Tipping vehicle inadequacies
Page 78
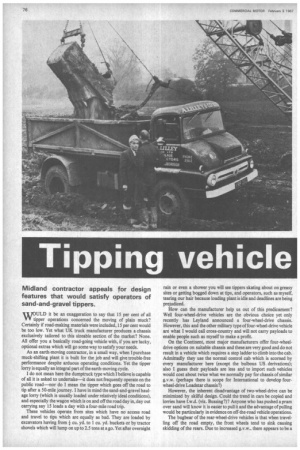
Page 79
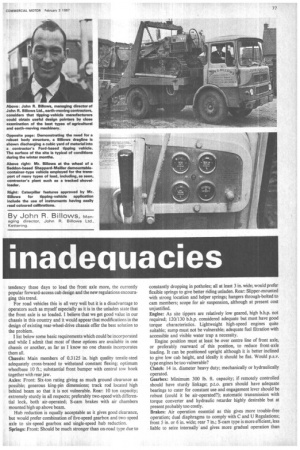
Page 80
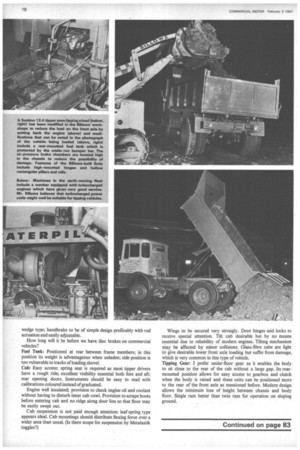
Page 85
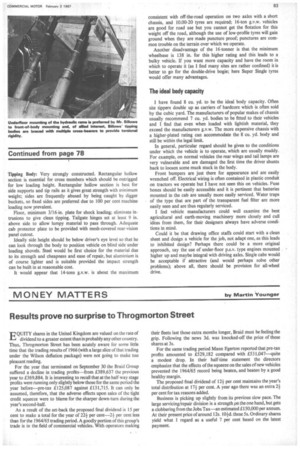
If you've noticed an error in this article please click here to report it so we can fix it.
NV7ULD it be an exaggeration to say that 15 per cent of all ipper operations concerned the moving of plain muck? Certainly if road-making materials were included, 15 per cent would be too low. Yet what UK truck manufacturer produces a chassis exclusively tailored to this sizeable section of the market? None. All offer you a basically road-going vehicle with, if you are lucky, optional extras which will go some way to satisfy your needs.
As an earth-moving contractor, in a small way, when I purchase muck-shifting plant it is built for the job and will give trouble-free performance despite arduous operating conditions. Yet the tipper lorry is equally an integral part of the earth-moving cycle.
I do not mean here the dumptruck type which! believe is capable of all it is asked to undertake—it does not frequently operate on the public road—nor do I mean the tipper which goes off the road to tip after a 50-mile journey. I have in mind the sand-and-gravel haulage lorry (which is usually loaded under relatively ideal conditions), and especially the wagon which is on and off the road day in, day out carrying say 15 loads a day with a four-mile road trip.
These vehicles operate from sites which have no access road and travel to tips which are equally as bad. They are loaded by excavators having from + cu. yd. to 1 cu. yd. buckets or by tractor shovels which will lump on up to 2.5 tons at a go. Yet after overnight rain or even a shower you will see tippers skating about on greasy sites or getting bogged down at tips, and operators, such as myself, tearing our hair because loading plant is idle and deadlines are being prejudiced.
How can the manufacturer help us out of this predicament? Well four-wheel-drive vehicles are the obvious choice yet only recently has Leyland announced a four-wheel-drive chassis. However, this and the other military type of four-wheel-drive vehicle are what I would call cross-country and will not carry payloads to enable people such as myself to make a profit.
