DAF gears up for automatic
Page 25
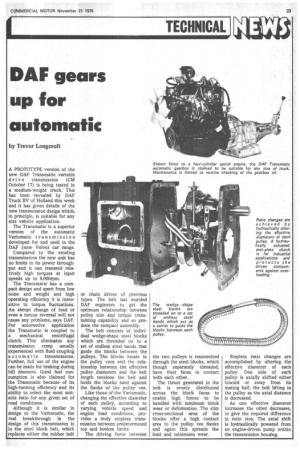
If you've noticed an error in this article please click here to report it so we can fix it.
by Trevor Longeroft
A PROTOTYPE version of the new DAF Transmatic variable drive transmission (CM October 17) is being tested in a medium-weight truck. This has been revealed by DAF Truck BV of Holland this week and it has given details of the new transmission design which, in principle, is suitable for any size vehicle 'application.
The Transmatic is a superior version of the automatic Variomatic transmission developed for and used in the DAF (now Volvo) car range.
Compared to the existing transmissions the new unit has no limits to its power throughput and it can transmit relatively high torques at input speeds up to 8,000rpm.
The Transmatic has a compact design and apart from low noise and weight and high operating efficiency it is insensitive to torque. fluctuations. An abrupt change of load or even a torque reversal will not cause any problems, says DAF. For automotive application the Transmatic is coupled to a mechanical centrifugal clutch. This eliminates any transmission creep usually experienced with fluid coupling automatic transmissions. Further, full use of the engine can be made for braking during hill descents. Good fuel consumption ;is also claimed for the Transmatic because of its high-running efficiency and its ability to select the most suitable ratio for any given set of road conditions.
Although it is similar in design to the Variomatic, the real breakthrough in the design of this transmission is in the steel block belt, which replaces either the rubber belt or chain drives of previous types. The belt has enabled DAF engineers to get the optimum relationship between pulley size and torque transmitting capability and so produce the compact assembly.
The belt consists of individual wedge-shape steel blocks which are threaded on to a set of endless steel bands that guide the blocks between the pulleys. The blocks locate in the pulley vees and the relationship between the effective pulley diameters and the belt length tensions the belt and holds the blocks hard against the flanks of the pulley vee.
Like those of the Variomatic, changing the effective diameter of each pulley, according to varying vehicle speed and engine load conditions, provides a truly stepless transmission between predetermined top and bottom limits.
The driving force between the two pulleys is transmitted through the steel blocks, which though separately threaded, have their faces in contact with each other.
The thrust generated in the belt is evenly distributed across the block faces to enable high forces to be handled with minimum block wear or deformation. The slim cross-sectional area of the blocks offer a high contact area to the pulley vee flanks and again this spreads the load and minimises wear. Stepless ratio changes are accomplished by altering the effective diameter of each pulley. One side of each pulley is axially shifted either toward or away from its mating half, the belt lifting in the pulley as the axial distance is decreased.
As one effective diameter increases the other decreases, to give the required difference in ratio step. The axial shift is hydraulically powered from an engine-driven pump within the transmission housing.