Simple to• Build and Maintain
Page 34
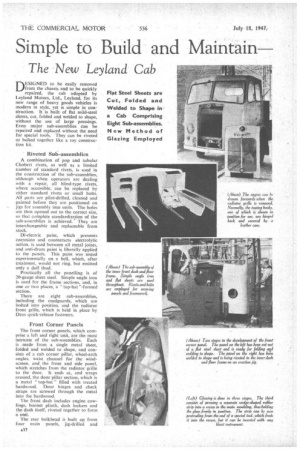
Page 35
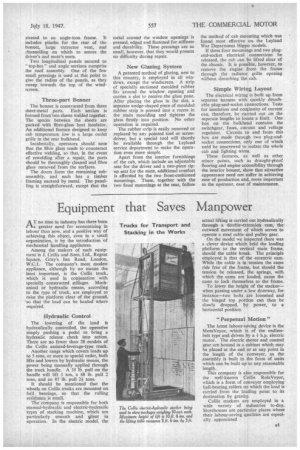
If you've noticed an error in this article please click here to report it so we can fix it.
The New Leyland Cab DESIGNED to be easily removed from the chassis and to be quickly repaired, the cab adopted by Leyland Motors, Ltd., Leyland, for its new range of heavy goods vehicles is modern in style, yet is simple in construction. It is built of flat mild-steel sheets, cut, folded and welded to shape, without the use of large pressings. Even major sub-assemblies can be repaired and replaced without the need for special tools. They can be riveted or bolted together like a toy construction kit.
Riveted Sub-assemblies
A combination of pop and tubular Chobert rivets, as well as a limited number of standard rivets, is used in the construction of the sub-assemblies, although when operators are dealing with a repair, all blind-type rivets, where accessible, can be replaced by either standard rivets or small bolts. All parts are pilot-drilled, cleaned and painted before they are positioned on jigs for assembly into units. The holes are then opened out to the correct size, so that complete standardization of the sub-assemblies is achieved.' They are interchangeable and replaceable from stock.
Di-electric paint, which prevents corrosion and counteracts electrolytic action, is used between all metal joints, and anti-drum paint is liberally applied to the panels. This paint was tested experimentally on a bell, which, after treatment, would not ring, but emitted only a dull thud.
Practically all the panelling is of 20-gauge sheet steel. Simple angle iron is used for the frame sections, and, in one or two places, a "top-hat "-formed section.
There are eight sub-assemblies, including the mudguards, which are bolted into position, and the radiator front grille, which is held in place by Dzus quick-release fasteners.
Front Corner Panels
The front corner panels, which comprise a left and right unit, are the most intricate of the sub-assemblies. Each is made from a single metal sheet, folded and welded to shape, and consists of a cab corner pillar, wheel-arch angles, waist channel for the windscreen. and, the front and side panel, which stretches from the radiator grille to the door. It ends at, and wraps around, the door pillar section, which is a metal " top-hat " filled with treated hardwood. Door hinges and check straps are screwed through the metal into the hardwood.
The front dash includes engine cowlings, bonnet plinth. dash lockers and the dash itself, riveted together to form a unit.
The rear bulkhead is built up from four main panels, jig-drilled and riveted to an angle-iron frame. It includes plinths for the rear of the bonnet, large extractor vent, and channelling on which to secure the driver's and mate's seats.
Two longitudinal panels secured to top-hat" and angle sections comprise the roof assembly. One of the few small pressings is used at this point to give the radius of the panels, as they sweep towards the top of the windscreen.
Three-part Bonnet
The bonnet is constructed from three sheet-metal parts. Each section is formed from two sheets welded together. The spaces between the sheets are packed with fibre-glass heat insulator. An additional feature designed to keep cab temperature low is a large outlet grille in the rear bulkhead.
Incidentally, operators should note that the fibre glass tends to counteract effective welding, so that, in the event of rewelding after a repair, the parts should be thoroughly cleaned and fibre glass removed from the surfaces.
The doors form the remaining subassembly, and each has a timber framing encased by metal. The panelling is straightforward, except that the metal around the window openings is pressed, edged and flattened for stiffness and durability. These pressings are so small, however, that they would present no difficulty during repair.
New Glazing System
A patented method of glazing, new to this country, is employed in all windows, except the windscreen. A strip of specially sectioned moulded rubber fit3 around the window opening and carries a slot to receive the glass pane. After placing the glass in the slot, a separate wedge-shaped piece of moulded rubber strip is pressed into a recess in the main moulding and tightens the glass firmly into position. No other operation is required.
The rubber strip is easily removed or replaced by any pointed tool or screwdriver, but a special tool will shortly be available through the Leyland service department to make the operation even more simple.
Apart from the interior furnishings of the cab, which include an adjustable seat for the driver and a two-piece tipup seat for the mate, additional comfort is afforded by the two front-cushioned mountings. These, together with the two fixed mountings at the rear, follow the method of cab mounting which was found most effective on the Leyland War Department Hippo models.
If these four mountings and two plugand-socket electrical connections be released, the cab can be lifted clear of the chassis. It is possible, however, to remove the engine from the frame through the radiator grille opening without disturbing the cab.
Simple Wiring Layout
The electrical wiring is built up from separate harness with quickly detachable plug-and-socket connections. Tests for insulation and continuity of current can, therefore, be carried out on the separate lengths to locate a fault. One box on the bulkhead contains the switchgear, fuses, cut-out and voltage regulator. Circuits to and from this box are made through two plug-andsocket connections, only one of which need be unscrewed to isolate the whole cab and lighting wires.
These features, as well as other minor points, such as draught-piroof flooring and engine accessibility through the interior bonnet, show that attractive appearance need not suffer in achieving ease of production and, more important to the operator. ease of maintenance.