• There is little disagreement among operators of petroleum spirit
Page 65
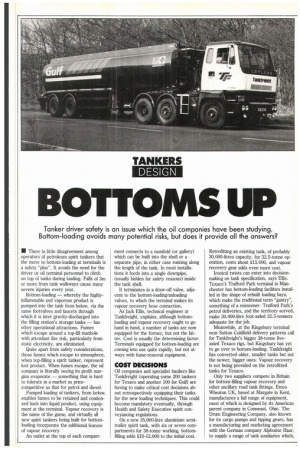
Page 66
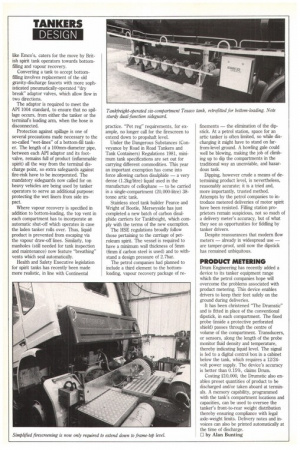
If you've noticed an error in this article please click here to report it so we can fix it.
tankers that the move to bottom-loading at terminals is a safety "plus". It avoids the need for the driver or oil terminal personnel to climb on top of tanks during loading. Falls of 3m or more from tank walkways cause many severe injuries every year.
Bottom-loading — whereby the highlyinflammable and vaporous product is pumped into the tank from below, via the same footvalves and faucets through which it is later gravity-discharged into the filling station's storage tanks — has other operational attractions. Fumes which escape around a top-fill manhole with attendant fire risk, particularly from static electricity, are eliminated.
Quite apart from safety considerations, those fumes which escape to atmosphere, when top-filling a spirit tanker, represent lost product. When fumes escape, the oil company is literally seeing its profit margins evaporate — something that is hard to tolerate in a market as pricecompetitive as that for petrol and diesel.
Pumped loading of tankers, from below, enables fumes to be retained and condensed back into liquid product, using equipment at the terminal. Vapour recovery is the name of the game, and virtually all new spirit tankers being built for bottomloading incorporate the additional feature of vapour recovery.
An outlet at the top of each compart ment connects to a manifold (or gallery) which can be built into the shell or a separate pipe, in either case running along the length of the tank. In most installations it feeds into a single downpipe, (usually hidden for safety reasons) inside the tank shell.
It terminates in a draw-off valve, adjacent to the bottom-loading/unloading valves, to which the terminal makes its vapour recovery hose connection.
As Jack Ellis, technical engineer at Tankfreight, explains, although bottomloading and vapour recovery ought to go hand in hand, a number of tanks are now equipped for the former, but not the latter. Cost is usually the determining factor.
• Terminals equipped for bottom-loading are coming into use quite rapidly, but not always with fume-removal equipment.
COST DECISIONS
Oil companies and specialist hauliers like Tankfreight (operating some 200 tankers for Texaco and another 100 for Gulf) are having to make critical cost decisions about retrospectively equipping their tanks for the new loading techniques. This could become mandatory eventually, through Health and Safety Executive spirit conveyancing regulations.
On a new 35,000-litre aluminium semitrailer spirit tank, with six or seven compartments for 38-tonne working, bottomfilling adds 210-12,000 to the initial cost. Retrofitting an existing tank, of probably 30,000-litres capacity, for 32.5-tonne operation, costs about £15,000, and vapour recovery gear adds even more cost.
Ironical twists can enter into decisionmaking on tank specification, says Ellis. Texaco's Trafford Park terminal in Manchester has bottom-loading facilities installed in the shape of rebuilt loading bays, which make the traditional term "gantry", something of a misnomer. Trafford Park's petrol deliveries, and the territory served, make 30,000-litre four-axled 32.5-tonners adequate for the job.
Meanwhile, at the Kingsbury terminal near Sutton Coldfield delivery patterns call for Tankfreight's bigger 38-tonne fiveaxled Texaco rigs, but Kingsbury has yet to go over to bottom-loading. Tankfreight has converted older, smaller tanks but not the newer, bigger ones. Vapour recovery is not being provided on the retrofitted tanks for Texaco.
