Distribution , and transport
Page 82
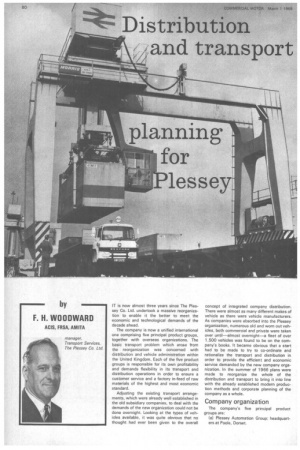
Page 83
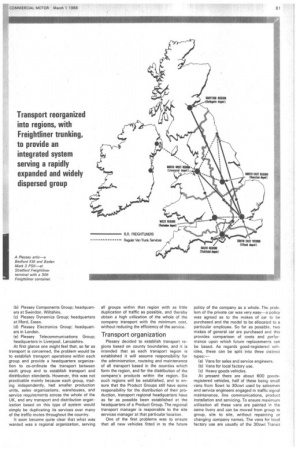
Page 84
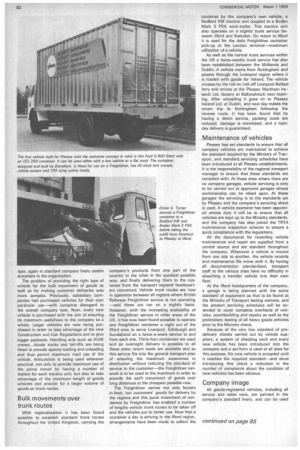
Page 87
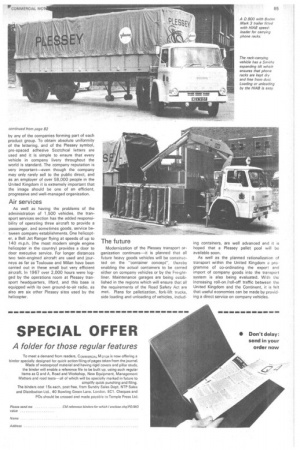
If you've noticed an error in this article please click here to report it so we can fix it.
by F. H. WOODWARD
ACIS, FRSA, AM ITA
IT is now almost three years since The Plessey Co. Ltd. undertook a massive reorganization to enable it the better to meet the economic and technological demands of the decade ahead.
The company is now a unified international one comprising five principal product groups, together with overseas organizations. The basic transport problem which arose from the reorganization was concerned with distribution and vehicle administration within the United Kingdom. Each of the five product groups is responsible for its own profitability and demands flexibility in its transport and distribution operations in order to ensure a customer service and a factory in-feed of raw materials of the highest and most economic standard.
Adjusting the existing transport arrangements, which were already well established in the old subsidiary companies, to deal with the demands of the new organization could not be done overnight. Looking at the types of vehicles available, it was quite obvious that no thought had ever been given to the overall concept of integrated company distribution. There were almost as many different makes of vehicle as there were vehicle manufacturers. As companies were absorbed into the Plessey organization, numerous old and worn out vehicles, both commercial and private were taken over until—almost overnight—a fleet of over 1,500 vehicles was found to be on the company's books. It became obvious that a start had to be made to try to co-ordinate and rationalize the transport and distribution in order to provide the efficient and economic service demanded by the new company organization. In the summer of 1966 plans were made to reorganize the whole of the distribution and transport to bring it into line with the already established modern production methods and corporate planning of the company as a whole.
Company organization
The company's five principal product groups are: Ca) Plessey Automation Group: headquarters at Poole, Dorset. {b) Plessey Components Group; headquarters at Swindon, Wiltshire.
(c) Plessey Dynamics Group; headquarters at Ilford, Essex.
(d) Plessey Electronics Group; headquarters in London.
(e) Plessey Telecommunications Group; headquarters in Liverpool, Lancashire.
At first glance one might feel that, so far as transport is concerned, the problem would be to establish transport operations within each group and provide a headquarters organization to co-ordinate the transport between each group and to establish transport and distribution standards. However, this was not practicable mainly because each group, trading independently, had smaller production units, sales organizations, warehouses, and service requirements across the whole of the UK, and any transport and distribution organization based on this type of system would simply be duplicating its services over many of the traffic routes throughout the country.
