearance adjuster and not a stroke adjuster_ In effect it measures the lining/drum clearance on each brake application and acts accordingly. It does not take up any wear all in one go though. Instead, it takes up about 10 per cent on each application of the brakes, with adjustment taking place during the release stroke when the un is not under load.
To understand how the ai juster works, let's go back an enlarge upon the problem why adjustment is necessary the first place. As the brakes al used, the friction materii making up the linings wea away which has the effect 1 increasing very, very gradual the clearance between th linings and the drum. The tray Of the actuating brake cylindi push rod is not related to or factor only; it can be divided ini three parts.
C — the clearance tray, which corresponds to the no mal clearance between th lining and the drum as set by if
an acturer; — the excessive travel
hi corresponds to the exe clearance caused by iii wear;
the elasticity travel is due to the elasticity in urn, linings, shoes and all her parts concerned with itting the force between ake unit and the foundaake.
normal clearance is deed by the machined notch the control ring. If this mended clearance is exd. the lower side of the pushes against the rack d moves it upwards. As ck moves, it turns the heel (C) which is part of a ay clutch assembly. At ge, the clutch slips in this on.
en the lining comes up t the drum and the system the elasticity region, the wormscrew (D) is pushed axially against the coil spring (E), at the same time disengaging from the one-way clutch assembly.
Now we come to the actual adjusting part — on the return stroke. When the brakes are released, the one-way clutch is re-engaged by the wormscrew at the end of the elasticity travel. After the brake actuating rod has returned through the clearance travel and during the completion of the return stroke through the excess due to wear, the upper side, this time of the control ring notch, pulls the rack back down.
The rack then rotates the gear wheel which — because the clutch only operates one way — turns the wormscrew at the same time. At the wormscrew meshes directly with the wormwheel, the latter is turned, acting on the S-cam and so adjusting the brakes. As men tioned earlier, this is a constant process, but if there is a large excessive clearance initially (due to, say, under-adjustment after a lining change) then the SAB will take this up in 10 per cent steps.
A useful extra provided by SAB is a visual lining wear indicator, which saves scrambling about underneath the vehicle. It fits directly on the S-cam shaft and as the brakes are adjusted, it rotates with the shaft. The indicator is set to be vertical with new linings so when it has moved through 90 it is time for an inspection.
Savings A well-adjusted brake is an obvious asset to road safety but SAB claims that it is a useful cost-reducing component-as well.
If we take a tandem axle trailer to illustrate the point, then the initial cost of the adjusters will be in the region of C2120. Suppose we consider a five-year period and do a few sums related to maintenance costs, then we get some interesting answers.
With the SAB adjuster, there is an obvious saving in labour because of the elimination of manual adjustment. The lining wear indicator should remove any need for drum replacement due to linings wearing down to the rivets. Although the odd chamber diaphragm will still probably need replacing during the normal course of events, the SAB — by maintaining a constant stroke — should decrease the number of diaphragms needed due to excessive flexing.
Balancing up all these variables, SAB reckons that the operator can save around £200 per trailer over a five-year period.
The maintenance requirements of the SAB adjuster are not exactly lengthy or complicated — merely a quick greasegun job every 24,000 to 32,000km (15,000 to 20,000 miles)! The units can in fact be supplied ready tapped for coupling to an automatic lubrication system.
A garage wall chart is available from SAB gaving full details of setting-up procedure, service instructions, fault finding etc. and this can be obtained free of charge from Howden Way, Aycliffe Industrial Estate, Darlington.
The future
So why doesn't every operator have automatic slack adjusters fitted? Good question. According to SAB, the operators don't want to pay the extra but with a new tractive unit selling for over C-220,000 in many cases, the extra initial outlay looks rather small.
At the moment there is no sign that regulations within the EEC will make automatic adjustment mandatory. It is mandatory in Sweden that the manufacturers fit something of the sort, as Swedish regulations require that the operating stroke must be kept constant. Whether other countries will follow the Swedish lead is still a matter for conjecture.
• Graham Montgomerie