How industry profits from military trials
Page 76
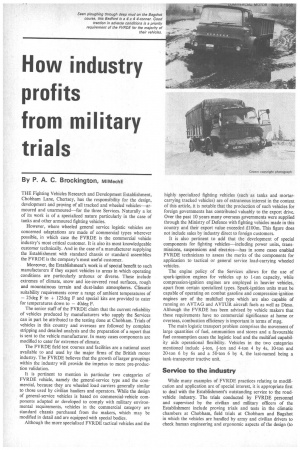
Page 77
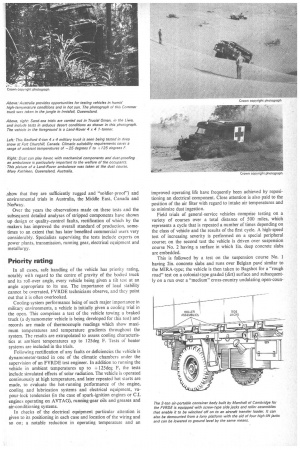
Page 78
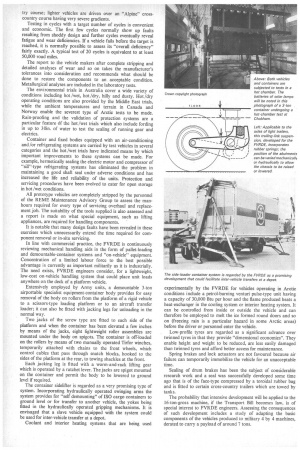
If you've noticed an error in this article please click here to report it so we can fix it.
By P. A. C. Brockington, MIMechE
THE Fighting Vehicles Research and Development Establishment, Chobham Lane, Chertsey, has the responsibility for the design, development and proving of all tracked and wheeled vehicles—armoured and unarmoured—for the three Services. Naturally a lot of its work is of a specialized nature particularly in the case of tanks and other armoured fighting vehicles.
However, where wheeled general service logistic vehicles are concerned adaptations are made of commercial types wherever possible, in which case the FVRDE is the commercial vehicle industry's most critical customer. It is also its most knowledgeable customer technically. And in the case of a manufacturer supplying the Establishment with standard chassis or standard assemblies the FVRDE is the company's most useful customer.
Moreover, the Establishment's work is of special benefit to such manufacturers if they export vehicles to areas in which operating conditions are particularly arduous or diverse. These include extremes of climate, snow and ice-covered road surfaces, rough and mountainous terrain and dust-laden atmospheres. Climatic suitability requirements cover a range of ambient temperatures of — 25deg F to + 125deg F and special kits are provided to cater for temperatures down to — 40deg F.
The senior staff of the FVRDE claim that the current reliability of vehicles produced by manufacturers who supply the Services can in part be attributed to the testing done at Chobham. Trials of vehicles in this country and overseas are followed by complete stripping and detailed analysis and the preparation of a report that is sent to the vehicle manufacturer. In many cases components are modified to cater for extremes of climate.
The FVRDE field test courses and facilities are a national asset available to and used by the major firms of the British motor industry. The FVRDE believes that the growth of larger groupings within the industry will provide the impetus to more pre-production validation.
It is pertinent to mention in particular two categories of FVRDE vehicle, namely the general-service type and the commercial, because they are wheeled load carriers generally similar to those used by civilian hauliers and operators. While the design of general-service vehicles is based on commercial-vehicle components adapted or developed to comply with military environmental requirements, vehicles in the commercial category are standard chassis purchased from the makers, which may be modified in detail and are equipped with special bodies.
Although the more specialized FVRDE tactical vehicles and the highly specialized fighting vehicles (such as tanks and mortarcarrying tracked vehicles) are of extraneous interest in the context of this article, it is notable that the production of such vehicles for foreign governments has contributed valuably to the export drive. Over the past 10 years many overseas governments were supplied through the Ministry of Defence with fighting vehicles made in this country and their export value exceeded £100m. This figure does not include sales by industry direct to foreign customers.
It is also pertinent to add that the development of special components for fighting vehicles—including power units,. transmissions, suspensions and electrics—has in some cases enabled FVRDE technicians to assess the merits of the components for application to tactical or general service load-carrying wheeled vehicles.
