ise brake is not
Page 43
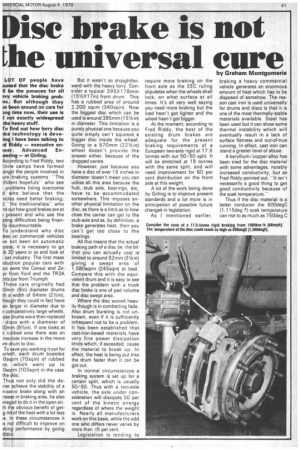
Page 44
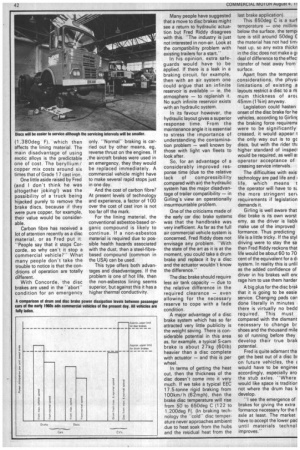
If you've noticed an error in this article please click here to report it so we can fix it.
e universal ff.!. Graham L T OF people have ;urrd that the disc brake II e the panacea for all 3vy vehicle braking probns. But although they ire been around on cars for )ng time now, their use is 11 nt exactly widespread th heavy stuff.
To ind out how lorry disc ik technology is develin I have been talking to KI Riddy — executive en
lee , Advanced Eniee ing — at Girling.
Acc rding to Fred Riddy, two 'ini e camps have formed on St the people involved in ure braking systems. The -did nt hopefuls' who see i pr blems being overcome
d ho believe that the licles need better braking;
he traditionalists'. who nt C ut how good brakes are at i pr sent and who see the stir' difficulties being finanIly i surmountable.
To understand why disc ikes on commercial vehicles ye ot been an automatic ces , it is necessary to go .:k 2 years or so and look at i ca industry. The first mass )du tion popular cars with cs were the Consul and Zeyr from Ford and the TR3A arts ar from Triumph.
Th se cars originally had :Om (9in) diameter drums th a width of 64mrn (21/2in), h they could in fact have rger in diameter due to paratively large wheels. rums were then replaced cs with a diameter of
(91/2in). If one looks at bed area there was an iate increase in the move urn to disc.
ave you working it out for It, each drum boasted m (70sqin) of rubbed which went up to m (102sgin) in the case isc.
hou en I 3 co ese di [Om .?„ ru me im d To urs Osq Osq the Thus not only did the detier chieve the stability of a n-se vo brake along with an ;rea in braking area, he also inag d to do it in the open air, th th obvious benefit of getrid of the heat with a lot less ;s. I these circumstances it is n t difficult to improve on kin performance by going disc
But it wasn't so straightforward with the heavy lorry. Consider a typical 395X 178mm (151/2X17in) front drum_ This has a rubbed area of around 2,200 sqcm (340sqin). Now the biggest disc which can be used is around 395mm (151/2in) in diameter. This limitation is a purely physical one because you quite simply can't squeeze a bigger disc inside the wheel. Going to a 570mm (221/2in) wheel doesn't provide the answer either, because of the dropped centre.
However, just because you have a disc of over 15 inches in diameter doesn't mean you can utilise all-this area because the hub, stub axle, bearings, etc, have to be accommodated somewhere. This imposes another physical limitation on the disc, as there is a limit as to how close the carrier can get to the stub axle and as, by definition, a brake generates heat, then you can't get too close to the bearings.
All this means that the actual braking path of a disc (ie, the bit that you can actually use) is' limited to around 82mm (31/4in) giving a swept area of 1,580sqcm (245sgin) at best. Compare this with the equivalent drum and it is easy to see that the problem with a truck disc brake is one of pad volume and disc swept area.
Where the disc scored heavily though is in combatting fade. Also drum bursting is not unknown, even if it is sufficiently infrequent not to be a problem. It has been established that cast-iron-based materials, have very fine power dissipation limits which, if exceeded, cause the material to break up. In effect, the heat is being put into the drum faster than it can be got out.
In normal circumstances a braking system is set up for a certain split, which is usually 50/50. Thus with a two-axle vehicle, the axle under consideration will dissipate 50 per cent of the kinetic energy regardless of where the weight is. Nearly all manufacturers work on this basis, while the odd one who differs never varies by more than ±5 per cent.
Legislation is tending to require more braking on the front axle as the EEC ruling stipulates when the wheels shall lock, on what surface at all times. It's all very well saying you need more braking but the load hasn't got lighter and the wheel hasn't got bigger.
At the moment, according to Fred Riddy, the best of the existing drum brakes are adequate for the present braking requirements of a European two-axle rigid at 17.5 tonnes with our 50/50 split, it will be stretched at 19 tonnes with the same split, and will need improvement for 60 per cent distribution on the front axle at this weight.
A lot of the work being done by Girling is to improve present standards and a lot more is in anticipation of possible future change's in legislation.
As I mentioned earlier, braking a heavy commercial vehicle generates an enormous amount of heat which has to be disposed of somehow. The reason cast iron is used universally for drums and discs is that it is one of the most thermally stable materials available. Steel has been used but it can show some thermal instability which will eventually result in a lack of surface flatness and out-of-true running. In effect, cast iron can stand a greater level of abuse.
