Long Wheelba! Tippers CAN be Safe
Page 58
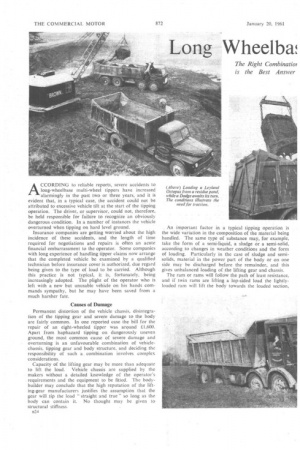
Page 59
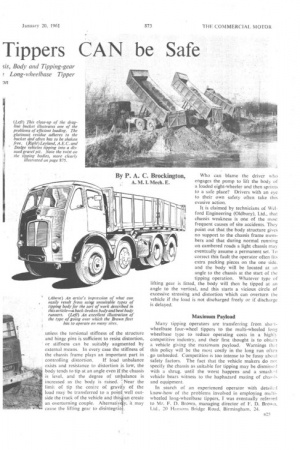
Page 60
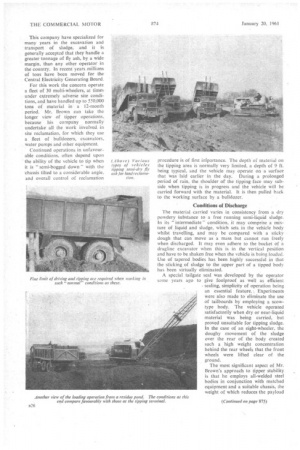
Page 63
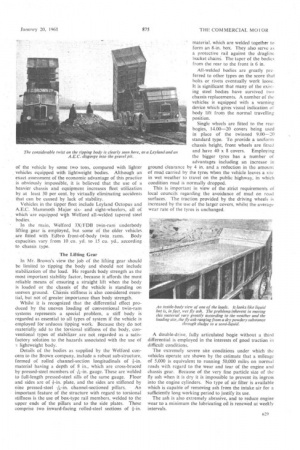
If you've noticed an error in this article please click here to report it so we can fix it.
The Right Cornbinatior is the Best Answer
ACCORDING to reliable reports, severe accidents to long-wheelbase multi-wheel tippers have increased alarmingly in the past two or three years, and it is evident that, in a typical case, the accident could not be attributed to excessive vehicle tilt at the start of the tipping operation. The driver, or supervisor, could not, therefore, be held responsible for failtire to recognize an obviously dangerous condition. In a number of instances the vehicle overturned when tipping on hard level ground.
Insurance companies are getting worried about the high incidence of these accidents, and the length of time required for negotiations and repairs is often an acute financial embarrassment to the operator. Some companies with long experience of handling tipper claims now arrange that the completed vehicle be examined by a qualified technician before insurance cover is authorized, due regard being given to the type of load to be carried. Although this practice is not typical, it is, fortunately, being increasingly adopted. The plight of the operator who is left with a new but unusable vehicle on his hands commands sympathy, but he may have been saved from a much harsher fate.
Causes of Damage
Permanent distortion of the vehicle chassis, disintegration of the tipping gear and severe damage to the body are fairly common. In one reported case the bill for the repair of an eight-wheeled tipper was around £1,600. Apart from haphazard tipping on dangerously uneven ground, the most common cause of severe damage and overturning is an unfavourable combination of vehiclechassis, tipping gear and body structure, and deciding the responsibility of such a . combination involves complex considerations.
Capacity of the lifting gear may be more than adequate to lift the load. Vehicle chassis are supplied by the makers without a detailed knowledge of the operator's requirements and the equipment to be fitted. The bodybuilder may conclude that the high reputation of the lifting-gear manufacturers justifies the assumption that the gear will .tip the load " straight and true" so long as the body can contain it. No thought may be given to structural stiffness. An important factor in a typical tipping operation is the wide variation in the composition of the material being handled. The same type of substance may, for example, take the form of a semi-liquid, a sludge or a semi-solid, according to changes in weather conditions and the form of loading. Particularly in the case of sludge and semisolids, material in the power part of the body or on one side may be discharged before the remainder, and this gives unbalanced loading of the lifting gear and chassis.