The engine policy of the Services allows for the use of spark-ignition engines for vehicles up to 1-ton capacity, while compression-ignition engines are employed in heavier vehicles, apart from certain specialized types. Spark-ignition units must be capable of operating on combat gasoline and compression-ignition engines are of the multifuel type which are also capable of running on AVTAG and AVTUR aircraft fuels as well as Dieso. Although the FVRDE has been advised by vehicle makers that these requirements have no commercial significance at home or overseas, combustion efficiency is important in terms of mpg.
The main logistic transport problem comprises the movement of large quantities of fuel, ammunition and stores and a favourable fuel consumption eases the logistic load and the multifuel capability aids operational flexibility. Vehicles in the two categories mentioned include fton, +-ton and 4-ton 4 by 4s, 10-ton and 20-ton 6 by 6s and a 50-ton 6 by 4, the last-named being a tank-transporter tractive unit.
Service to the industry
While many examples of FVRDE practices relating to modification and application are of special interest, it is appropriate first to deal with the Establishment's outstanding service to the roadvehicle industry. The trials conducted by FVRDE personnel and supervised by the civilian and military officers of the Establishment include proving trials and tests in the climatic chambers at Chobham, field trials at Chobham and Bagshot in which the vehicles are handled by army and civilian drivers to check human engineering and ergonomic aspects of the design (to ..show that they are sufficiently rugged and "soldier-proof") and environmental trials in Australia, the Middle East, Canada and NofWa y.
Over the years the observations made on these tests and the subsequent detailed analyses of stripped components have shown up design or quality-control faults, rectification of which by the makers has improved the overall standard of production, sometimes to an extent that has later benefited commercial users very considerably. Specialists supervising the tests include experts on power plants, transmission, running gear, electrical equipment and metallurgy.
Priority rating
In all cases, safe handling of the vehicle has priority rating, notably with regard to the centre of gravity of the bodied truck and its roll-over angle, every vehicle being given a tilt test at an angle appropriate to its use. The importance of load stability cannot be overrated, FVRDE technicians observe, and they point out that it is often overlooked.
Cooling-system performance being of such major importance in military environments, a vehicle is initially given a cooling trial in the open. This comprises a test of the vehicle towing a braked truck (a dynamometer vehicle is being developed for this test) and records are made of thermocouple readings which show maximum temperatures and temperature gradients throughout the system. The results are extrapolated to assess cooling characteristics at ambient temperatures up to 125deg F. Tests of heater systems are included in the trials.
Following rectification of any faults or deficiencies the vehicle is dynamometer-tested in one of the climatic chambers under the supervision of an FVRDE test engineer. In addition to running the vehicle in ambient temperatures up to ÷125deg F, the tests include simulated effects of solar radiation. The vehicle is operated continuously at high temperature, and later repeated hot starts are made, to evaluate the hot-running performance of the engine, cooling and lubrication systems and electrical equipment, vapour-lock tendencies (in the case of spark-ignition engines or C.I. engines operating on AVTAG), running-gear oils and greases and air-conditioning systems.
In checks of the electrical equipment particular attention is given to its positioning in each case and location of the wiring and so on; a notable reduction in operating temperature and an improved operating life have frequently been achieved by repositioning an electrical component. Close attention is also paid to the position of the air filter with regard to intake air temperatures and to minimize dust ingestion.
Field trials of general-service vehicles comprise testing on a variety of courses over a total distance of 500 miles, which represents a cycle that is repeated a number of times depending on the class of vehicle and the results of the first cycle. A high-speed test of increasing severity is performed on a special peripheral course; on the second test the vehicle is driven over suspension course No. 2 having a surface in which lin. deep concrete slabs are embedded.
This is followed by a test on the suspension course No 1 having 2in. concrete slabs and runs over Belgian pavi similar to the MIRA-type; the vehicle is then taken to Bagshot for a "rough road" test on a colonial-type graded (dirt) surface and subsequently on a run over a "medium" cross-country undulating open-coun try course; lighter vehicles are driven over an "Alpine" crosscountry course having very severe gradients.
Testing in cycles with a target number of cycles is convenient and economic. The first few cycles normally show up faults resulting from shoddy design and further cycles eventually reveal fatigue and wear deficiencies. If a vehicle fails before the target is reached, it is normally possible to assess its "overall deficiency" fairly exactly. A typical test of 20 cycles is equivalent to at least 50,000 road miles.