A beryllium/copper alloy has been tried for the disc material with some advantages, notably increased conductivity, but as Fred Riddy pointed out, "It isn't necessarily a good thing to get good conductivity because of the soak temperature."
Thus if the disc material is a better conductor the 600degC (1,115deg F) soak temperature can rise to as much as 750deg C (1,380deg F), which then affects the lining material. The main disadvantage of using exotic alloys is the predictable one of cost. The beryllium / copper mix costs around six times that of Grade 17 cast iron.
One little aside raised by Fred (and I don't think he was altogether joking!) was the possibility of a truck being hijacked purely to remove the brake discs, because if they were pure copper, for example, their value would be considerable.
Carbon fibre has received a lot of attention recently as a disc material, or as Fred put it. "People say that it stops Corcorde, so why can't it stop a commercial vehicle?" What many people don't take the trouble to notice is that the conditions of operation are 'totally different.
With Concorde, the disc brakes are used in the "abort" condition for an emergency only. "Normal" braking is carried out by other means, eg, reverse thrust on the engines. If ,the aircraft brakes were used in an emergency, they they would be replaced immediately. A commercial vehicle might have to make several rapid stops just in one day.
And the cost of carbon fibre? At present levels of technology and experience, a factor of 100 over the cost of cast iron is not too far off the mark.
For the lining material, the conventional asbestos-based organic compound is likely to continue. If a non-asbestos material is required due to possible health hazards associated with the dust, then a steel-fibrebased compound (common in the USA) can be used.
This type offers both advantages and disadvantages. If the problem is one of hot life, then the non-asbestos lining seems superior, but against this it has a higher thermal conductivity. Many people have suggested that a move to disc brakes might see a return to hydraulic actuation but Fred Riddy disagrees with this. "The industry is just not interested in non-air. Look at the compatibility problem with existing trailers for a start."' In his opinion, extra safeguards would have to be applied. If there is a leak in a braking circuit, for example, then with an air system one could argue that an infinite reservoir is available — ie, the atmosphere — to replenish it. No such infinite reservoir exists with an hydraulic system.
In its favour however, the hydraulic layout gives a superior response time. From the maintenance angle it is essential to stress the importance of understanding the contamination problem — well known by those with light van fleets to look after.
So, for an advantage of a considerably improved response time (due to the relative lack of compressibility compared with air) the hydraulic system has the major disadvantage of trailer compatibility — in Girling's view an operationally insurmountable problem.
One of the criticisms made of the early car disc brake systems was that the handbrake was very inefficient. As far as the full air commercial vehicle system is concerned, Fred Riddy does not envisage any problem "With the state of the art as it is at the moment, you could take a drum brake and replace it by a disc and the actuator wouldn't know the difference."
The disc brake should require less air tank capacity — due to the relative difference in the required clearance — even allowing for the necessary reserve to cope with a fade condition.
A major advantage of a disc brake system which has so far attracted very little publicity is the weight saving. There is considerable potential in this area as, for example, a typical S-cam brake is about 27kg (60Ib) heavier than a disc complete with actuator — and this is per wheel.
In terms of getting the heat out, then the thickness of the disc doesn't come into it very much. If we take a typical EEC 17.5-tonne rigid braking from 100km/ h (62mph), then the brake disc temperature will rise from 50 to 650deg C (122 to 1,200deg F(. (In braking technology the "colddisc temperature never approaches ambient due to heat soak from the hubs and the residual heat from the
last brake application).
This 650deg C is a surf temperature — one minim( below the surface, the tempi ture is still around 50deg C the material has not had timr heat up, so any extra thickn in the disc does not make a gr deal of difference to the effec. transfer of heat away from surface.
Apart from the temperat considerations, the physi limitations of existing a layouts restrict a disc to a m mum thickness of aroi 45mm (1 3/4in) anyway.
Legislation could hasten onset of the disc brake for he vehicles, according to Girlinc the braking force requiremE were to be significantly creased, it would appear 1 the only way out is to gc discs, but with the rider thr higher standard of inspeci would be required, as well a: operator acceptance of creasing service intervals.
The difficulties with exis. technology are pad life and life, which means t the operator will have to the more stringent sen, requirements if legislation demands it.
Girling is well aware that disc brake is its own worst emy, as the driver is liablE make use of the improved formance. Thus predicting life is a little tricky. If the styl driving were to stay the sa then Fred Riddy reckons that life would be about 60 to 70 cent of the equivalent for a di system. In reality this is unlil as the added confidence of driver in his brakes will enc rage him to use them harder
A big plus for the disc bra it that it is going to be easie service. Changing pads can done literally in minutes , there is virtually no bedd required. This must compared with the dismant necessary to change br shoes and the thousand mile so of running before they develop their true brak potential.
Fred is quite adamant tha. get the best out of a disc br on future vehicles, the z would have to be enginee accordingly, especially aro the stub axles. "Where would like space is tradition not where the drum has IE develop.
'I see the emergence of brakes for giving the extra formance necessary for the fr axle at least. The market have to accept the lower pad until materials technol improves."