On the Continent, most major manufacturers offer four-wheeldrive options on suitable chassis and these are very good and do not result in a vehicle which requires a step ladder to climb into the cab. Admittedly they use the normal control cab which is scorned by every manufacturer here (except the bulbous US derivations); also I guess their payloads are less and to import such vehicles would cost about twice what we normally pay for chassis of similar g.v.w. (perhaps there is scope for International to develop fourwheel-drive Loadstar chassis?) However, the inherent disadvantage of two-wheel-drive can be minimized by skilful design. Could the trend in cars be copied and lorries have f.w.d. (viz. Bussing?)? Anyone who has pushed a pram over sand will know it is easier to pull it and the advantage of pulling would be particularly in evidence on off-the-road vehicle operations.
The bugbear of the rear-wheel-drive vehicles is that when travelling off the road empty, the front wheels tend to sink causing skidding of the rears. Due to increased g.v.w., there appears to be a tendency these days to load the front axle more, the currently popular forward-access cab design and the new regulations encouraging this trend.
For road vehicles this is all very well but it is a disadvantage to operators such as myself especially as it is in the unladen state that the front axle is so loaded. I believe that we get good value in our chassis in this country and it would appear that modifications in the design of existing rear-wheel-drive chassis offer the best solution to the problem.
I list below some basic requirements which could be incorporated and while I admit that most of these options are available in one chassis or another, as far as I know no one chassis incorporates them all.
Chassis: Main members of 0.3125 in. high quality tensile-steel adequately cross-braced to withstand constant flexing; optimum wheelbase 10 ft.; substantial front bumper with central tow hook together with rear jaw.
Axles: Front: Six-ton rating giving as much ground clearance as possible; generous king-pin dimensions; track rod located high behind beam so that it is not vulnerable. Rear: 10 ton capacity; extremely sturdy in all respects; preferably two-speed with differential lock, both air-operated; S-cam brakes with air chambers mounted high up above beam.
Hub reduction is equally acceptable as it gives good clearance, but would prefer combination of five-speed gearbox and two-speed axle to six-speed gearbox and single-speed hub reduction. Springs: Front: Should be much stronger than on-road type due to constantly dropping in potholes; all at least 3 in. wide; would prefer flexible springs to give better riding unladen. Rear: Slipper-mounted with strong location and helper springs; hangers through-bolted to cam members; scope for air suspension, although at present cost unjustified.
Engine: As site tippers are relatively low geared, high b.h.p. not required; 120/130 b.h.p. considered adequate but must have good torque characteristics. Lightweight high-speed engines quite suitable; sump must not be vulnerable; adequate fuel filtration with accessible and visible water trap a necessity.
Engine position must at least be over centre line of front axle, or preferably rearward of this position, to reduce front-axle loading. It can be positioned upright although it is better inclined to give low cab height, and ideally it should be flat. Would p.s.v. type engines be too vulnerable?
Clutch: 14 in. diameter heavy duty; mechanically or hydraulically operated. Gearbox: Minimum 300 lb. ft. capacity; if remotely controlled should have sturdy linkage; p.t.o. gears should have adequate bearings to cater for constant use and engagement lever should be robust (could it be air-operated?); automatic transmission with torque converter and hydraulic retarder highly desirable but at present probably too costly.
Brakes: Air operation essential as this gives more trouble-free operation; dual diaphragms to comply with C and U Regulations; front 5 in. or 6 in. wide; rear 7 in.; S-cam type is more efficient, less liable to seize internally and gives more gradual operation than wedge type; handbrake to be of simple design preferably with rod actuation and easily adjustable.
How long will it be before we have disc brakes on commercial vehicles?
Fuel Tank: Positioned at rear between frame members; in this position its weight is advantageous when unladen; side position is too vulnerable to tracks of loading shovel.
Cab: Easy access; spring seat is required as most tipper drivers have a rough ride; excellent visibility essential both fore and aft; rear opening doors. Instruments should be easy to read with calibrations coloured instead of graduated.
Engine well insulated; provision to check engine oil and coolant without having to disturb inner cab cowl. Provision to scrape boots before entering cab and no ridge along door line so that floor may be easily swept out.