Only two suppliers compete in Britain for bottom-filling vapour recovery and other ancillary road tank fittings. Emco Wheaton UK, based at Margate in Kent, manufactures a full range of equipment, most of which is designed by its American parent company in Conneaut, Ohio. The Drum Engineering Company, also known for its cargo pumps and tipping gears, has a manufacturing and marketing agreement with the German company Alphonse Haar, to supply a range of tank auxiliaries which, like Emco's, caters for the move by British spirit tank operators towards bottomfilling and vapour recovery.
Converting a tank to accept bottomfilling involves replacement of the old gravity-discharge faucets with more sophisticated pneumatically-operated "dry break" adaptor valves, which allow flow in two directions.
The adaptor is required to meet the API 1004 standard, to ensure that no spillage occurs, from either the tanker or the terminal's loading arm, when the hose is disconnected.
Protection against spillage is one of several precautions made necessary to the so-called "wet-lines" of a bottom-fill tanker. The length of a 100mm-diameter pipe, between each API adaptor and its footvalve, remains full of product (inflammable spirit) all the way from the terminal discharge point, so extra safeguards against fire-risk have to be incorporated. The mandatory sideguards now called for on heavy vehicles are being used by tanker operators to serve an additional purpose: protecting the wet liners from side impact.
Where vapour recovery is specified in addition to bottom-loading, the top vent in each compartment has to incorporate an automatic shut-off which operates in case the laden tanker rolls over. Thus, liquid product is prevented from escaping via the vapour draw-off lines. Similarly, top manholes (still needed for tank inspection and maintenance) now feature "breathing" vents which seal automatically.
Health and Safety Executive legislation for spirit tanks has recently been made more realistic, in line with Continental practice. "Pet reg" requirements, for example, no longer call for the firescreen to extend down to propshaft level.
Under the Dangerous Substances (Conveyance by Road in Road Tankers and Tank Containers) Regulations 1981, minimum tank specifications are set out for carrying different commodities. This year an important exemption has come into force allowing carbon disulphide — a very dense (1.2kg/litre) liquid used in the manufacture of cellophane — to be carried in a single-compartment (20,000-litre) 38tonne artic tank.
Stainless steel tank builder Pearce and Wright of Bootie. Merseyside has just completed a new batch of carbon disulphide carriers for Tankfreight, which comply with the terms of the new exemption.
The HSE regulations broadly follow those pertaining to the carriage of petroleum spirit. The vessel is required to have a minimum wall thickness of 5mm (6rnm if carbon steel is used) and to withstand a design pressure of 2. Thar.
The petrol companies had planned to include a third element to the bottomloading, vapour recovery package of re finements — the elimination of the dipstick. At a petrol station, space for an artic tanker is often limited, so while discharging it might have to stand on farfrom-level ground. A howling gale could well be blowing, making the job of climbing up to dip the compartments in the traditional way an unenviable, and hazardous task.
Dipping, however crude a means of determining product level, is nevertheless, reasonably accurate; it is a tried and, more importantly, trusted method. Attempts by the petrol companies to introduce metered deliveries of motor spirit have been resisted. Filling station proprietors remain suspicious, not so much of a delivery meter's accuracy, but of what they see as opportunities for fiddling by tanker drivers.
Despite reassurances that modern flow meters — already in widespread use — are tamper-proof, until now the dipstick has remained unbiquitous.
PRODUCT METERING
Drum Engineering has recently added a device to its tanker equipment range which the petrol companies hope will overcome the problems associated with product metering. This device enables drivers to keep their feet safely on the ground during deliveries.
It has been christened "The Drumstic" and is fitted in place of the conventional dipstick, in each compartment. The fixed probe (inside a protective perforated shield) passes through the centre of volume of the compartment. Transducers, or sensors, along the length of the probe monitor fluid density and temperature, thereby indicating liquid level. The signal is fed to a digital control box in a cabinet below the tank, which requires a 12/24volt power supply. The device's accuracy is better than 0.15%, claims Drum.
Costing 210,000, the Drumstic also enables preset quantities of product to be discharged and/or taken aboard at terminals. A memory capability, programmed with the tank's compartment locations and capacities, can be used to oversee the tanker's front-to-rear weight distribution thereby ensuring compliance with legal axle-weight limits. Delivery notes and invoices can also be printed automatically at the time of discharge.
El by Alan Bunting