A USEFUL MISCELLANY.
Page 29
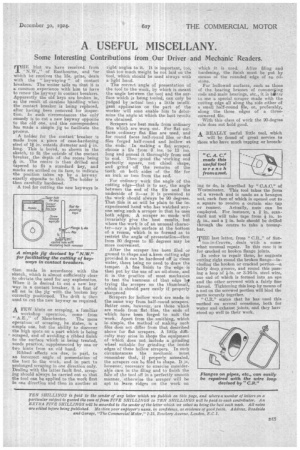
If you've noticed an error in this article please click here to report it so we can fix it.
Some Interesting Contributions from Our Driver and Mechanic Readers.
MHE hint we have received from
'
NW.," of Eastbourne, and or which he receives the 15s. prize, deals with the " keywaying " of contact breakers. The writer tells us that it is a common .experience with him to have to renew the keyway in contact breakers. Apparently the old keys are broken in, C s the result of careless handling when the contact breaker is being replaced, after haying been removed for inspection. In such circumstances the only remedy is to cut El new keyway opposite to the old one, and this correspondent has made a simple jig to facilitate the process.
A holder for the contact breaker ;s made from a piece of case-hardening steel of 1 in. outside diameter and I. in. longThis is bored, as ehown in the sketch, to fit the outside of the contact breaker, the depth of the recess being * in. The centre is then drilled and tapered to fit a standard key, and marks are scribed on its face, to indicate the position taken up by a keyway exactly opposite to this. The holder is then carefully hardened.
A tool for cutting the new keyways is then made in accordance with the sketch, which is almost sufficiently clear to obviate the need for any explanation. When it is desired to cut a new key way in a contact breaker, it is first of all set in the jig with. the broken key correctly positioned. The drift is then used to cut the new keyway as required.
A FEW hints on scraping, a familiar workshop operation, come• from
" A.E.," of Manchester. The mere operation of scraping, he states, is a simple one, but the ability to discover the high spots on a part which is being scraped, and of avoiding a ribbed finish to the surface which is being treated, needs practice, supplemented by one or two hints from an old hand.
Ribbed effects are due, in part, to an incorrect angle of presentation of the tool to the work, and in part to prolonged scraping in one direction only. Dealing with the latter fault first, scraping should always be carried out so that the tool can be applied to the work first in one direction and then in another at
right angles to it. It is important, too, that too much weight be not laid no the tool, which should be used always with
a light hand. • The correct angle of presentation of the tool to the work, by which is meant the angle between the tool and the surface which is being tooled, can only be judged by _actual test; a little intelligent application on the part of. the worker will soon enable him to determine the angle at which the best results are obtained.
Scrapers are best made from ordinary files which are worn out. For flat surfaces ordinary flat files are used, and for round faces half-round files or fiat files forged half-round and hollow at the ends. In making a flat_ scraper, choose a file from 8 ins. to 12 ins. long and anneal it thoroughly from end to end. Thee grind the working end perfectly square, not chisel shape, and grind off the remains of tho teeth on both sides of the file • for an inch or two from the end.
For ordinary work the angle of the cutting edge—that is to say, the angle between the end of the file and the underside of it—as it is presented to the work should always be 90 degrees. That this is so will be plain to the inexperienced hand who, has watched anyone using such a scraper in that he uses both edges. A scraper so made will invariably give the best results, hut where the work is of an unusual character—say a plain surface at the bottom of a recess, which is so formed as to restrict the angle of presentation—then from 80 degrees to 85 degrees may be more convenient.
After the scraper has been filed or ground to shape and a. keen cutting edge provided it can be hardened off in clean -water, there being no need to draw the temper. A fine finish to the edge is then put by the use of an oil-stone, and it is the practice of most mechanics to test the keenness of that edge bye trying the scraper on the thumbnail, which it should pare easily if properly sharpened. Scrapers for hollow work are made in the same way Irons half-round scrapers. Better ones, however, • are those which are made from flat files, the ends of which have been forged to suit .the work. Apart from the smithing, which issimple, the method of making such files does not differ from that described above for flat scrapers. A little difficulty may arise in shops the equipment of -which does not include a grinding -wheel suitable for grinding the inside edges of these hollow scrapers. In such circumstances the mechanic must remember that, if properly annealed, the scrapers can be filed to shape. It is, however, necessary to exercise considerable care in the filing and to finish the faZe of the tool off in a perfectly smooth manner, otherwise the scraper will he apt to leave ridges on the work on
which it is used. After filing end hardening, the finish must be put by means of the rounded edge of an oilstone.
For hollowed surfaces, such as those of the bearing brasses of comine4ing rods and main bearings, etc., it is bitter to use a special scraper made with the cutting edge all along the side either of a small half-round file, or, preferably, along the three cages of a threecornered file.
With this class of work the 90-degree rule does not hold good.
A REALLY useful little tool, which will be found of great service to those who have much tapping or broach ina to do, is described by " C.A.C," of 'Westminster. This tool takes the form of a wrench and is made as a hexagon. nut, each face of which is opened out to a square to receive a certain size tap or reamer. Actually, nuts can be employed. For instance, a * in. standard nut will take taps from * in. to * in., and a * in. hole should be drilled through the centre to take a tommy: bar.
THE last letter, from " C.R.," of Sutton-in-Craven, deals with a somewhat unusual repair. Li this case it is for cracked or broken flange joints.
In order to repair these, he suggests cutting right round the broken flange—including the broken or cracked portion—a fairly deep groove, and round this passing a loop of Fin. or 3-16-in. steel wire, one end of which is formed into an eye and the other screwed with a fairly fine thread. Tightening this loop by means of a nut on the screwed portion will bind the parts securely together. • "Cit." states that he has used this method on several occasions, both for water and exhaust joints, and they have stood up well to their work.