Tough work needs trained men
Page 60
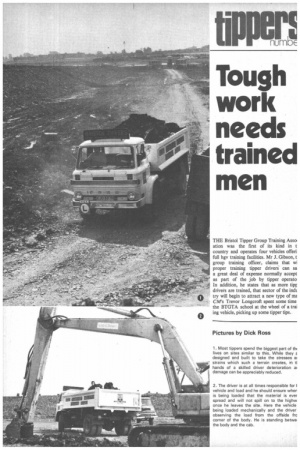
Page 61
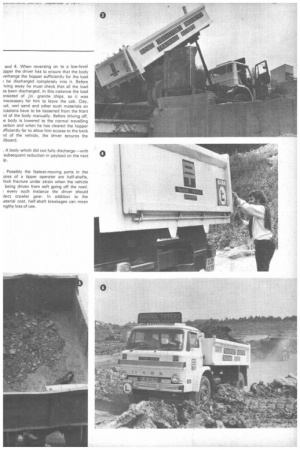
Page 62
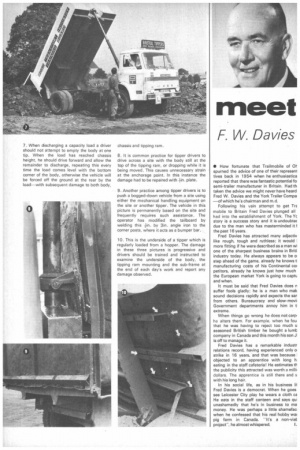
If you've noticed an error in this article please click here to report it so we can fix it.
THE Bristol Tipper Group Training Asso ation was the first of its kind in t country and operates four vehicles offeri full hgv training facilities. Mr J. Gibson, t group training officer, claims that wi proper training tipper drivers can sa a great deal of expense normally accept as part of the job by tipper operato In addition, he states that as more tipr drivers are trained, that sector of the indt try will begin to attract a new type of am CM's Trevor Longcroft spent some time the BTGTA school at the wheel of a trai ing vehicle, picking up some tipper tips.
Pictures by Dick Ross
1. Most tippers spend the biggest part of thi lives on sites similar to this. While they z designed and built to take the stresses ai strains which such a terrain creates, in tl hands of a skilled driver deterioration at damage can be appreciably reduced.
2. The driver is at all times responsible for I vehicle and load and he should ensure whef is being loaded that the material is ever spread and will not spill on to the highw once he leaves the site. Here the vehicle being loaded mechanically and the driver observing the load from the offside frc corner of the body. He is standing betwa the body and the cab. and 4. When reversing on to a low-level 3pper the driver has to ensure that the body verhangs the hopper sufficiently for the load ) be discharged completely into it, Before -lying away he must check that all the load as been discharged. In this instance the load insisted of ;in. granite chips, so it was inecessary for him to leave the cab. Clay, ■ ud, wet sand and other such materials on :casions have to be loosened from the front id of the body manually. Before driving off, ie body is lowered to the normal travelling psition and when he has cleared the hopper ifficiently far to allow him access to the back id of the vehicle, the driver secures the ilboard.
. A body which did not fully discharge—with subsequent reduction in payload on the next ip.
. Possibly the fastest-moving parts in the ores of a tipper operator are half-shafts, 'filch fracture under strain when the vehicle being driven from soft going off the road. every such instance the driver should :lect crawler gear. In addition to the iaterial cost, half-shaft breakages can mean ngthy toss of use. 7. When discharging a capacity load a driver should not attempt to empty the body at one tip. When the load has reached chassis height, he should drive forward and allow the remainder to discharge, repeating this every time the load comes level with the bottom corner of the body, otherwise the vehicle will be forced off the ground at the rear by the load—with subsequent damage to both body, chassis and tipping ram.
8. It is common practice for tipper drivers to drive across a site with the body still at the top of the tipping ram. or dropping while it is being moved. This causes unnecessary strain at the anchorage point. In this instance the damage had to be repaired with lin. plate.
9. Another practice among tipper drivers is to push a bogged-down vehicle from a site using either the mechanical handling equipment on the site or another tipper. The vehicle in this picture is permanently based on the site and frequently requires such assistance. The operator has modified the tailboard by welding this in. by 3in. angle iron to the corner posts, where it acts as a bumper bar.
10. This is the underside of a tipper which is regularly loaded from a hopper. The damage in these three pictures is progressive and drivers should be trained and instructed to examine the underside of the body, the tipping ram mounting and the sub-frame at the end of each days work and report any damage observed.