FOR WORKSHOP AND GARAGE.
Page 63
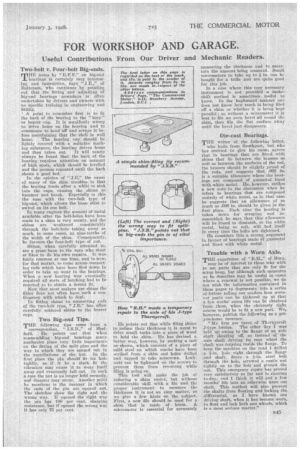
If you've noticed an error in this article please click here to report it so we can fix it.
Useful Contributions From Our Driver and Mechanic Readers.
Two-bolt v. Four-bolt Big-ends.
THE notes by "E.F.F." on big-end bearings ii certainly very interesting and instructive, Says "J.E.," of Battersea, who continues by pointing out that the fitting and adjusting of big-end bearings nowadays is often undertaken by drivers and owners with no specific traieing in engineering and fitting.
" A point to remember first is to fit the back of the bearing to the "keep" or bearer cap. It is manifestly wrong to 'drive home on the bearing and to commence to level off and scrape it before ascertaining that the shell is well home. The bearing cap should be lightly covered with a suitable marking substance, the bearing driven home
and then taken out. It will nearly always be found that the back of the bearing requires attention on account of high spots, which should be levelled and the process repeated nntil the back shows a good bed.
In the opinion of "I.E." the cause of many of the shim troubles is that the bearing tends after a while to sink into the caps, causing the shims to hammer and break. Especially is this the case with the two-bolt type of big-end, which allows the loose shim to swivel on its one bolt.
In many engines the amount of metal available after the bolt-boles have been made in a shim is very scanty, and the shims are weakened considerably through the bolt-hole taking away as much, in some cases, as nine-tenths of the width of the shim. Consequently, he favours the four-bolt type of rod.
Shims, when carefully attended to, are a great boon to the man who Must or likes to do his own repairs, it was fairly common at one time, and is now, for that matter, to come across connecting rods which have been filed down in order to take up wear in the bearings. When a new bearing was eventually required all sorts of botching had to be resorted to to obtain a decent fit.
Now that most makers use shims the fitter does not often have such a contingency with which to deal.
In fitting shims to connecting rods of the two-bolt type, " I.E." has often carefully soldered shims to the bearer caps.
Two Big-end Tips.
THE following tips come from a
correspondent. " of Sheffield. He points out that when reassembling big-end bearings many mechanics place very little importance on the fitting of the split pins and the way in which they are opened out in the castellafions of the nut. In the first place the pin shoubf fit its hole tightly, as if .it be a slack fit the vibration may cause it to wear itself away and eventually fall out. In such a case the nut is no longer held securely, and disaster may occur. Another point he mentions is the manner in which the ends *of the pin are opened out. The sketches show the right and the wrong way. If opened the right way the pin has 100 per cent, shearing resistance, bnt if opened the wrong way it has only 75 per cent.
He points out that while filing shims to reduce their thickness it is usual to drive small tacks into a piece of wood to hold the shim. He has devised a better way, however, by making a tool as shown, which consists of a piece of mild steel on which marks have been scribed from a shim and holes drilled and tapped to take setscrews. Locknuts can he tightened on the screws to prevent them from revolving while filing is going on.
This tool will make the job of reducing a shim easier, but without considerable skill with a file and the proper instrument to measure the thickness it is not an easy matter, so we give a few hints on the subject. First, a new file should be used for a shim that is made of brass. A micrometer is essential for accurately measuring the thickness and to ascertain the amount being removed. Small micrometers to take up to / in. can be bought for a trifle and are quite good for this job.
In a case where this very necessary instrument is not provided a makeshift method is sometimes useful to know. In the haphazard manner ona does not know how much is being filed off a shim or whether it is being kept parallel; so without a micrometer it is best to file an even bevel all round the shim, then file the flat .surface away until the bevel just disappears.
Die-cast Bearings.
THE writer of the following letter,
who hails from Southport, but who has omitted to give his name, agrees that in bearings that are fitted with shims that lie between the brasses as well as between the surfaces of the rod, the brasses should be slightly proud of the rods, and suggests that .002 in. is a suitable allowance where the bearings are composed of gunmetal lined with white metal. He, however, strikes a new note in the discussion when he refers to bearings that are composed entirely of white metal, as in that ease he suggests that an allowance of as much as .006 in. should be given in the first place. Each time the bearing is taken down for scraping and reassembled, he says that this allowance will be found to diminish, as the white metal, being so soft, will bed itself in every time the bolts are tightened.
He considers this a strong argument in favour of bearings made of gunmetal and lined with white metal.
Trouble with a Worn Axle.
THE experience of " R.H.," of Bury, may be of interest to those who wish to use parts that are only fit for the scrap heap, but although such measures as he describes may be useful in cases where a renewal is not possible, we do not wish the information contained in these pages to degenerate into a series of letters telling our readers how wornout parts can be tinkered up so that a few weeks' extra life can be obtained from. them, when the obviously right course would be to fit a new part. We, however, publish the following as a getyou-home measure.
"My firm are risers of Thornycroft I-type lorries. The other day I was• held up owing to the flange of an axle shaft shearing off, so instead of the axle shaft driving its rear wheel the shaft was rotating inside the flange. To keep the machine on the road I drilled a I-in. hole right through the flange and shaft, drove a .1.-in, steel bolt through the hole, screwed a castle nut tightly on to the bolt and pinned the nut. This emergency repair has proved very satisfactory so far and is running to-day, and I think it will put a few months' life into an otherwise worn out shaft. This method will also prevent the shafts from floating and locking the differential, as I have known one driving shaft, when it has become worn, to float and lock both sun wheels, which is a most serious matter."