Cab suspension is not paid enough attention: leaf-spring type appears ideal. Cab mountings should distribute flexing force over a wider area than usual. (Is there scope for suspension by Metalastik toggles?) Wings to be secured very strongly. Door hinges and locks to receive special attention. Tilt cab desirable but by no means essential due to reliability of modern engines. Tilting mechanism may be affected by minor collisions. Glass-fibre cabs are light to give desirable lower front axle loading but suffer from damage, which is very common in this type of vehicle.
Tipping Gear: I prefer under-floor gear as it enables the body to sit close to the rear of the cab without a large gap. Its rearmounted position allows for easy access to gearbox and clutch when the body is raised and these units can be positioned more to the rear of the front axle as mentioned before. Modern design allows the minimum loss of height between chassis and body floor. Single ram better than twin ram for operation on sloping ground.
Tipping Body: Very strongly constructed. Rectangular hollow section is essential for cross members which should he outrigged for low loading height. Rectangular hollow section is best for side supports and tip rails as it gives great strength with minimum weight; sides are frequently abused by being caught by digger buckets, so fixed sides are preferred due to 100 per cent machine loading now prevalent.
Floor, minimum 3/16-in, plate for shock loading; eliminate intrusions to give clean tipping. Tailgate hinges set at least 9 in. above side to allow lumpy material to pass through. Adequate cab protector plate to be provided with mesh-covered rear-vision panel cutout.
Ideally side height should be below driver's eye level so that he can look through the body to position vehicle on blind side under loading shovels. Steel would be first choice for the material due to its strength and cheapness and ease of repair, but aluminium is of course lighter and is suitable provided the impact strength can be built in at reasonable cost.
It would appear that 14-tons g.v.w. is about the maximum consistent with off-the-road operation on two axles with a short chassis, and 10.00-20 tyres are required; 16-ton g.v.w. vehicles are good for road use but you cannot get the flotation for this weight off the road, although the use of low-profile tyres will gain ground when they are made puncture proof; punctures are common trouble on the terrain over which we operate.
Another disadvantage of the 16-tonner is that the minimum wheelbase is 138 in. for this higher rating and this leads to a bulky vehicle. If you want more capacity and have the room in which to operate it (as I find many sites are rather confined) it is better to go for the double-drive bogie; here Super Single tyres would offer many advantages.
The ideal body capacity
I have found 8 cu. yd. to be the ideal body capacity. Often site tippers double up as carriers of hardcore which is often sold by the cubic yard. The manufacturers of popular makes of chassis usually recommend 7 cu. yd. bodies to be fitted to their vehicles and I find that even when loaded with lightish material, they exceed the manufacturers g.v.w. The more expensive chassis with a higher-plated rating can accommodate the 8 cu. yd. body and still be within the legal limit.
In general, particular regard should be given to the conditions under which the vehicle is to operate, which are usually muddy. For example, on normal vehicles the rear wings and tail lamps are very vulnerable and are damaged the first time the driver shunts back to loosen some muck stuck in the body.
Front bumpers are just there for appearance and are easily wrenched off. Electrical wiring is often contained in plastic conduit on tractors we operate but I have not seen this on vehicles. Fuse boxes should be easily accessible and it is pertinent that batteries mounted in the cab are usually more easily serviced. Water traps of the type that are part of the transparent fuel filter are more easily seen and are thus regularly serviced.
I feel vehicle manufacturers could well examine the best agricultural and earth-moving machinery more closely and cull ideas from them, for their designers always have adverse conditions in mind.
Could it be that drawing office staffs could start with a clean sheet and design a vehicle for the job, not adapt one, as this leads to inhibited design? Perhaps there could be a more original approach, say the use of under-floor p.s.v. type engines mounted higher up and maybe integral with driving axles. Single cabs would be acceptable if attractive (and would perhaps solve other problems); above all, there should be provision for all-wheel drive.