Sam Buckley on
Page 167
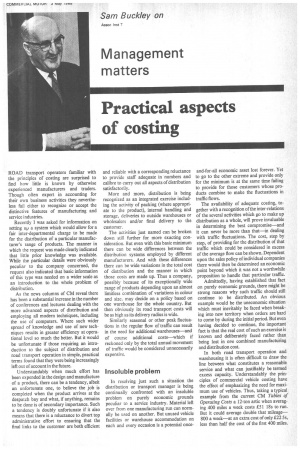
Page 168
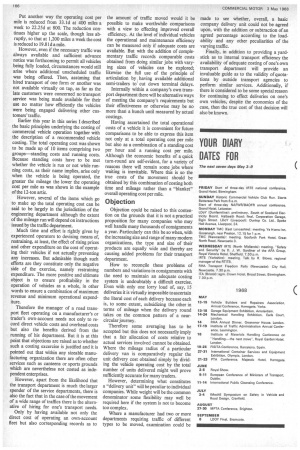
If you've noticed an error in this article please click here to report it so we can fix it.
Assoc lost T
Management matters
Practical aspects of costing
ROAD transport operators familiar with the principles of costing are surprised to find how little is known by otherwise experienced manufacturers and traders. Though often expert in accounting for their own business activities they nevertheless fail either to recognize or accept the distinctive features of manufacturing and service industries.
Recently I was asked for information on setting up a system which would allow for a fair inter-departmental charge to be made for the distribution of a particular manufacturer's range of products. The manner in which the request was made clearly indicated that little prior knowledge was available. While the particular details were obviously peculiar to the company concerned, the request also indicated that basic information of this type was needed on a wider scale as an introduction to the whole problem of distribution.
As the news columns of CM reveal there has been a substantial increase in the number of conferences and lectures dealing with the more advanced aspects of distribution and employing all modern techniques, including the use of computers. Where such wider spread of knowledge and use of new techniques results in greater efficiency at operational level so much the better. But it would be unfortunate if those requiring an introduction to the subject of distribution and road transport operation in simple, practical terms found that they were being increasingly left out of account in the future.
Understandably when much effort has been expended in the design and manufacture of a product, there can be a tendency, albeit an unfortunate one, to believe the job is completed when the product arrives at the despatch bay and what, if anything, remains to be done is of secondary importance. Such a tendency is doubly unfortunate if it also means that there is a reluctance to divert top administrative effort to ensuring that the final links to the customer are both efficient and reliable with a corresponding reluctance to provide staff adequate in numbers and calibre to carry out all aspects of distribution satisfactorily.
More and more, distribution is being recognized as an integrated exercise including the activity of packing (where appropriate to the product), internal handling and storage, deliveries to outside warehouses or wholesalers and/or final delivery to the customer.
The activities just named can be broken down still further for more exacting consideration. But even with this basic minimum there can be wide differences between the distribution systems employed by different manufacturers. And with these differences there can be wide variations in the total cost of distribution and the manner in which those costs are made up. Thus a company, possibly because of its exceptionally wide range of products depending upon an almost limitless combination of variations in colour and size. may decide on a policy based on one warehouse for the whole country. But then obviously its road transport costs will be as high as its delivery radius is wide.
Similarly seasonal or other peak fluctuations in the regular flow of traffic can result in the need for additional warehouses—and of course additional costs—which if reckoned only by the total annual movement of traffic would be considered unnecessarily expensive.
Insoluble problem In resolving just such a situation the distribution or transport manager is being continually confronted with an insoluble problem on purely economic grounds peculiar to a service industry. Material left over from one manufacturing run can normally be used on another. But unused vehicle facilities or warehouse accommodation on each and every occasion is a potential once
and-for-all economic asset lost forever. Yet to go to the other extreme and provide only for the minimum is at the same time failing to provide for those customers whose products combine to make the fluctuations in traffic flows.
The availability of adequate costing, together with a recognition of the inter-relations of the several activities which go to make up distribution as a whole, will prove invaluable in determining the best compromise—and it can never be more than that—in dealing with traffic fluctuations. The cost, step by step, of providing for the distribution of that traffic which could be considered in excess of the average flow can be shown. Dependent upon the sales policy of individual companies there would then be determined an economic point beyond which it was not a worthwhile proposition to handle that particular traffic.
Admittedly, having established that fact on purely economic grounds, there might be strong reasons why such traffic should still continue to be distributed. An obvious example would be the uneconomic situation which must inevitably be faced when breaking into new territory when orders are hard to come by during the initial period. But even having decided to continue, the important fact is that the real cost of such an exercise is known and deliberately faced rather than being lost in one combined manufacturing and distribution cost.
