HAULIER 0 Who Should Carr
Page 26
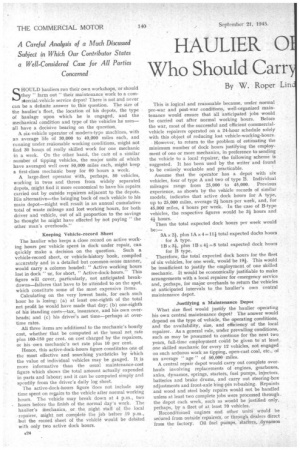
Page 27
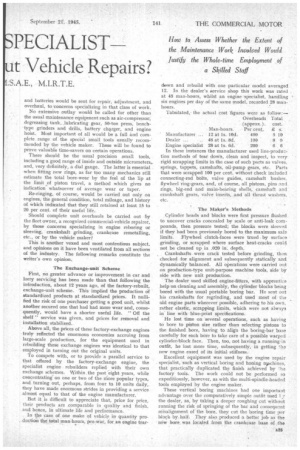
Page 28
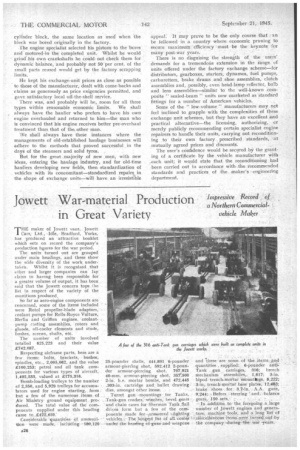
If you've noticed an error in this article please click here to report it so we can fix it.
EPECIALIST September 21, 1945 t Vehicle Repairs.
By W. Roper Lin
I.S.A.E., M.I.R.T.E.
A Careful Analysis of a Much Discussed Subject in Which Our Contributor States a Well-Considered Case for All Parties Concerned
Ho w to. Assess Whether the Extent of the Maintenance Work Involved Would Justify the Whole-time Employment of a Skilled Staff
SHOULD hauliers run their own workshops, or should they "farm out" their maintenance work to a cornniercial-vehicle service depot? There is not and never can be a definite answer to this question. The size of the haulier's fleet, the location of his depots, the type of haulage upon which he is engaged, and the mechanical condition and type of the vehicles he uses— all have a decisive bearing on the question.
A six-vehicle operator of modern-type machines, with an average life of 30,000 to 40,000 miles each, and running under realonable working conditions, might not find 30 hours of really skilled work for one mechanic in a week. On the other hand, the care of a similar number of tipping vehicles, the major units of which have averaged well over 50,000 miles each, might keep a first-class mechanic busy for 60 hours a week.
A large-fleet operator with, perhaps, 50 vehicles, working in twos and threes from widely separated depots, might find it more economical to have his repairs carried out by outside repairers adjacent to the depots. His alternative—the bringing back of each vehicle tO his main depot—might well result in an annual cumulative total of waste mileage and lost working hours, for both driver and vehicle, out of all proportion to the savings he thought he might have effected by not paying "the other man's overheads."
Keeping Vehicle-record Sheet The haulier who keeps a close record on active working hours per vehicle spent in dock under repair, can quickly make a decision on the question. Such a vehicle-record sheet, or vehicle-history book, compiled accurately and in a detailed but common-sense manner, would carry a column headed: " Active working hours lost in dock" or, for short, " Active-dock-hours." This figure will cover, particularly, not anticipated breakdowns—failures that have to be attended to on the spot, which constitute some of the most expensive items.
Calculating on the very lowest basis, for each such hour he is losing: (a) at least one-eighth of the total net profit he would have made that day; (b) one-eighth of his 'standing costs—tax, insurance, and his own overheads; and (c) his driver's net time—perhaps at overtime rates.
All three items are additional to the mechanic's hourly cost, whether that be computed at the 'usual net rate plus 100-150 per cent. on cost charged by the repairers, or his own mechanic's net rate plus 10 per cent.
Hence, this active-dock-hours figure constitutes one of the most effective and searching yardsticks by which the value of individual vehicles may be gauged. It is more informative than the usual maintenance-cost figure which shows the total amount actually expended in parts and labour; and it can be computed simply and speedily from the driver's daily log sheet.
The active-dock-hours figure 'does not include any time spent on repairs to the vehicle after normal working hours. The vehicle may break down at 4 p.m., two hours before the finish of the normal day's work. The haulier's mechanics, or .the night staff of the local • repairer, might not complete the job before 10 p.m., but the record sheet of the vehicle would be debited with only two active dock hours.
