MECHANICALLY-LOADED ARTICS GIVE 50 PER CENT SAVING
Page 31
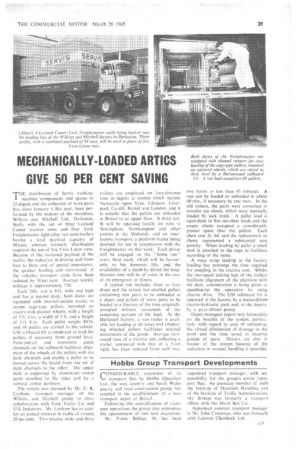
If you've noticed an error in this article please click here to report it so we can fix it.
j'HE distribution of Servis washing'. machine components and spares to 22 depots and the collection of worn parts has, since January 4 this year, been performed by the makers of the machines. Wilkins and Mitchell Ltd., Darlaston. Staffs, with the aid of three Leyland ,Comet tractive units and four York Freightmaster light-alloy van semi-trailers having a total payload capacity of 48 tons. whereas formerly distribution required the use of five 5-ton Luton vans. Because of the increased payload of the outfits, the reduction in driving staff from four to three and, of special importance, the quicker loading and turn-round of the vehicles, transport costs have been reduced by 50 per cent. Average weekly mileage is approximately 750.
Each 6ft, van is 8 ft wide and high and has a 'second deck; both decks are equipped with channel-section tracks to accept cage-type pallets, mounted on casters with plastics wheels, with a length of 3 ft. 6 in., a width of 2 ft. and a height of 3 ft. 8 in. Each pallet weighs 84 lb. and 48 pallets are carried in the vehicle. USI tailboard lift is employed to load the pallets, if necessary from ground level. Fore-and-aft and transverse guide channels on the tailboard facilitate alignment of the wheels of the millets with the deck channels and enable a pallet to he moved across the board from one set of deck channels to the other: The upper deck is supported by aluminium stump posts attached to the sides and by a vertical centre partition.
The system was planned by Mr. C. R. Lynham, transport manager of the Wilkins and Mitchell group. in close collaboration with York Trailer. Co. and U.S. Industries. Mr. Lynham has to eatei' for an annual increase in. traffic of around 20 per cent. Two tractive units and three
trailers are employed on long-distance runs to depots at centres which include Newcastle upon Tyne, Glasgow, Liverpool. Cardiff, Bristol and London, and it is notable that the pallets are unloaded at Bristol to an upper floor. A third outfit will be operated locally on runs to Nottingham. Northampton and other centres in the Midlands, and on interfactory transport, a platform trailer being destined for use in conjunction with the Freightmaster on this work. Each driver will be engaged on the " home run" every third week, wlUch will be favourable to his domestic life, and the availability of a stand-by driver for longdistance runs Will be of value in the case of an emergency or illness.
A typical run includes three to four drops and the system has enabled pallets containing new parts to be unloaded at a depot and pallets of worn parts to be loaded in a fraction of the time originally occupied without ' movement of the remaining sections of the load, At the Darlaston factory, a van trailer is available for loading at all times and employing wheeled pallets facilitates internal movements of the goods. Average turnround time of a tractive unit collecting a trailer, compared with that of a 5-ton rigid, has been reduced from well over two hours to less than 45 minutes. A van can be loaded or unloaded in about 40 min., if necessary by one man. In the old system, the parts were contained in wooden tea chests, which were manually loaded by sack truk. A pallet load is equivalent to five tea-chest loads and the empty chests occupied a considerably greater space than the pallets. Each chest cost 2s. 6d. and the replacement of chests represented a substantial cost penalty. When loading by. pallet a small desk is attached to the cage to facilitate recording of the items.
A steep ramp leading to the factory loading bay prolongs the time required for coupling to-the tractive unit. Whilst the two-speed jacking legs of the trailers facilitate alignment of the platform with the deck, consideration is being given to speeding-up the operation by using electric drive. The US1 tailboard lift is operated at the factory by a mains-driven electro-hydraulic pack and, at the depots, by a p.t.o.-driven pump.
Depot managers report very favourably on the benefits of the system, particularly with regard to ease of unloading, the virtual elimination of damage to the parts and the time saved in locating groups of parts. Drivers are also in favour of the system because of the reduction in manual handling it provides.