It soon became quite clear that what was wanted was a regional organization, serving all groups within that region with as little duplication of traffic as possible, and thereby obtain a high utilization of the whole of the company transport with the minimum cast, without reducing the efficiency of the service.
Transport organization
Plessey decided to establish transport regions based on county boundaries, and it is intended that as each transport region is established it will assume responsibility for the administration, routeing and maintenance of all transport based in the counties which form the region, and for the distribution of the company's products within the region. Six such regions will be established, and to ensure that the Product Groups still have some responsibility for the distribution of their production, transport regional headquarters have as far as possible been established at the headquarters of a Product Group. The regional transport manager is responsible to the site services manager at that particular location.
One of the first problems was to ensure that all new vehicles fitted in to the future
policy of the company as a whole. The problem of the private car was very easy—a policy was agreed as to the makes of car to he purchased and the model to be allocated to a particular employee. So far as possible, two makes of general car are purchased and this provides comparison of costs and performance upon which future replacements can be based. As regards good-registered vehicles, these can be split into three distinct types:
la) Vans for sales and service engineers.
(13) Vans for local factory use.
(c) Heavy goods vehicles.
At present there are about 600 goodsregistered vehicles, half of these being small vans from 5cwt to 30cwt used by salesmen and service engineers engaged in traffic signal maintenance, line communications, product installation and servicing. To ensure maximum utilization all these vans are painted in the same livery and can be moved from group to group, site to site, without repainting or changing company names. The vans for local factory use are usually of the 30cwt Transit type, again in standard company livery usable anywhere in the organization.
The problem of providing the right type of vehicle for the bulk movement of goods as well as for making customer deliveries was more complex. Previously, subsidiary companies had purchased vehicles for their own particular use—with complete disregard to the overall company task. Now, every new vehicle is purchased with the aim of ensuring its maximum usefulness to the company as a whole. Larger vehicles are now being purchased in order to take advantage of the new Construction and Use Regulations and to give bigger payloads. Handling aids such as HIAB cranes, Joloda tracks and tail-lifts are being fitted to provide speedy loading and unloading and thus permit maximum road use of the vehicle. Articulation is being used wherever practical, not only to provide maximum use of the prime mover by having a number of trailers for each tractive unit, but also to take advantage of the maximum length of goods vehicles and provide for a larger volume of goods on trunk routes.
Bulk movements over trunk routes
With regionalization it has been found possible to establish standard trunk routes throughout the United Kingdom, carrying the company's products from one part of the country to the other in the quickest possible way, and finally delivering them to the customer from the transport regional headquarters concerned. Vehicle trunk routes are now in operation between all regions where British Railways Freightliner service is not operating —and these are run on a nightly basis. However, with the increasing availability of the Freightliner service in other areas of the UK, it has now been found possible to operate one Freightliner container a night out of the Ilford area to serve Liverpool, Edinburgh and Sunderland on a twice-a-week service to and from each site. Thirty-foot containers are used and an overnight delivery is possible to all these sites; return loads are available and so this service fits into the general transport plan of ensuring the maximum economies in distribution without reducing the standard of service to the customer—the Freightliner network is to be used to the maximum in order to provide the swift movement of goods over long distances at the cheapest possible rate.
The Freightliner carries not only factory in-feed, but customers' goods for delivery by the regions and this quick movement of containers by Freightliner has enabled a number of lengthy vehicle trunk routes to be taken off and the vehicles put to better use. Now that a container a day is arriving in the Ilford region, arrangements have been made to collect the container by the company's own vehicle, a Bedford KM tractive unit coupled to a Baden Mark 3 PSK semi-trailer. This tractive unit also operates on a nightly trunk service between Ilford and Swindon. On return to Ilford it is used for the daily Freightliner container pick-up at the London terminal—maximum utilization of a vehicle.
