From the Eli - owing Boor
Page 72
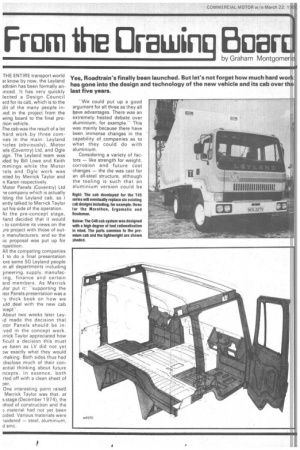
Page 73

If you've noticed an error in this article please click here to report it so we can fix it.
by Graham Montgomeri
THE ENTIRE transport world st know by now, the Leyland )dtrain has been formally aninced. It has very quickly lected a Design Council aid for its cab, which is to the dit of the many people infed in the project from the wing board to the final pro:tion vehicle.
che cab was the result of a lot hard work by three cornlies in the main: Leyland -lidos (obviously), Motor iels (Coventry) Ltd, and Ogle 3ign. The Leyland team was ided by Bill Lowe and Keith mrnings while the Motor leis and Ogle work was 3cted by Merrick Taylor and
n Karen respectively.
Motor Panels (Coventry) Ltd le company which is actually !ding the Leyland cab, so I ently talked to Merrick Taylor Alt his side of the operation. At the pre-concept stage, 'land decided that it would to combine its views on the Jre project with those of out • manufacturers, and so the iic proposal was put up for npetition.
All the competing companies 1 to do a final presentation ore some 50 Leyland people m all departments including jineering, supply, manufacing, finance and certain aid members. As Merrick flor put it -supporting the itor Panels presentation was a -y thick book on how we uld cleal with the new cab -wept'.
About two weeks later Ley made the decision that )tor Panels should be inNied in the concept work. irriok Taylor appreciated how ficult a decision this must ve been as LV did not yet Dw exactly what they would making. Both sides thus had disclose much of their conential thinking about future ncepts. In essence, both rted off with a clean sheet of per.
One interesting point raised Merrick Taylor was that, at s stage (December 1974), the ithod of construction and the • material had not yet been cided. Various materials were lsidered — steel, aluminium, d smc.
-We could put up a good argument for all three as they all have advantages. There was an extremely heated debate over aluminium, for example,'" This was mainly because there have been immense changes in the capability of companies as to what they could do with aluminium.
Considering a variety of factors — like strength for weight, corrosion and future cost changes — the die was cast for an all-steel structure, although the tooling is such that an aluminium version could be produced if needed in the future.
At this stage a very stringent brief was put together. At Leyland's request, because the time scale was tight, the brief was put out to competition for external styling.
Entries came from four sources: the Austin Morris styling department, Ogle, John Beck (who at that time worked at Leyland Truck and Bus), and Lionel Sherrow (who had previously done some styling work for Scania). Ogle Design of Letchworth ended up as winners and, with only minor changes, their design went forward into the project plan.
At this stage Motor Panels asked (not unreasonably) to be involved in the styling with Ogle, as the Coventry company was, after all, eventually going to be responsible for making the cab. Thus Motor Panels and Ogle got together for what Merrick Taylor described as a "'hairraising four weeks to develop the exterior style".
One of the most significant variations in style between C40 and the opposition lies in the use of curved glass. According to Merrick Taylor, no commercial vehicle on the road used other than flat glass at the sides and back of the cab. This was one area where car technology and experience could be put to good use in order to present a smoother and more rounded, and hence less aggressive, image.
Another important move was the gentle curve upwards at the side of the cab below the side window. This was done for a number of reasons. It reduced the amount of glass needed in the cab and there was little reduction in visibility as the relevant section was behind the driver.
If reducing the amount of glass seems an odd idea, remember that glass is very heavy (the C40 windscreen weighs 561b, for example) and so reducing it kept the weight and the cost down as well as keeping the required styling.
If a normal control version of the C40 is produced, then the problem of blending a horizontal line with a sloping bonnet is already removed.
One of Merrick Taylor's hobby horses, if I can phrase it like that, is to try to get the benefit of the graphic schemes which are becoming available. It is in this area that the sloping line can again be useful.
He strOngly believes that the technical differences between
one make of chassis and an are getting less and so E which can give a graphic in has a major advantage.
The thinking beyond th that a large number of veh in a "dramatic—livery on t. operation can be a useful motion ploy.
One thing which Leylar particularly proud of is amount of work the various ties involved have put in or subject of corrosion proven One of the problems here is box sections should be tilated to help cut down on rosion, and thus a structu open sections would be answer. However a closed
section (or a tube) is far stro
and is necessary for high s areas like the screen pillars. For such areas whei closed section was necessar
strength, vent areas have I
provided for the pre-treatr and paint dip. The anti-corrc
measures included wax COE in the box sections plus con tional undersealing with thE of zinc coated steels in straareas.
The C40 cab was desil with a high degree of ratii isation in mind for the too Thus the wide cab and the y be announced "narrow" ca the lighter models have a c parts commonality.
Of the approximately major sets of tools used to duce the 16.28 Roadtrain about 85 per cent will be I on the smaller version. parts uniformity has beer tended to the interior as we the accompanying diagr shown.
Roadtrain is available Leyland fully painted, not ju primer — a major step in fight against corros Although this might see simple move on the face of was defintely not so eas practice.
The design team spen less than two years befo arrived at a satisfactory p specification; one which practical and could be prodi consistently. Merrick Ta recalled: "In many cases, required technology just
there at the time. It was a q tion of analysing opportun
as they became available," tainly the Leyland / M Panels/Ogle team feels it been setting the pace in area.
The new vehicle and its deserve to succeed if only fo amount of hard work that been put in over the last years.