Designers set their eyes on distant horizont
Page 68
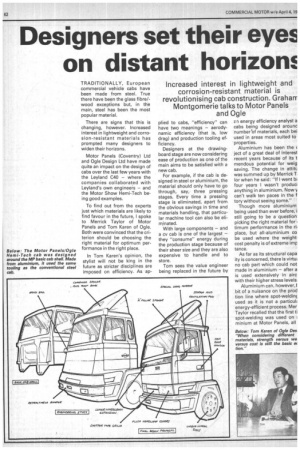
Page 69
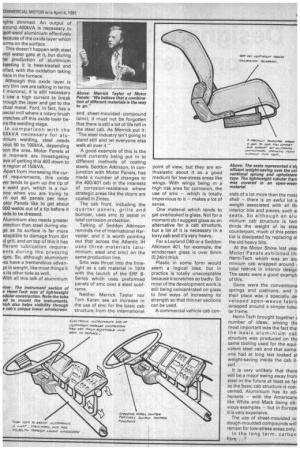
If you've noticed an error in this article please click here to report it so we can fix it.
TRADITIONALLY, European commercial vehicle cabs have been made from steel. True there have been the glass fibre/wood exceptions but, in the main, steel has been the most popular material.
There are signs that this is changing, however. Increased interest in lightweight and corrosion-resistant materials has prompted many designers to widen their horizons.
Motor Panels (Coventry) Ltd and Ogle Design Ltd have made quite an impact on the design of cabs over the last few yearswith the Leyland C40 — where the companies collaborated with Leyland's own engineers — and the Motor Show Hemi-Tech being good examples.
To find out from the experts just which materials are likely to find favour in the future, I spoke to Merrick Taylor of Motor Panels and Tom Karen of Ogle. Both were convinced that the criterion should be choosing the right material for optimum performance in the right place.
In Tom Karen's opinion, the stylist will not be king in the future as stricter disciplines are imposed on efficiency. As ap
plied to cabs, "efficiency" can have two meanings — aerodynamic efficiency (that is, low drag) and production tooling efficiency.
Designers at the drawingboard stage are now considering ease of production as one of the main aims to be satisfied with a new cab.
For example, if the cab is designed in steel or aluminium, the material should only have to go through, say, three pressing stages. Every time a pressing stage is eliminated, apart from the obvious savings in time and materials handling, that particular machine tool can also be eliminated.
With large components — and a cv cab is one of the largest — they "consume" energy during the production stage because of their sheer size and they are also expensive to handle and to store.
Tom sees the value engineer being replaced in the future by
Ei energy efficiency analyst a cabs being designed arounc number 'of materials, each bei used in areas most suited to
properties.
Aluminium has been the ( ject of a great deal of interest recent years because of its t mendous potential for weig saving. The change in attitu was summed up by Merrick T. lor when he said: "If I went LN four years I wasn't produci anything in aluminium. Now y can't walk ten paces in the f tory without seeing some."
Though more aluminium being used than ever before, i still going to be a question picking the right material for timum performance in the rii place, but all-aluminium co be used where the weight. cost penalty is of extreme imp tan ce.
As far as its structural capa ity is concerned, there is virtui no cab part which could not made in aluminium — after a is used extensively in airc with their higher stress levels.
Aluminium can, however,t bit of a nuisance on the prod tion line where spot-weldinc used as it is not a particuk energy-efficient process. Mer Taylor recalled that the first ti spot-welding was used on i minium at Motor Panels, all ights dimmed. An output of mound 400kVA is necessary to ;pot-weld aluminium effectively )ecause of the oxide layer which orms on the surface.
This doesn't happen with steel intil water gets at it, but during he production of aluminium heeting it is heat-treated and oiled, with the oxidation taking dace in the furnace.
Although this oxide layer is ery thin (we are talking in terms f microns), it is still necessary use a high current to break irough the layer and get to the ctual metal. Ford, in fact, has a pecial mill where a rotary brush ...ratches off this oxide layer bere the welding stage.
In corn parison with the 00kVA necessary for alulinium welding, steel needs out 50 to 100kVA, depending Don the area. Motor Panels at le moment are investigating ays of getting this 400 down to e region of 150kVA.
Apart from increasing the curnt requirements, this oxide ver tends to gum up the tip of e weld gun, which is a nui nce when you are trying to rn out 80 panels per hour.
otor Panels like to get about 000 welds out of a tip before it .:eds to be dressed.
Aluminium also needs greater otection than steel during stoge as its surface is far more sceptible to damage from dirt d grit, and on top of this it has fferent lubrication requireents during the pressing 3ges. So, although aluminium les have a tremendous advan)e in weight, like most things it s its other side as well.
With all this talk of aluminium and sheet-moulded compound (smc), it must not be forgotten that there is still a lot of life left in the steel cab. As Merrick put it: "The steel industry isn't going to stand still and let everyone else walk all over it."
A good example of this is the work currently being put in to different methods of coating steels. Seddon Atkinson, in conjunction with Motor Panels, has made a number of changes to the 400/401 cab in the interests of corrosion-resistance where strategic areas like the doors are coated in Zintec.
The cab front, including the quarter panels, grille and bumper, uses smc to assist in total corrosion protection.
Talking of Seddon Atkinson reminds me of International Harvester, and it is worth pointing out that across the Atlantic IH uses three materials (aluminium, steel and smc) on the same production line.
Smc was thrust into the limelight as a cab material in 1974 with the launch of the ERF BSeries which uses preformed panels of smc over a steel subframe.
Neither Merrick Taylor nor Tom Karen see an increase in the use of smc for the basic cab structure from the international point of view, but they are enthusiastic about it as a good medium for low-stress areas like wings. With wings being in a high risk area for corrosion, the use of smc — which is totally impervious to it — makes a lot of sense.
One material which tends to get overlooked is glass. Not for a moment do I suggest glass as an alternative for a cab structure, but a lot of it is necessary in a lorry cab and it's very heavy.
For a Leyland C40 or a Seddon Atkinson 401, for example, the windscreen glass is over 6mm (0.24in) thick.
Plastic in some form would seem a logical idea, but in practice is totally unacceptable because it scratches so badly. So most of the development work is still being concentrated on glass to find ways of increasing its strength so that thinner sections can be used.
A commercial vehicle cab con sists of a lot more than the meta shell — there is an awful lot o weight associated with all thi interior bits and pieces, such a: seats. So although an alu minium cab structure is two thirds the weight of its stee counterpart, much of this poten tial is dissipated by replacing al the old heavy bits.
At the Motor Show last year Motor Panels exhibited till Hemi-Tech which was an alu minium cab wrapped around total rethink in interior design The seats were a good examplc of this.
Gone were the conventiona springs and cushions, and ir their place was a specially de veloped open-weave fabric wrapped around a simple tubu. lar frame.
Hemi-Tech brought together E number of ideas; among the most important was the fact that the basic aluminium caL structure was produced on the same tooling used for the equivalent steel cab and that someone had at long last looked at weight-saving inside the cab itself.
It is very unlikely that there will be a major swing away from steel in the future at least as far as the basic cab structure is concerned. Aluminium has its adherents — with the Americans like White and Mack being obvious examples but in Europe it is very expensive.
The use of sheet-moulded or dough-moulded compounds will remain for low-stress areas only. In the long term, carbon fibre. , ?