In both road transport operation and warehousing it is often difficult to draw the line between what constitutes a reasonable service and what can justifiably be termed excess capacity. Understandably the principles of commercial vehicle costing have the effect of emphasizing the need for maximum use of vehicles. Thus, taking a typical example from the current CM Tables of Operating Costs a 12-ton artic when averaging 400 miles a week costs £51 18s to run. But it could average double that mileage800 a week—at an extra cost of only £22 5s, less than half the cost of the first 400 miles. Put another way the operating cost per mile is reduced from 33.1d at 400 miles a week to 22.25d at 800. The reduction continues higher up the scale, though less abruptly, so that at 1,200 miles a week the cost is reduced to 19.81d a mile.
However, even if the necessary traffic was always available and sufficient advance notice was forthcoming to permit all vehicles being fully loaded, circumstances would still arise where additional unscheduled traffic was being offered. Then, assuming that hired transport of one form or another was not available virtually on tap, as far as the late customers were concerned no transport service was being made available for their use no matter how efficiently the vehicles were being engaged delivering other customers' traffic.
Earlier this year in this series I described the basic principles underlying the costing of commercial vehicle operation together with the description of a recommended vehicle costing. The total operating cost was shown to be made up of 10 items comprising two groups—standing costs and running costs. Because standing costs have to be met whether the vehicle is run or not while running costs, as their name implies, arise only when the vehicle is being operated, the greater the mileage the lower the operating cost per mile as was shown in the example of the 12-ton artic.
However, several of the items which go to make up the total operating cost can be said to be largely in the jurisdiction of the engineering department although the extent of the mileage run will depend on instructions issued by the traffic department.
Much time and effort is rightly given by experienced operators to devising means of, restraining, at least, the effeCt of rising prices and other expenditure on the cost of operating their vehicles if not actually preventing any increases. But admirable though such efforts are they constitute only the negative side of the exercise, namely restraining expenditure. The more positive and ultimate object is to ensure profitability in the operation of vehicles as a whole, in other words to ensure a combination of maximum revenue and minimum operational expenditure.
Therefore the manager of a road transport fleet operating on a manufacturer's or trader's own-account needs not only to record direct vehicle costs and overhead costs but also the benefits derived from the running of his department. But it is at this point that objections are raised as to whether such a costing excercise is justified and it is pointed out that within any sizeable manufacturing organization there are often other services such as canteens or sports grounds which are nevertheless not costed as independent enterprises.
However, apart from the likelihood that the transport department is much the larger spender of the service departments, there is also the fact that in the case of the movement of a wide range of traffics there is the alternative of hiring for one's transport needs.
Only by having available not only the direct cost of operating an own-account fleet but also corresponding records as to the amount of traffic moved would it be possible to make worthwhile comparisons with a view to effecting improved overall efficiency. At the level of individual vehicles the operational and maintenance efficiency can be measured only if adequate costs are available. But with the addition of complementary traffic records comparable costs obtained from doing similar jobs with varying sizes of vehicles can be explored; likewise the full use of the principle of articulation by , having available additional semi-trailers to cut down terminal delays.
Internally within a company's own transport department there will be alternative ways of meeting the company's requirements but their effectiveness or otherwise may be no more than a hunch until measured by actual costings.
Having ascertained the total operational costs of a vehicle it is convenient for future comparisons to be able to express this item not only at a total operating cost per mile but also as a combination of a standing cost per hour and a running cost per mile. Although the economic benefits of a quick turn-round are self-evident, for a variety of reasons there will remain some jobs where waiting is inevitable. Where this is so the true costs of the movement should be obtained by this combination of costing both time and mileage rather than a "blanket" overall operating cost per mile.
Objection
Objection could be raised to this contention on the grounds that it is not a practical proposition for many companies who may well handle many thousands of consignments a year.-Particularly can this be so when, with the increasing size and range of many modern organizations, the type and size of their products are equally wide and thereby are causing added problems for their transport department.
How to reconcile these problems of numbers and variations in consignments with the need to maintain an adequate costing system is undoubtably a difficult exercise. Even with only one lorry load of, say, 15 deliveries it is virtually impossible toascertain the literal cost of each delivery because each is, to some extent, subsidizing the other in terms of mileage when the delivery round takes on the common pattern of a nearcircular journey.
Therefore some averaging has to be accepted but this does not necessarily imply that a fair allocation of costs relative to actual services involved cannot be obtained. Where the mileage radius of a particular delivery van is comparatively regular the unit delivery cost obtained simply by dividing the vehicle operating cost by the total number of units delivered might well prove sufficiently accurate for many traders.
However, determining what constitutes a "delivery unit" will be peculiar to individual companies. While weight will be the common denominator some flexibility may well be required here if the system is not to become too complex.
Where a manufacturer had two or more departments requiring traffic of different types to be moved, examination could be made to see whether, overall, a basic company delivery unit could not be agreed upon, with the addition or subtraction of an agreed percentage according to the loadability and any other peculiarities of the varying traffic.
Finally, in addition to providing a yardstick as to internal transport efficiency the availability of adequate costing of one's own transport department will provide an invaluable guide as to the validity of quotations by outside transport agencies to perform similar services. Additionally, if there is considered to be some special reason for continuing to effect deliveries on one's own vehicles, despite the economics of the case, then the true cost of that decision will also be known.