The report to the vehicle makers after complete stripping and detailed analyses of wear and so on takes the manufacturer's tolerances into consideration and recommends what should be done to restore the components to an acceptable condition. Metallurgical analyses are included in the laboratory tests.
The environmental trials in Australia cover a wide variety of conditions including hot /wet, hot /dry, hilly and dusty. Hot /dry operating conditions are also provided by the Middle East trials, while the ambient temperatures and terrain in Canada and Norway enable the severest type of Arctic tests to be made. Rain-proofing and the validation of protection systems are a particular feature Of the hot /wet trials which also include fording in up to 30in. of water to test the sealing of running gear and electrics.
Container and fixed bodies equipped with an air-conditioning and/or refrigerating systems are carried by test vehicles in several categories and the hot /wet trials have indicated means by which important improvements to these systems can be made. For example, hermetically sealing the electric motor and compressor of "sill"-type refrigerating systems has eliminated the problem in maintaining a good shaft seal under adverse conditions and has increased the life and reliability of the units. Protection and servicing procedures have been evolved to cater for open storage in hot /wet conditions.
All prototype vehicles are completely stripped by the personnel of the REME Maintenance Advisory Group to assess the manhours required for every type of servicing overhaul and replacement job. The suitability of the tools supplied is also assessed and a report is made on what special equipment, such as lifting appliances, are required for handling components.
It is notable that many design faults have been revealed in these exercises which unnecessarily extend the time required for cornponent removal or in-situ servicing.
In line with commercial practice, the FVRDE is continuously reviewing mechanical handling aids in the form of pallet-loading and demountable-container systems and "on-vehicle" equipment. Concentration of a limited labour force to the best possible advantage is currently as important militarily as it is industrially. The need exists, FVRDE engineers consider, for a lightweight, low-cost on-vehicle handling system that could place unit loads anywhere on the deck of a platform vehicle.
Extensively employed by Army units, a demountable 3-ton airportable specialist equipment-container body provides for easy removal of the body on rollers from the platform of a rigid vehicle to a scissors-type loading platform or to an aircraft transfer loader; it can also be fitted with jacking legs for unloading in the normal way.
Two jacks of the screw type are fitted to each side of the platform and when the container has been elevated a few inches by means of the jacks, eight lightweight roller assemblies are mounted under the body on spigots. The container is off-loaded on the rollers by means of two manually operated Tirfor winches, temporarily attached with chains to the front wheels, which control cables that pass through snatch blocks, hooked to the sides of the platform at the rear, to towing shackles at the front.
Each jacking leg is fitted with a worm-and-rack lifting gear which is operated by a ratchet lever. The jacks are spigot mounted on the container and permit the body to be lowered to ground level if required.
The container sidelifter is regarded as a very promising type of system. Incorporating hydraulically operated swinging arms the system provides for "self demounting" of ISO cargo containers to ground level or for transfer to another vehicle, the yokes being fitted in the hydraulically operated gripping mechanisms. It is envisaged that a slave vehicle equipped with the system could be used for inter-vehicle transfer at a depot.
Coolant and interior heating systems that are being used experimentally by the FVRDE for vehicles operating in Arctic conditions include a petrol-burning venturi pulse-type unit having a capacity of 30,000 Btu per hour and the flame produced heats a heat-exchanger in the cooling system or interior heating system. It can be controlled from inside or outside the vehicle and can therefore be employed to melt the ice formed round doors and so on (freezing rain is a particular hazard in some Arctic areas) before the driver or personnel enter the vehicle.
Low-profile tyres are regarded as a significant advance over twinned tyres in that they provide "dimensional economies". They enable height and weight to be reduced, are less easily damaged than twinned tyres and afford better access for maintenance.
Spring brakes and lock actuators are not favoured because air failure can temporarily immobilize the vehicle for an unacceptable time.
Sealing of drum brakes has been the subject of considerable research work and a seal was successfully developed some time ago that is of the face-type compressed by a toroidal rubber bag and is fitted to certain cross-country trailers which are towed by tanks.
The probability that intensive development will be applied to the 16-ton-gross machine, if the Transport Bill becomes law, is of special interest to FVRDE engineers. Assessing the consequences of such development includes a study of adapting the basic components of the vehicles produced to military 4 by 4 machines, derated to carry a payload of around 7 tons.