THE ONE TI E FO THAT GOT
Page 36
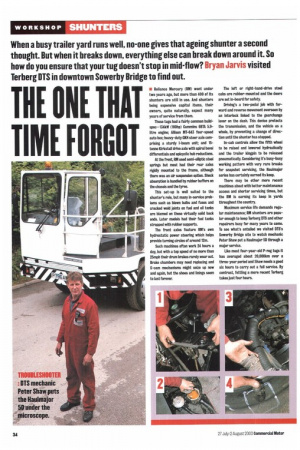
Page 37
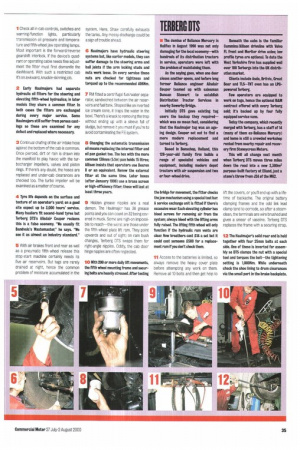
If you've noticed an error in this article please click here to report it so we can fix it.
When a busy trailer yard runs well, no-one gives that ageing shunter a second thought. But when it breaks down, everything else can break down around it. So how do you ensure that your tug doesn't stop in mid-flow? Bryan Jarvis visited Terberg BB in downtown Sowerby Bridge to find out.
Reliance Mercury (AM) went under two years ago, but more than 400 of its shunters are still in use. And shunters being expensive capital items, their owners, quite naturally, expect many years of service from them.
These tugs had a fairly common buildspec-134kW (180hp) Cummins 6BTA 5.9litre engine; Allison MT-64.3 four-speed auto box; heavy-duty CNN steer axle comprising a sturdy I-beam unit; and 15twine Kirkstall drive axle with spiral bevel differentials and epicyclic hub reductions, At the front, AM used semi-elliptic steel springs but most had their rear axles rigidly mounted to the frame, although there was an air suspension option. Shock absorption is handled by rubber buffers on the chassis and the tyres.
This set-up is well suited to the shunter's role, but many in-service problems such as blown bulbs and fuses and cracked weld joints on fuel and oil tanks are blamed on these virtually solid back IL ends. Later models had their fuel tanks
strapped with rubber supports.
The front axles feature AM's own hydrostatic power steering which helps provide turning circles of around 12m.
Such machines often work 24 hours a day, but with a top speed of no more than 25mph their drum brakes rarely wear out. Brake chambers may need replacing and S-cam mechanisms might seize up now and again, but the shoes and linings seem to last forever. The left or right-hand-drive steel cabs are rubber-mounted and the doors are set in-board for safety.
Driving's a two-pedal job with forward and reverse movement overseen by an interlock linked to the gearchange lever on the dash. This device protects the transmission, and the vehicle as a whole, by preventing a change of direction until the shunter has stopped.
In-cab controls allow the frith wheel to be raised and lowered hydraulically and the trailer kingpin to be released pneumatically. Considering it's busy-busy working pattern with very rare breaks for snapshot servicing, the Haulmajor series has certainly earned its keep.
There may be other more recent machines about with better maintenance access and shorter servicing times, but the AM is earning its keep in yards throughout the country.
Maximum service life demands regular maintenance; AM shunters are popular enough to keep Terberg DM and other repairers busy for many years to come. To see what's entailed we visited DTS's Sowerby Bridge site to watch mechanic Peter Shaw put a Haulmajor 50 through a major service.
Like most four-year-old P-reg tugs it has averaged about 20,000km over a three-year period and Shaw needs a good six hours to carry out a full service. By contrast, fettling a more recent Terberg takes just four hours.
I Check all in-cab controls, switches and warning/function lights, particularly transmission oil pressure and temperature and fifth-wheel jaw operating lamps. Most important is the forward/reverse gearshift interlock. If the device's quadrant or operating cable needs fine adjustment the fitter must first dismantle the dashboard. With such a restricted cab it's an awkward, knuckle-skinning job.
2 Early Haulmajors had separate hydraulic oil filters for the steering and elevating fifth-wheel hydraulics; in later models they share a common filter. In both cases the filters are exchanged during every major service. Some Haulmajors still suffer from porous castings so these are examined for any defect and replaced where necessary.
3 Continual chafing of the air intake hose against the bottom of the cab is common. Once pierced, dirt or rain is drawn into the manifold to play havoc with the turbocharger impellers, valves and piston rings. If there's any doubt, the hoses are replaced and under-cab clearances are checked too. The turbo impeller will be examined as a matter of course.
• 6. Tyre life depends on the surface and texture of an operator's yard: on a good site expect up to 3,000 hours' service. Many hauliers fit second-hand tyres but Terberg DTS's Alisdair Curler reckons this is a false economy. "We usually fit Bandvulc's Wastemaster," he says. "We see it as almost an industry standard."
5 With air brakes front and rear as well as a pneumatic fifth wheel release this stop-start machine certainly needs its five air reservoirs. But tugs are rarely drained at night, hence the common problem of moisture accumulated in the
system. Here, Shaw carefully exhausts the tanks. Any messy discharge could be a sign of trouble ahead.
Haulmajors have hydraulic steering systems but, like earlier models, they can suffer damage to the steering arms and ball joints if the arm locking studs and nuts work loose. On every service these nuts are checked for tightness and torqued up to the recommended 406Nm.
7 RM fitted a centrifugal fuel/water separator, sandwiched between the air reservoirs and fuel tank. Shaped like an inverted ice cream cone, it traps the water in the bowl. There's a knack to removing the trap without ending up with a sleeve full of sludge, but remove it you must if you're to avoid contaminating the FIE system.
8 Changing the automatic transmission oil means replacing the internal fitter and oil pan gasket too, The box with the more common 139mm (5.1in) pan holds 15 litres; Allison insists that operators use Dexron II or an equivalent. Renew the external filter at the same time. Later boxes (after January 1996) use a brass screen or high-efficiency filter; these will last at least three years.
9 Hidden grease nipples are a real demon. The Haulmaior has 36 grease points and you can count on 32 being covered in muck. Some are nigh-on impossible to reach—the worst are those under the fifth wheel plate lift ram. They point upwards and out of sight; on ram bush changes, Terberg DTS swaps them for right-angle nipples. Oddly, the cab door hinge nipples are often neglected.
10 With 200 or more daily Itft movements, the fifth wheel mounting frame and securing bolts are heavily stressed. After testing the bridge for movement, the fitter checks the jaw mechanism using a special test bar. A service exchange unit is fitted if there's excessive wear Each elevating cylinder has bleed screws for removing air from the system; always bleed with the lifting arms fully raised. The lifting fifth wheel will only function if the hydraulic ram vents are clear. New breathers cost £14 a set but it could cost someone G500 for a replacement ram if you don't check them.
11 Access to the batteries is limited, so always remove the heavy cover plate before attempting any work on them. Remove all 10 bolts and then get help to lift the covers, or you'll end up with a lifetime of backache. The original battery clamping frames and the odd link lead clamp tend to corrode, so after a steamclean, the terminals are wire brushed and given a smear of vaseFine. Terberg DTS replaces the frame with a securing strap.
12 The Haulmajor's solid rear end is held together with four 25mm bolts at each side. One of these is inverted for assembly so DTS clamps the nut with a special tool and torques the bolt—the tightening setting is 1,000Nm. While underneath check the shoe lining to drum clearances via the small port in the brake backplate.