The ram or rams will follow the path of least resistance, and if twin rams are lifting a lop-sided load the lightlyloaded ram will lift the body towards the loaded section, unless the torsional stiffness of the structure and hinge pins is sufficient to resist distortion, or stiffness can be suitably augmented by external means. In every case the stiffness of the chassis frame plays an important part in
controlling distortion. If load unbalance exists and resistance to distortion is low, the body tends to tip at an angle even if:the chassis is level, and the degree of unbalance is increased as the body is raised. 'Near the limit of tip the centre of gravity of the load may be transferred to a polo _well outside the track of the vehicle and this an create an overturning couple. Alternatiy, y, it may cause the lifting gear to disintegrat .
Who can blame the driver who engages the pump to lift the body of a loaded eight-wheeler and then sprints to a safe place? Drivers with an eye to their own safety often take this evasive action.
It is claimed by technicians of Wetford Engineering (Oldbury), Ltd., that chassis weakness is one of the most frequent causes of site accidents. They point out that the body structure gives no support to the chassis frame members and that during normal running on cambered roads a light chassis may eventually assume a permanent set. in correct this fault the operator often fits extra packing pieces on the one side. and the body will be located at an angle to the chassis at the start of the tipping operation. Whatever type of lifting gear is fitted, the body will then be tipped at an angle to the vertical, and this starts a vicious circle of excessive stressing and distortion which can overturn the vehicle if the load is not discharged freely or if discharge is delayed.
•
1 mffi 11111 •111 iti ",
Maximum Payload Many tipping operators are transferring from shortwheelbase four-wheel tippers to the multi-wheeled long wheelbase type to reduce operating costs in a highly competitive industry, and their first thought is to obtail a vehicle giving the maximum payload. Warnings that this policy will be the most costly in the tong run ofien go unheeded. Competition is too intense to be fussy about safety factors. The fact that the vehicle makers do not specify the chassis as suitable for tipping may be dismissed with a shrug, until the worst happens and a smash‘d vehicle bears witness to the haphazard mating of chas,:k and equipment.
In search of an experienced operator with detailc.1 know-how of the problems involved in employing mullwheeled long-wheelbase tippers, I was eventually referred to Mr. F. D. Brown, managing director of F. D. Brown, Ltd., 20 Hansons Bridge Road, Birmingham, 24. This company have specialized for many years in the excavation and transport of sludge, and it is generally accepted that they handle a greater•tonnage of fly ash, by a wide margin, than any other operator in the country. In recent years millions of tons have been moved for the Central Electricity Generating Board.
For this work the concern operate a fleet of 30 multi-wheelers, at times under extremely adverse site conditions, and have handled up to 550.000 tons of material in a 12-month period. Mr. Brown can take the longer view of tipper operations, because his company normally undertake all the work involved, in site reclamation, for which they use a fleet of bulldozers, excavators, water pumps and other equipment.
Continued operations in unfavourable conditions, often depend upon the ability of the vehicle to tip when it is "semi-bogged down" with the • chassis tilted to a considerable angle, and overall control of reclamation
procedure is of first iniportance. The depth of material on the tipping area is normally very limited, a depth of 9 ft. being typical, and the vehicle may operate on a surface that was laid earlier in the day. During a prolonged period of rain, the shoulder of the tipping face may subside when tipping is in progress and the vehicle will be carried forward with the material. It is then pulled back to the working surface by a bulldozer.
Conditions of Discharge
The material carried varies in consistency from a dry powdery Substance to a free running semi-liquid sludge. In its " intermediate " condition, it may comprise a mixture Of liquid and sludge, which sets in the vehicle body whilst travelling, and may be compared with a sticky dough that can move as a mass but cannot run freely when discharged. It may even adhere to the bucket of a dragline excavator when this is in the vertical position and have to be shaken free when the vehicle is being loaded. Use of tapered bodies has been highly successful in that the sticking of sludge to the upper part of a tipped body has been virtually eliminated.
