Make Do and Mend in Metals
Page 34
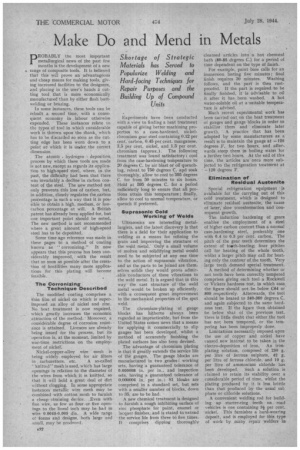
Page 35
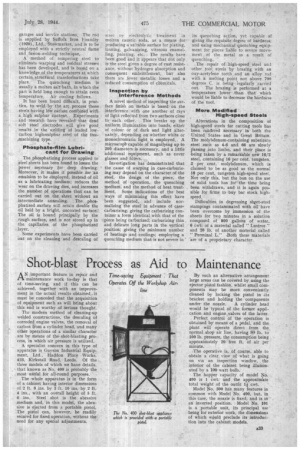
If you've noticed an error in this article please click here to report it so we can fix it.
Shortage of Strategic Materials has Served to Popularize Welding and Hard-facing Techniques for Repair Purposes and the Building Up of Compound Units
PROBABLY the most important metallurgical news of the past few months is the development of a new • range of composite tools. It is believed that this will prove an advantageous and cheap means for making tools, giving increased facilities to the designers, and placing in the user's hands a cutting tool that is more economically manufactured than by either flash buttwelding or brazing.
In some instances, these tools can be rebuilt a second time, with a consequent economy in labour otherwise expended. These instances relate to the types of tool in which considera,ble work is thrown upon the shank, which has to be discarded so soon as the cutting edge has been worn down to a point at which it is under the correct dimension.
The atomic hydrogen deposition, process by which these tools are made is not new, except as regards its application to high-speed steel, where, in the past, the difficulty had been that there was invariably a decline in carbon content of the steel. The new method not only prevents this loss of carbon, but, in addition, closely regulates the carbon percentage in such a way that it is possible to obtain a high, medium, or carbon percentagepercentage at will. A British patent has already been applied for, but one important point should be noted. The new method is not recommended where a great amount of high-speed steel has to be depoSited.
Some time ago reference was made in these pages to a Method of coating known as " corronizing." It now appears that this process has been considerably improved, with the result that so soon as possible after the cessation of hostilities many more applications for this plating will become feasible.
The Dorronizing Technique Described The modified coating comprises a thin film of nickel on which is superimposed an alloy of nickel and zinc. No heat treatment is now required. which greatly increases the economic attraction of the method. Moreover, a considerable degree of corrosion resistance is attained. Licences are already being issued for the process, but its operation is, at the moment, limited by war-time restrictions on the employment of nickel: Nickel-copper-alloy wire mesh is being widely employed for air filters in carburetters, etc. A so-called "
knitted" mesh is used, which has large openings in relation to the diameter of the wires from which it is knitted, so that it will hold a great deal of dirt e.ithout clogging. In some appropriate instances metallic wire mesh may be combined with cotton mesh to furnish a cheap. straining device. ,Even with fine wire, as few as four.or five open, ings to the lineal inch may be had in wire 0.0045-0.005 dia. A wide range ol•forms and designs, both large and
small, may be produced.
Experiments have been conducted with a view to finding a heat treatment capable of giving better machining properties to a case-hardened, nickelchromium gear steel containing 0.12 per cent. carbon, 0.45 per cent. manganese, 3.5 per cent, nickel, and 1.5 per cent. chromium (approx.). The following treatment was found satisfactory :cçol from the case-hardening temperature to 20 degrees C. by air blast or oil quenching, reheat to 750 degrees C. ad soak thoroughly, allow to cool to 595 degrees C. for from rk minutes to six hours. Hold at 505 degrees C. for a period sufficiently long to ensure that all portions attain this temperature; finally, allow to cool to normal temperature, or quench if preferred.
Suprasonlc Cold Working of Welds Ultrasonics are interesting metallurgists, and the latest discovery is that there is a field for their application to welding as a means for refining the grain and improving the structure of the weld Metal. Only a small volume of molten and solidifying metal would need to be subjected at any one time to the action of suprasonic vibration, and as the parts to be joined are themselves solids they would prove admirable conductors of these vibrations to the weld metal. It is argued that in this way the cast structure of the weld metal would be broken up efficiently, with a consequent great improvement in the mechanical properties of the spot weld.
The chromium-plating of gauge blocke has hitherto always been regarded as impracticable, but from the United States comes news that a means for applying it commercially to slip gauges has been developed, whilst a method of accurately finishing the plated surfaces has also been devised.
The advantage of chromium plating is that it greatly extends the service life of the gauges. The gauge blocks are manufactured in two grades: working sets, having a guaranteed tolerance of 0.000008 in. per in., and inspection sets, having a guaranteed tolerance of 0.000004 in, per in.; 81 bloaks are comprised in a standard set, but sets with a smaller number of blocks, down to 35, are to be had.
A new chemical treatment is designed to furnish a rough inhibiting surface of 7inc phosphate for paint, enamel or lacquer finishes, and is stated to-extend the service life from three to five times. It comprises dipping thoroughly
cleansed articles into a hot chemical bath (80-85 degrees C.) for a period of time dependent on the type of finish.
For example, paint base calls for an immersion lasting five minutes; final finish requires 30 minutes. Washing follows, and the part is then rustproofed. If the part is required to be finally finished, it is advisable to oil it after it has been washed. A hot water-soluble oil at a suitable temperature is advised.
