Rust has eleetrit shock treatment
Page 80
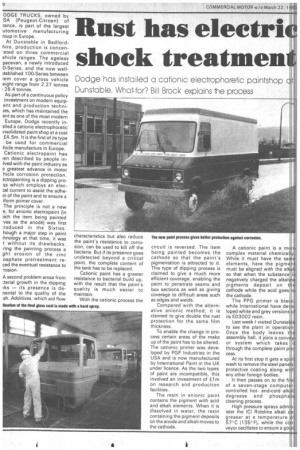
Page 81
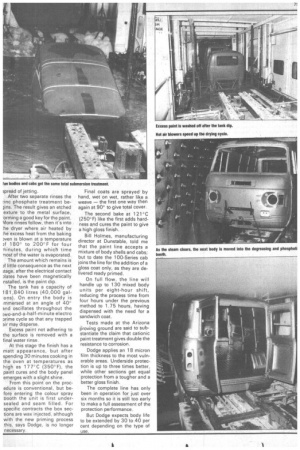
If you've noticed an error in this article please click here to report it so we can fix it.
Dodge has installed a cationic electrophoretic paintshop at Dunstable. What-for? Bill Brock explains the process
ODGE TRUCKS, owned by SA (Peugeot-Citroen) of rance, is part of the largest utomotive manufacturing roup in Europe.
At Dunstable in Bedfordhire, production is concen:ated on three commercial ehicle ranges. The ageless pacevan, a newly introduced 0-Series, and the now well;tablished 100-Series between iem cover a gross vehicle eight range from 2.27 tonnes , 26.4 tonnes.
As part of a continuous policy investment on modern equipent and production techniJes, which has maintained the ant as one of the most modern Europe, Dodge recently inailed a cationic electrophoretic insolidated paint shop at a cost £4.5m. It is the first of its type be used for commercial hide manufacture in Europe. Cationic electropaint has ien described by people inlved with the paint industry as e greatest advance in motor hide corrosion protection. )ctropainting is a dipping pross which employs an elec2„al current to assist the adhein of the paint and to ensure a iform primer cover.
The principle is not a new e, for anionic electropaint (in lich the item being painted 'yes as the anode) was first :roduced in the Sixties. hough a major step in paint :hnology at that time, it was t without its drawbacks. ring the painting process a ght erosion of the zinc osphate pretreatment reced the eventual resistance to Tosion.
A second problem arose from terial growth in the dipping iks — its presence is denental to the quality of the sh. Additives, which aid flow characteristics but also reduce the paint's resistance to corrosion, can be used to kill off the bacteria. But if its presence goes undetected beyond a critical point, the complete content of the tank has to be replaced.
Cationic paint has a greater resistance to bacterial build up, with the result that the paint's quality is much easier to maintain.
With the cationic process the circuit is reversed. The item being painted becomes the cathode so that the paint's pigmentation is attracted to it. This type of dipping process is claimed to give a much more efficient coverage, enabling the paint to penetrate seams and box sections as well as giving coverage to difficult areas such as edges and welds.
Compared with the alternative anionic method, it is claimed to give double the rust protection for the same film thickness.
To enable the change in process certain areas of the make up of the paint has lobe altered. The cationic primer was developed by PGP Industries in the USA and is now manufactured by International Paint in the UK under licence. As the two types of paint are incompatible, this involved an investment of Lim on research and production facilities.
The resin in anionic paint contains the pigment with acid and alkali elements. When it is dissolved in water, the resin containing the pigment deposits on the anode and alkali moves to the cathode. A cationic paint is a mor complex material chemically While it must have the sam elements, here the pigmen must be aligned with the alka so that when the substance i negatively charged the alkalin pigments deposit on th cathode while the acid goes t the cathode.
The PPG primer is black while International have deve loped white and grey versions o its ED3002 resin.
Last week I visited Dunstabl to see the plant in operation Once the body leaves th assembly hall, it joins a conve or system which takes through the complete paint pro cess.
At its first stop it gets a spini wash to remove the steel panels protective coating along wit any other foreign bodies.
It then passes on to the firs of a seven-stage computer controlled hotand-cold alkal degrease and phosphat cleaning process.
High pressure sprays admin ister the ICI Ridoline alkali de greaser at a temperature o 57" C (135 F), while the con veyor oscillates to ensure a goo
After two separate rinses the Einc phosphate treatment bejins. The result gives an etched :exture to the metal surface, :orming a good key for the paint. Vlore rinses follow, then its into :he dryer where air heated by :he excess heat from the baking pven is blown at a temperature )f 180' to 200°F for four -ninutes, during which time 'nest of the water is evaporated.
The amount which remains is )f little consequence as the next 3tage, after the electrical contact 3lates have been magnetically nstalled, is the paint dip.
The tank has a capacity of 181,840 litres (40,000 gallons). On entry the body is immersed at an angle of 40c and oscillates throughout the two-and-a-half-minute electro prime cycle so that any trapped air may disperse.
Excess paint not adhering to the surface is removed with a final water rinse.
At this stage the finish has a matt appearance., but after spending 30 minutes cooking in the oven at temperatures as high as 177cC (350°F), the paint cures and the body panel emerges with a slight shine.
From this point on the procedure is conventional, but be fore entering the colour spray booth the unit is first undersealed and seam filled. For specific contracts the box sections are wax injected, although with the new priming process this, says Dodge, is no longer necessary. Final coats are sprayed by hand, wet on wet, rather like a . weave — the first one way then again at 90° to give total cover.
The second bake at 121°C (250°F) like the first adds hardness and cures the paint to give a high gloss finish, Bill Holmes, manufacturing director at Dunstable, told me that the paint line accepts a mixture of body shells and cabs; but to date the 100-Series cab joins the line for the addition of a gloss coat only, as they are delivered ready primed.
On full flow, the line will handle up to 130 mixed body units per eight-hour shift, reducing the process time from four hours under the previous method to 1.75 hours, having dispensed with the need for a sandwich coat.
Tests made at the Arizona p-roving ground are said to substantiate the claim that cationic paint treatment gives double the resistance to corrosion.
Dodge applies an 18 micron film thickness to the most vulnerable areas. Underside protection is up to three times better, while other sections get equal protection from a tougher and a better gloss finish.
The complete line has only been in operation for just over six months so it is still too early to make a full assessment of the protection performance.
But Dodge expects body life to be extended by 30 to 40 per cent depending on the type of use.