A special tailgate seal was developed by the operator some years ago to give foolproof as well as efficient sealing, simplicity of operation being an essential feature. , Experiments were also made to eliminate the use of tailboards by employing a scowtype body. The vehicle operated satisfactorily when dry or near-liquid material was being carried, but proved unsuitable for tipping sludge. In the case of an eight-wheeler, the doughy movement of the sludge over the rear of the body created such a high weight concentration behind the rear wheels that the front wheels were lifted clear of the ground.
The most significant aspect of Mr. Brown's approach to tipper stability is that he employs all-welded steel bodies in conjunction with matched equipment and a suitable chassis, the weight of which reduces the payload of the vehicle by some two tons, compared with lighter vehicles equipped with lightweight bodies. Although an exact assessment of the economic advantage of this practice is obviously impossible, it is believed that the use of a heavier chassis and equipment increases fleet utilization by at least 30 per cent. by virtually eliminating accidents that can be caused by lack of stability.
Vehicles in the tipper fleet include Leyland Octopus and A.E.C. Mammoth Major sixand eight-wheelers, all of which are equipped wii,h Welford all-welded tapered steel bodies.
In the main, Welford 3X/FDB twin-ram underbody lifting gear is employed, but some of the older vehicles are fitted with Edbro front-of-body twin rams. Body capacities vary from 10 cu. yd. to 15 cu. yd., according to chassis type.
The Lifting Gear
'In Mr. Brown's view the job of the lifting gear should be limited to tipping the body and should not include stabilization of the load. He regards body strength as the most important stability factor, because it affords the most reliable means Of ensuring a straight lift when the body is loaded or the chassis of the vehicle is standing on uneven ground. Chassis stiffness is also considered essential, but not of greater importance than body strength.
Whilst it is recognized that the differential effect produced by the uneven loading of conventional twin-ram systems represents a special problem, a stiff body is regarded as essential to all types of system if the vehicle is employed for arduous tipping. work.. Because they do not materially. add to the torsional stiffness of the body, conventional types of stabilizer, are tick regarded as a satisfactory solution to the hazards associated with the use of `A lightweight body.
Details of the bodies as supplied by the Welford concern to the Brown company, include a robust sub-structure, formed of rolled channel-section longitudinals of *-in. material having a depth of 8 in., which are cross-braced by pressed-steel members of 13u-in. gauge. These are welded to full-length pressed-steel sills of the same gauge. Floor and sides are of fin. plate, and the sides are stiffened by
nine pressed-steel channel-sectioned pillars. .An important feature of the structure with regard to torsional stiffness is the use of box-type rail members, welded to the upper ends of the pillars and to the side plates. These comprise two inward-facing rolled-steel sections of fin. material, which are welded together to form an 8-in. box. They also serve as a protective rail against the dragline bucket chaini The taper of the bodies from the rear to the front is 6 in.
All-welded bodies are greatly preferred to other types on the score that bolts or rivets eventually work loose. It is significant that many of the existing. steel bodies have survived two chassis replacements. A number of the vehicles is equipped with a warning device which gives visual indication ol body lift from the normal travelling
position.
Single wheels are fitted to the rear bogies, 14.00-20 covers being used in place of the twinned 9.00-20 standard type. To provide a uniform chassis height, front wheels are fitted and have 40 x 8 covers. Employing the bigger tyres has a number of
advantages including an increase in
ground clearance by 4 in. and a reduction in the amount of mud carried by the tyres when the vehicle leaves a site in wet weather to travel on the public highway, in which condition mud is normally dropped.
This is important in view of the strict requirements of local councils regarding the avoidance of mud on road surfaces. The traction provided by the driving wheels is increased by the use of the larger covers, whilst the average wear rate of the tyres is unchanged.
A double-drive, fully articulated bogie without a third differential is employed in the interests of good traction in difficult conditions.
The extremely severe site conditions under which the vehicles operate are shown by the estimate that a mileage of 5,000 is equivalent to running 50,000 miles on normal roads with regard to the wear and tear of the engine and chassis gear. Because of the very fine particle sice of the fly ash when it is dry it is impossible to prevent its ingress into the engine cylinders. No type of air fitter is available which is capable of removing ash from the intake air for sufficiently long working period to justify its use.
The ash is also extremely abrasive, and to reduce engine
Wear to a minimum the lubricating oil is renewed at weekly intervals.