Much recent experimental work has been carried out on the heat treatment of gauges and gauge blocks in order to stabilize them and eliminate later growth. A practice that has been adopted by some manufacturers as a result is to maintain the gauge at —120 degrees F. for two hours, and after-, wards steep them in boiling water for a further two hours. At the end of this time, the articles are once more subjected to the refrigeration treatment at —120 degrees F.
Elimination of Residual Austenite Special refrigeration equipment is available for the carrying out of this cold treatment, which is designed to eliminate residual austenite, the cause of later, slow transformation and consequent growth.
The induction hardening of gears enables the employment of a steel of higher carbon content than a normal case-hardening steel, preferably one with 0.4 to 0.5 per cent. carbon. 'The pitch of the gear teeth determines the extent of tooth-heating; finer pitches call for heating of the whole tooth. whilst a larger pitch may call for heating only the contour of the tooth. Very large teeth demand special treatment.
• A method of determining whether or not tools have been correctly tempered comprises giving each tool a Rockwell or Vickers hardness test, in which case. the figure should not be. below C64 or 800 respectively. Afterwards, the tool should be heated to 340-360 degrees C. and again subjected to the same hardness test. If the figure then Obtained be below that of the previous test, there is little doubt that either the tool has not been tempered, or the tempering has been improperly done.
Limitations necessarily imposed upor the use of copper and nickel have caused new ixtt6rest to be taken in the
electro-deposition of iron. An ironplating solution, composed of 250 g. per litre of ferrous sulphate, 42 g. per litre of ferrous chloride, and 10 g. per litre of ammonium chloride has been developed. Such a solution is claimed to retain its stability over a considerable period of time, whilst the plating produced by it is less brittle than that produced by the usual sulphate or chloride solutions.
A convenient welding rod for building up starter-ring teeth on road vehicles is one containing 3* per cent. nickel. This furnishes a hard-wearing deposit, and is employed for this type of work by many repair welders in garages and service stations. The rod is supplied by Suffolk Iron Foundry (1920), Ltd., Stowmarket, and is to be employed with a strictly neutral flame and fusion-welding technique.
A method of tempering steel to eliminate warping and residual stresses has been developed, and is based on a knowledge of the temperatures at which certain, structural transforinations take place. The quenching medium is usually a molten salt bath, in which the part is held long enough to attain even temperature. Air cooling follows.
It has been found difficult, in practice, to weld by • the arc, process those steels having ldw carbon combined with a high sulphur content. Experiments and research have revealed. that dead soft steel electrodes will give good, resulti in the welding of leaded lowcarbon high-sulphur steel of the free-machining type.
Phosphate-film Lubricant for Drawing The phosphatizing process applied to steel sheets has been found to lessen the power necessary for deep drawing. Moreover, it makes it possible for an emulsion to be employed, instead of oil as a lubricating medium; reduces the wear on the drawing dies, and increases the number of operations that can be carried out on the sheet without an intermediate annealing. The phosphatized surface will retain double the oil held by a bright, uncoated surface. The oil is bound principally by the rough surface, and is not stored up in the capillaries of the phosphatized layer.
Some experiments have been carried Out on the cleaning and descaling of
steel Dy electrolytic treatment in molten caustic soda, as a means for producing a suitable surface for plating, tinning, galvanizing, vitreous enamelling, painting, etc. The results have been good and it appears that not only is the steel given a degree of rust resistance, without -hydrogen absorption and consequent embrittlement, but also there are fewer metallic losses and a reduced consumption of chemicals.
Inspection by Interference Methods A novel method of inspecting the surface finish on metals is based on the interference with one another of rays of light reflected from two surfaces close to each other. This breaks up the uniform illumination into bands, either of colour or of dark and light alternately, depending on whether white or monochromatic light is employed.. A microscoph capable of magnifying up to 200 diameters is necessary, and a little additional equipment, such as cover glasses and filters.
Investigation has demonstrated that the cause of warping in case-carburizing may depend on the character a the steel, the design of the piece, the method of operation, the quenching medium, and the method of heat treatment. Some indications of the best ways of minimizing this effect have been suggested, and include normalizing the steel in advance of casecarburizing; giving the carburizing container a farm identical with that of the piece being carburized; carburizing thin and delicate long parts in the vertical position; giving the minimum number of heatings and coolings; employing a quenching medium that is not severe in'
its quenching action, yet capable of giving the requisite degree of hardness; and using mechanical quenching equipment for pieces liable to severe movement of the metal as a result of quenching.
The repair of high-speed steel and other tab!, steels by brazing with an oxy-acetylene torch and an alloy rod with a melting point not above 700 degrees C. is being l'egularIY carried out. The brazing is performed at a temperature lower than that which would be liable to decrease the hardness of the tool.
More Modified High-speed Steels
Alterations in the composition of high-speed steels for cutting tools has been mndered necessary in both the United States and in Great Britain. The molybdenum-containing substithte steel such as 4-6 and 66 are slowly Passing into limbo, and their place is being taken by a remarkable new 16/2 steel, containing 16 per cent. tungsten, 2 per cent, molybdenum, which is claimed to be as good as the normal 18 per cent, tungsten high-speed steel. Not only this, but the ban on the use of solid tools has for the time being been withdrawn, and it is again possible for firms to buy bar stock highspeed.
Difficulties in degreasing sheet-steel stampings contaminated with oil have been overcome by immersion of the sheets for two minutes in a solution composed of 300 gallons of water, 6 Cwt. of a material called " Lustros " and 20 lb. of another material called " Perminal L." -Both these materials are of a proprietary character.