MAINTENANa
Page 56
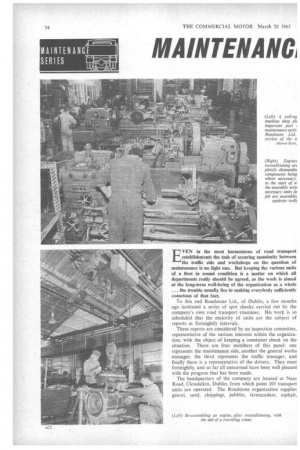
Page 57
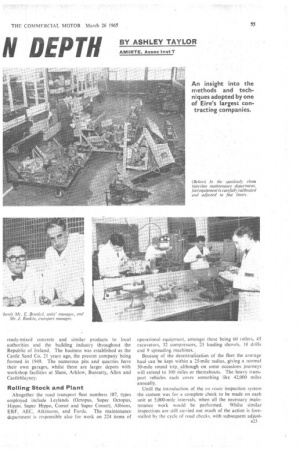
Page 58
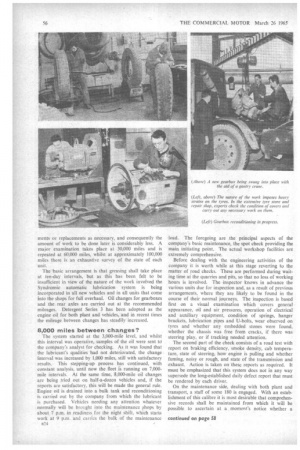
Page 60
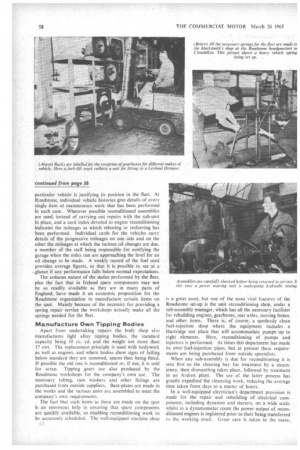
Page 61
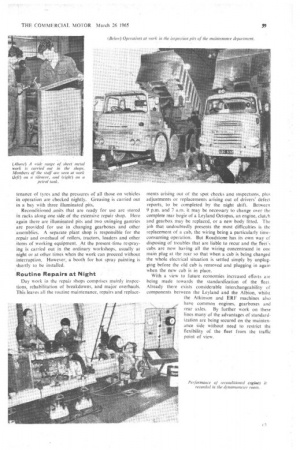
If you've noticed an error in this article please click here to report it so we can fix it.
N DEpTif BY ASHLEY TAYLOR
AMIRTE, Assoc lost T
EVEN in the most harmonious of road transport establishments the task of securing unanimity between the traffic side and workshops on the question of maintenance is no light one. But keeping the various units of a fleet in sound condition is a matter on which all departments really should be agreed, as the work is aimed at the long-term well-being of the organization as a whole ... the trouble usually lies in making everybody sufficiently conscious of that fact.
To this end RoadstoneLtd., of Dublin, a few months ago instituted a series of spot checks carried out by the company's own road transport examiner. His work is so scheduled that the majority of units are the subject of reports at fortnightly intervals.
These reports are considered by an inspection committee, representative of the various interests within the organization, with the object of keeping a consistent check on the situation. There are four members of this panel: one represents the maintenance side, another the general works manager, the third represents the traffic manager, and finally there is a representative of the drivers. They meet fortnightly, and so far all concerned have been well pleased with the progress that has been made.
The headquarters of the company are located at Naas Road, Clondalkin, Dublin, from which point 105 transport units are operated. The Roadstone organization supplies gravel, sand, chippings, pebbles, tarmacadam, asphalt, ready-mixed concrete and similar products to local authorities and the building industry throughout the Republic of Ireland. The business was established as the Castle Sand Co. 21 years ago, the present company being formed in 1949. The numerous pits and quarries have their own garages, whilst there are larger depots with workshop facilities at Slane, Arklow, Bunratty, Allen and Castleblayney.