As well as the normal trunk services within the UK a twice-weekly trunk service has also been established between the Midlands and Dublin. A vehicle starts from Nottingham and passes through the Liverpool region where it is loaded with goods for Ireland. The vehicle crosses by the roll-on /roll-off Liverpool-Belfast ferry and arrives at the Plessey (Northern Irelandi Ltd. factory at Ballynahinch next morning. After unloading it goes on to Plessey Ireland Ltd. at Dublin, and next day makes the return trip to Nottingham following the reverse route. It has been found that by having a direct service, packing costs are reduced, damage is minimized, and a nextday delivery is guaranteed.
Maintenance of vehicles
Plessey has set standards to ensure that all company vehicles are maintained to achieve the standard required by the Ministry of Transport, and standard. servicing schedules have been introduced at all Plessey establishments. It is the responsibility of the regional transport manager to ensure that these standards are complied with. At those sites where there are no company garages, vehicle servicing is only to be carried out at approved garages whose workmanship can be relied upon. At these garages the servicing is to the standards set by Plessey and the company's servicing sheet is used. A vehicle examiner has been appointed whose duty it will be to ensure that all vehicles are kept up to the Ministry standards, and the company has also joined the TRTA maintenance inspection scheme to ensure a quick compliance with the regulations.
All the documents for recording vehicle maintenance and repair are supplied from a central source and are standard throughout the company. Whenever a vehicle is moved from one site to another, the vehicle records and maintenance file move with it. By having all documentation standardized, transport staff at the various sites have no difficulty in absorbing a transfer vehicle into their own fleet.
At the Ilford headquarters of the company, a garage is being planned with the same standard of equipment as that to be found at the Ministry of Transport testing stations, and the present servicing schedules will be extended to cover complete overhauls of vehicles, coachbuilding and repairs as well as the preliminary testing of all heavy goods vehicles prior to the Ministry check.
Because of the very low standard of predelivery checks carried out by vehicle suppliers, a system of checking each and every new vehicle has been introduced into the company and a set form is used at all sites for this purpose. No new vehicle is accepted until it reaches the required standard—and since introducing this check a reduction in the number of complaints about the condition of new vehicles has been obvious.
Company image
All goods-registered vehicles, including all service and sales vans, are painted in the company's standard livery, and Can be used by any of the companies forming part of each product group. To obtain absolute uniformity of the lettering, and of the Plessey symbol, pre-spaced adhesive Scotchcal letters are used and it is simple to ensure that every vehicle in company livery throughout the world is standard. The company reputation is very important—even though the company may only rarely sell to the public direct and as an employer of over 58,000 people in the United Kingdom it is extremely important that the image should be one of an efficient, progressive and well-managed organization.
Air services
As well as having the problems of the administration of 1,500 vehicles, the transport services section has the added responsibility of operating three aircraft to provide a passenger, and sometimes goods, service between company establishments. One helicopter, a Bell Jet Ranger flying at speeds of up to 140 m.p.h. (the most modern single engine helicopter in the country) provides a door to door executive service. For longer distances two twin-engined aircraft are used and journeys as far as Toulouse and Milan have been carried out in these small but very efficient aircraft. In 1967 over 2,000 hours were logged by the operations room at Plessey transport headquarters, Ilford, and this base is equipped with its own ground-to-air radio, as also are six other Plessey sites used by the helicopter.
The future Modernization of the Plessey transport organization continues—it is planned that all future heavy goods vehicles will be constructed on the -container concept-, thereby enabling the actual containers to be carried either on company vehicles or by the Freightliner. Maintenance garages are being established in the regions which will ensure that all the requirements of the Road Safety Act are met. Plans for palletization, fork-lift trucks, side loading and unloading of vehicles, includ
ing containers, are well advanced and it is hoped that a Plessey pallet pool will be available soon.
As well as the planned rationalization of transport within the United Kingdom a pro gramme of co-ordinating the export and import of company goods into the transport system is also being evaluated, With the increasing roll-on /roll-off traffic between the United Kingdom and the Continent, it is felt that useful economies can be made by providing a direct service on company vehicles.