.24 • This is logical and reasonable because, under normal pre-war and post-war conditions, well-organized maintenance would ensure that all anticipated jobs would be carried out after normal working hours. Before the war, most of the successful and efficient commercialvehicle repairers operated on a 24-hour schedule solely with this object of reducing lost vehicle-working-hours.
However, to return to the problem of estimating the minimum number of dock hours justifying the employment of one or more mechanics, in preference to sending the vehicle to a local fepairer; the following scheme is suggested. It has been used by the writer and found to be entirely workable and practicable. • Assume that the operator has a depot with six vehicles, four of type A and two of type B. Individual mileages range from 25,000 to 45,000. Previous experience, as shown by the yehicle records of similar models, indicates that active dock hours for A type. up to 25,000 miles, average 2/ hours per week, and, for 45,000 miles, 4 hours per week. In the case of B-type vehicles, the respective figures would be 3i hours and 4/ hours. "
Then the total expected dock hours per week would be:—
3A x 2, plus lA x 4=11/ total expected docks hours for A type.
1B x 3, plus 1B x 4 =8 total expected dock hours
for B type. • Therefore, the total expected dock hours for the fleet of six vehicles, or one week, would be l9. This would be insufficient to justify the employment of one skilled mechanic. It would be economically justifiable to make arrangements with a local repairer for emergency service and, perhaps, for major overhauls to return the vehicles at anticipated intervals to the haulier's own central maintenance depot.
Justifying a Maintenance Depot • What size fleet would justify the haulier operating his own central maintenance depot? The answer would depend on the type of vehicle, the operating conditions, and the availability, size, and efficiency of the local repairer. As a general rule, under prevailing conditions, such as may be presumed to continue for the next two years, full-time employment could be given to at least one skilled mechanic for every 12 vehicles, not engaged on such arduous work as tipping, open-cast coal, etc., of an average " age " of 50,000 miles.
A central repair depot would carry out complete overhauls involving replacements of engines, gearboxes, axles, dynamos, springs, starters, fuel pumps, injectors. batteries and brake drums, and carry out steering-box adjustments and front-axle king-pin rebushing. Repaints and wood and steel body repairs would not be handled unless at least two complete jobs were processed through, the depot each week, such as would be justified only. perhaps, by a fleet of at least 70 vehicles. Reconditioned engines and other units would be seCured from outside repairers, or through, dealers direct from the factory. Oil fuel pumps, starters, .dynamos and batteries would be sent for repair, adjustment, and overhaul, to concerns specializing in that class of work.
No extensive outlay would be called for other than the usual maintenance equipment such as air-compressor: degreasing tank, _lubricating gear, 50-ton press, benchtype grinders and drills, battery chvger, and engine hoist. Most important of all would be a full and complete range of the special small tools usually recommended by the vehicle maker. These will be found to prove valuable time-savers on certain operations.
There should be the usual precision small tools, including a good range of inside and outside micrometers... and, very definitely, a dial gauge. The latter is essential when fitting new rings, as far too many mechanics still estimate the total bore-wear by the feel of the lip at the limit of piston travel, a method which gives no indication whatsoever of average wear or taper.
Re-ringing, of course, would be carried out only on engines, the general condition, total mileage, and history of which indicated that they still retained at least 15 to 20 per cent. of their useful life.
Should complete unit overhauls be carried out by the fleet owner, a recognized commercial-vehicle repairer, by those concerns specializing in engine reboring or sleeving, crankshaft grinding, crankcase remetalling, etc., or by the vehicle maker?
This is another vexed and most contentious subject. and opinions on it have been ventilated from all sections of the industry. The following remarks constitute the writer's Own opinion.
The Exchange-unit Scheme First, no greater advance or improvement in car and lorry servicing has been made than that following the introduction, about 12 years ago, of the factory-rebuilt, exchange-unit scheme. This implied the production Of standardized products at standardized prices. It nullified the risk of one purchaser getting a good unit, whilst another secured one that had had more wear and, consequently, would have a shorter useful life. "Off the shelf" service was given, and prices for removal and installation stabilized.
Above all, the prices of these factory-exchange engines truly reflected the enormous economies accruing from large-scale production, for the equipment used in rebuilding these exchange engines was identical to that employed in turning Out the original units.
To compete with, or to provide a parallel service to that offered by the factory-exchange engine, the specialist engine rebuilders replied with their own exchange schemes. Within the past eight years, while concentrating on one or two of the rnore popular types, and turning out, perhaps, from four to 10 units daily, they have made enormous strides in providing a service almost equal to that of the engine manufacturer.
But it is difficult to appreciate that, price for price, their products are comparable in quality and finish, and hence, in ultimate life and performance.