Rolling Stock and Plant
Altogether the road transport fleet numbers 187, types employed include Leylands (Octopus, Super Octopus, Hippo, Super Hippo, Comet and Super Comet), Albions, ERF, AEC, Atkinsons, and Fords. The maintenance department is responsible also for work on 224 items of operational equipment, amongst these being 60 rollers, 45 eXcavators, 32 compressors, 23 loading shovels, 18 drills and 9 spreading machines. , Because, of the decentralization of the fleet the average haul can be kept within a 25-mile radius, giving a normal 50-mile round trip, although on some occasions journeys will extend to 100 miles or thereabouts. The heavy transport vehicles each cover something like 42,000 miles annually.
Until the introduction of the en route inspection system the custom was for a complete check to be made on each unit at 5,000-mile intervals, when all the necessary maintenance work would be performed. Whilst similar inspections are still carried out much of the action is forestalled by the cycle of road checks, with subsequent adjust
ments or replacements as necessary, and consequently the amount of work to be done later is considerably less. A major examination takes place at 30,000 miles and is repeated at 60,000 miles, whilst at approximately 100,000 miles there is an exhaustive survey of the state of each unit.
The 'basic arrangement is that greasing shall take place at ten-day intervals, but as this has been felt to be insufficient in view of the nature of the work involved the Syndrornic automatic lubrication system is being incorporated in all new vehicles and in all units that come into the shops for full overhaul. Oil changes for gearboxes and the rear axles are carried out at the recommended mileages. Detergent Series 3 has been adopted as the engine oil for both plant and vehicles, and in recent times the mileage between changes has steadily increased.
8,000 miles between changes?
The system started at the 3,000-mile level, and whilst this interval was operative, samples of the oil were sent td the company's analyst for checking. As it was found that the lubricant's qualities had not deteriorated, the change interval was increased by 1,000 miles, still with satisfactory results. This stepping-up process has continued, with constant analysis, until now the fleet is running on 7,000mile intervals. At the same time, 8,000-mile oil changes are being tried out on half-a-dozen vehicles and, if the reports are satisfactory, this will be made the general rule. Engine oil is drained into a bulk tank and reconditioning is carried out by the company from which the lubricant is purchased. Vehicles needing any attention whatever normally will be bro4,ht into the maintenance shops by about 7 p.m. in readiness for the night shift, which starts work at 9 p.m. and carri:s the bulk of the maintenance load. The foregoing are the principal aspects of the company's basic maintenance, the spot check providing the main initiating point. The actual workshop facilities are extremely comprehensive.
Before dealing with the engineering activities of the company it is worth while at this stage reverting to the matter of road checks. These are performed during waiting time at the quarries and pits, so that no loss of working hours is involved. The inspector knows in advance the various units due for inspection and, as a result of previous arrangements, where they are likely to be found in the course of their normal journeys. The inspection is based first on a visual examination which covers general appearance, oil and air pressures, operation of electrical and auxiliary equipment, condition of springs, hanger brackets, lubrication pipes and U-bolts, wear observed on tyres and whether any embedded stones were found, whether the chassis was free from cracks, if there was steering play, or if tracking needed attention.
The second part of the check consists of a road test with report on braking efficiency, smoke density, cab temperature, state of steering, how engine is pulling and whether fuming, noisy or rough, and state of the transmission and exhaust. Action is taken on these reports as required. It must be emphasized that this system does not in any way supersede the long-established daily defect report that must be rendered by each driver.
On the maintenance side, dealing with both plant and transport, a staff of some 180 is engaged. With an establishment of this calibre it is most desirable that comprehensive records shall be maintained from which it will be possible to ascertain at a moment's notice whether a
particular vehicle is justifying its position in the fleet. At Roadstone, individual vehicle histories give details of every single item of maintenance work that has been performed in each case. Wherever possible reconditioned assemblies are used, instead of carrying out repairs with the sub-unit in place, and a card index devoted to engine reconditioning indicates the mileages at which reboring or resleeving has been performed. Individual cards for the vehicles carry details of the progressive mileages on one side and on the other the mileages at which the various oil changes are due, a member of the staff being responsible for notifying the garage when the miles run are approaching the level for an oil change to be made. A weekly record of the fuel used provides average figures, so that it is possible to see at a ..glance if any performance falls below normal expectations.
