Sugar handling strides ahead
Page 47
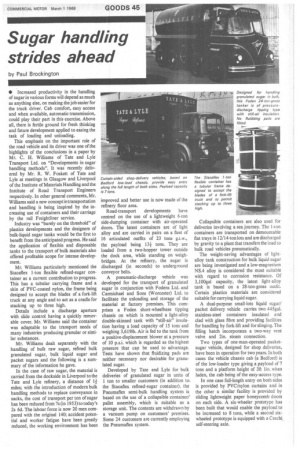
If you've noticed an error in this article please click here to report it so we can fix it.
by Paul Brockington
• Increased productivity in the handling of sugar in various forms will depend as much as anything else, on making the job easier for the truck driver. Cab comfort, easy access and when available, automatic transmission, could play their part in this exercise. Above all, there is fertile ground for fresh thinking and future development applied to easing the task of loading and unloading.
This emphasis on the important role of the road vehicle and its driver was one of the highlights of the conclusions in a paper by Mr. C. H. Williams of Tate and Lyle Transport Ltd. on "Developments in sugar handling methods". It was recently delivered by Mr. R. W. Foskett of Tate and Lyle at meetings in Glasgow and Liverpool of the Institute of Materials Handling and the Institute of Road Transport Engineers respectively. In other general comments, Mr. Williams said a new concept intransportation and handling is being inspired by the increasing use of containers and their carriage by the rail Freightliner service.
Industry was "barely on the threshold" of plastics developments and the designers of bulk-liquid sugar tanks would be the first to benefit from the anticipated progress. He said the application of flexible and disposable tanks to the transport of bulk materials also offered profitable scope for intense development.
Mr. Williams particularly mentioned the Stacaflex 1-ton flexible refined-sugar container as a current contribution to progress. This has a tubular carrying frame and a skin of PVC-coated nylon, the frame being designed to accept the blades of a fork-lift truck at any angle and to act as a cradle for stacking up to three high.
Details include a discharge aperture with slide control having a quickly removable cover. Mr. Williams said the container was adaptable to the transport needs of many industries producing granular or similar substances.
Mr. Williams dealt separately with the handling of bulk raw sugar, refined bulk granulated sugar, bulk liquid sugar and packet sugars and the following is a summary of the information he gave.
In the case of raw sugar, the material is carried from the dockside in Liverpool to the Tate and Lyle refinery, a distance of 1miles; with the introduction of modern bulk handling methods to replace conveyance in sacks, the cost of transport per ton of sugar has been reduced from 7s (in 1953) to today's 2s 6d. The labour force is now 20 men compared with the original 140; accident potential and worker fatigue have been greatly reduced, the working environment has been improved and better use is now made of the refinery floor area.
Road-transport developments have centred on the use of a lightweight 6-ton side-dumping container with air-operated doors. The latest containers are of light alloy and are carried in pairs on a fleet of 16 articulated outfits of 23 tons g.t,w., the payload being 13+ tons. They are loaded from a two-hopper tower outside the dock area, while standing on weighbridges. At the refinery, the sugar is discharged (in seconds) to underground conveyor belts.
A pneumatic-discharge vehicle was developed for the transport of granulated sugar in conjunction with Fodens Ltd. and Carmichael and Sons (Worcester) Ltd. to facilitate the unloading and storage of the material at factory premises. This comprises a Foden short-wheelbase tipping chassis on which is mounted a light-alloy double-skinned tank with "still-air" insulation having a load capacity of 15 tons and weighing 3,6191b. Air is fed to the tank from a positive-displacement blower at a pressure of 10 p.s.i. which is regarded as the highest pressure that can be used to advantage. Tests have shown that fluidizing pads are neither necessary nor desirable for granulated sugar.
Developed by Tate and Lyle for bulk deliveries of granulated sugar in units of 1 ton to smaller customers (in addition to, the Stacaflex refined-sugar container), the Pneumaflex semi-bulk handling system is based on the use of a collapsible container/pallet assembly, which is suitable as a storage unit. The contents are withdrawn by a vacuum pump on customers' premises. Some 24 customers are currently employing the Pneumaflex system.
Collapsible containers are also used for deliveries involving a sea journey. The 1-ton containers are transported on demountable flat trays in 12/14-ton lots and are discharged by gravity to a plant that transfers the load to bulk road vehicles pneumatically.
The weight-saving advantages of lightalloy tank construction for bulk liquid sugar are being investigated and a low-magnesium NS.4 alloy is considered the most suitable with regard to corrosion resistance. Of 3,100gal capacity, the latest light-alloy tank is based on a 28-ton-gross outfit. Certain plastics materials are considered suitable for carrying liquid sugar.
A dual-purpose small-lots liquid sugar/ packet delivery vehicle carries two 445ga1. stainless-steel containers insulated and clad with glass fibre and providing facilities for handling by fork-lift and for slinging. The filling hatch incorporates a two-way vent valve and 2in. steam connection.
Two types of one-man-operated packetsugar vehicle, designed for shop deliveries, have been in operation for two years. In both cases the vehicle chassis cab (a Bedford) is of the low-loader type giving a payload of 7 tons and a platform height of 3ft lin. when laden, the cab being of the easy-access type.
In one case full-length entry on both sides is provided by PVC/nylon curtains and in the other a similar facility is provided by sliding lightweight paper honeycomb doors on each side. A six-wheeler prototype has been built that would enable the payload to be increased to 8 tons, while a second sixwheeled prototype is equipped with a Ceschi. self-steering axle.