In the case of one make of vehicle in quantity production the total man-hours, pre-war, for an engine tear
down and rebuild with one particular model averaged 12. In the dealer's service shop this work was rated at 48 man-hours, whilst an engine specialist, handling six engines per day of the same model, recorded 28 manhours.
Tabulated,the actual cost figures were as follow:—
Overheads. Total (approx.). cost.
Man-hours. Per cent. £ s.
Manufacturer ... 12 at ls. 10d. 400 5 10 Dealer ... .. 48 at is. 8d. 100 8 0 Engine Specialist 28 at 1s. Gd. 200 6 6 In these instances the manufacturer used line-produc tion methods of tear down, clean and inspect, to very rigid scrapping limits in the case of such parts as valves, springs, tappets, camshafts, oil-pump gears, etc. Parts that were scrapped 100 per cent, without check included connecting-rod bolts, valve guides, camshaft bushes, flywheel ring-gears, and, of course, all pistons, pins and rings, big-end and main-bearing shells, camshaft and crankshaft gears, valve inserts, and all thrust washers, etc.
The Maker's Methods Cylinder heads and blocks were first pressure flushed to uncover cracks concealed by scale or anti-leak compounds, then pressure tested; the blocks were sleeved if they had been previously bored to the maximum safe limits. Flywheel clutch-faces were trued . by surface grinding, or scrapped where surface heat-cracks could not be cleaned up in .020 in. depth.
, Crankshafts were crack tested before grinding, then checked for alignment and subsequently statically and dynamically balanced. All operations were carried out on production-type unit-purpose machine tools, side by side with new unit production.
The dealer used skilled engine-fitters, with apprentice help on cleaning and assembly, the Cylinder blocks being bored with the usual portable boring bar. He sent out his crankshafts for regrinding, and used most of the old engine parts wherever possible, adhering to his own, rather elastic, scrapping limits, which were not always in line with blue-print specifications.
He lost time on several operations, such as having to bore to piston size rather than selecting pistons to the finished bore, having to align the boring-bar base carefully for each bore to take care of a possible warped cylindersblock face. Then, too, not having a running-in outfit, he lost more time, subsequently, in getting the new engine eased of its initial stiffness.
Excellent equipment was used by the engine repair specialist, such as vertical boring and honing rlachines, that practically duplicated the finish achieved by he factory tools. The work could not be performed so expeditiously, however, as with the multi-spindle-headed tools employed by the engine maker.
These vertical boring machines had one important advantage over the comparatively simple outfit used 1 the dealer, as, by taking a deeper roughing cut without running the risk of springing of the bar and consequent MiSalignment of the bore, they cut the boring time per block by half. They also produced a better job as the new bore, was loca,ted frond the crankcase base of the
cylinder block, the same location as used when the block was bored originally in the factory.
The engine specialist selected his pistons to the bores and motored-in the completed. unit. Whilst he would grind' his own crankshafts he could not check them for dynamic balance and probably not 50 per cent. of the small parts reused would get by the factory scrapping imits.
He kept his exchange-unit prices as close as possible to those of the manufacturer, dealt with come-backs and claims as generously as price exigencies permitted, and gave satisfactory local off-the-shelf service.
There was, and probably Will be, room for all three types within reasonable economic limits. We shall always have the haulier who prefers to have his own engine overhauled and returned to him—the man who is convinced that his engine receives better pre-overhaul treatment than that of the, other man.
We shall always have these instances where the managements of old-established haulage businesses will adhere to the methods that proved successful, in the days of the steamers and solid tyres.
But for the great -majority of new _men, with new ideas, entering the haulage industry, and for old-time hauliers developing new fields, then standardization of vehicles. with its concomitant—standardized repairs in the shape of exchange units—willhave an irresistible appeal. It may prove to be the only course that an he followed in a country where economic pruning to Secure 'maximum efficiency must be the keynote -for
many post-war years. •
There is no disguising the strength of the users' demands for a tremendous extension in the range of units offered under the factory exchange scheme—for distributors, gearboxes, starters, dynamos, fuel pumps, carburetters, brake drums and shoe assemblies, clutch assemblies and, .possibly, even head-lamp reflector, bulb and lens assemblies—similar to the well-known composite " sealed-beam " units now -marketed as standard fittings for a number of American vehicles.
Some of the " low-volume " manufacturers may not fee] inclined to grapple with the complexities of these exchange unit schemes, but they have an -excellent and practical alternative—the licensing, authorizing, or merely publicly recommending certain specialist engine repairers to handle their units, .carrying out reconditioning to. their own factory prescribed standards, at mutually agreed prices and discounts.
The user's confidence Would be secured by the granting of a certificate by the vehicle manufacturer with ,each unit; it would state that the reconditioning had been carried out in accordance with the recommended standards and practices of file maker's engineering department.