The arduous nature of the duties performed by the fleet, 'plus the fact that in Ireland spare components may not be so readily available as they are in many parts of England, have made it an economic proposition for the Roadstone organization to manufacture certain items on the spot. Mainly because of the necessity for providing a spring repair service the workshops actually make all the springs needed for the fleet,
Manufacture Own Tipping Bodies
Apart from undertaking repairs the body shop also manufactures light alloy tipping bodies, the standard capacity being 18 cu. yd. and the weight not more than 17 cwt. The replacement principle is used with bodywork as well as engines, and where bodies show signs of falling below standard they are removed, spares then being fitted. If passible the old one is reconditioned or, if not, it is sold for scrap. Tipping gears are also produced by the Roadstone workshops for the company's own use. The necessary tubing, ram washers and other fittings are purchased from outside suppliers. Base-plates are made in the works and the various units are assembled to meet the company's own requirements.
The fact that such items as these are made on the spot is an enormous help in ensuring that spare components are quickly available, so enabling reconditioning work to be accurately scheduled. The well-equipped machine shop c2 is a great asset, but one of the most vital features of the Roadstone set-up is the unit reconditioning shop, under a sub-assembly manager, which has all the necessary facilities for rebuilding engines, gearboxes, rear axles, steering boxes, and other items. There is, of course, a spotlessly clean fuel-injection shop where the equipment includes a Hart ridge test plant that will accommodate pumps up to eight elements. Here, reconditioning of pumps and injectors is performed. At times this department has made its own' fuel-injection pipes, but at present these requirements are being purchased from outside specialists.
When any sub-assembly is due for reconditioning it is sent first to the cleaning bay for treatment by a steamjenny, then dismantling takes place, followed by treatment in an Ardrox plant. The use of the latter process has greatly expedited the cleansing work, reducing the average time taken from days to a matter of hours.
In a well-equipped electrician's department provision is made for the repair and rebuilding of electrical components, including dynamos and starters, on a wide scale, whilst in a dynamometer room the power output of reconditioned engines is registered prior to their being transferred to the working stock. Great care is taken in the main-,
tcnance of tyres and the pressures of all those on vehicles in operation are checked nightly. Greasing is carried out in a bay with three illuminated pits.
Reconditioned ,units that are ready for use are stored in racks along. one side of the extensive repair shop. , Here again there are illuminated pits and two swinging gantries are provided for use in Changing gearboxes and other assemblies. A separate plant shop is responsible for the .repair and overhaul of rollers, tractors, loaders and other items of working equipment. .At the present time respraying is carried out in the ordinary 'workshops, usually at night or at other tirtie.S when the work can proceed without interruption. 1-loweVer,a booth for hot spray painting is shortly to. be installed.
Routine Repairs at Night Day work in the repair shops comprises mainly inspections, rehabilitation of breakdowns, and major overhauls. This leaves all the routine maintenance, repairs and replace
ments arising out of the spot checks and inspections, plus adjustments or replacements arising out of drivers' defect reports, to he completed by the night shift. Between 9 p.m. and 7 a.m. it may be necessary to change over the complete rear bogie of a Leyland Octopus, an engine, clutch and gearbox may be replaced, or a new body fitted. The job that undoubtedly presents the most difficulties is the replacement of a cab, the Wiring being a particularly timeconsuming operation. But Roadstone has its own way of disposing of troubles that are liable to recur and the fleet's cabs are now having all the wiring concentrated in one main plug at the rear so that when a cab is being changed the whole electrical situation is settled simply by unplugging before the old cab is removed and plugging in again when the new cab is in place.
With a view to future economies increased efforts are being made towards the standardization of the fleet. Already there exists considerable interchangeability of components between the Leyland and the Albion, whilst the Atkinson and ERF machines also have common engines, gearboxes and rear axles. By further work on these lines many of the advantages of standardization are being secured on the maintenance side without need to restrict the flexibility of the fleet from the traffic point of view.