• Look at the body first, say the men of Windfoil
Page 29
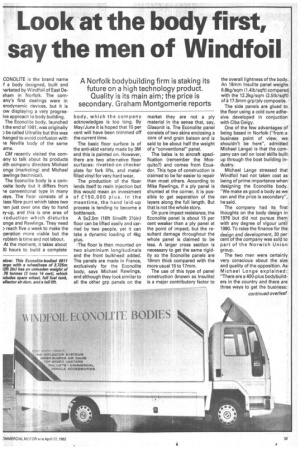
Page 30
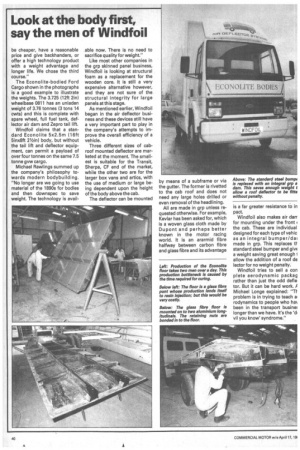
If you've noticed an error in this article please click here to report it so we can fix it.
A Norfolk bodybuilding firm is staking its future on a high technology product. Quality is its main aim; the price is secondary. Graham Montgomerie reports
.CONOLITE is the brand name I a body designed, built and narketed by Windfoil of East Desham in Norfolk. The corniany's first dealings were in erodynamic devices, but it is low displaying a very progresive approach to body building. The Econolite body, launched t the end of 1981, was originally D be called Ultralite but this was hanged to avoid confusion with le Neville body of the same ame.
CM recently visited the corn'any to talk about its products with company directors Michael onge (marketing) and Michael lawlings (technical).
The Econolite body is a corniosite body but it differs from le conventional type in many ways. The floor consists of a 'lass fibre punt which takes two nen just over one day to hand ly-up, and this is one area of iroduction which disturbs .onge and Rawlings. They need a reach five a week to make the iperation more viable but the foblem is time and not labour. At the moment, it takes about )0 hours to build a complete body, which the company acknowledges is too long. By May/June it is hoped that 10 per cent will have been trimmed off the current time.
The basic floor surface is of the anti-skid variety made by 3M and this is painted on. However, there are two alternative floor surfaces: rivetted-on checker plate for fork lifts, and metalfilled vinyl for very hard wear.
The production of the floor lends itself to resin injection but this would mean an investment of E1 5 0,0 00 plus. In the meantime, the hand laid-up process is tending to become a bottleneck.
A 5x2.5m (16ft 5inx8ft 21/21n) floor can be lifted easily and carried by two people, yet it can take a dynamic loading of 4kg plus.
/The floor is then mounted on two aluminium longitudinals and the front bulkhead added. The panels are made in France, exclusively for the Econolite body, says Michael Rawlings, and although they look similar to all the other grp panels on the market they are not a ply material in the sense that, say, Glasonit is. The Econolite panel consists of two skins enclosing a core of end grain balson and is said to be about half the weight of a "conventional" panel.
The balsa is to aircraft specification (remember the Mosquito?) and comes from Ecuador. This type of construction is claimed to be far easier to repair than most others. According to Mike Rawlings, if a ply panel is shunted at the corner, it is possible to get separation of the layers along the full length. But that is not the whole story.
On pure impact resistance, the Econolite panel is about 15 per cent weaker than a ply panel at the point of impact, but the resultant damage throughout the whole panel is claimed to be less. A larger cross section is necessary to get the same rigidity so the Econolite panels are 18mm thick compared with the more usual 15 to 17mm.
The use of this type of panel construction (known as lnsulite) is a major contributory factor to the overall lightness of the body. An 18mm Insulite panel weighs 6.8kg/sqm (1.4Ib/sqft) compared with the 12.2kg/sqm (2.5Ib/sqft) of 17.5mm grp/ply composite.
The side panels are glued to the floor using a cold cure adhesive developed in conjuction with Ciba Geigy.
One of the few advantages of being based in Norfolk ("from a business point of view, we shouldn't be here", admitted Michael Lange) is that the com pany can call on local skills built up through the boat building industry.
Michael Lange stressed that Windfoil had not taken cost as being of prime importance when• designing the Econolite body. "We make as good a body as we can and the price is secondary", he said.
The company had its first thoughts on the body design in 1976 but did not pursue them with any degree of vigour until 1980. To raise the finance for the design and development, 30 per cent of the company was sold to part of the Norwich Union group.
The two men were certainly very conscious about the size and quality of the opposition. As Michael Lange explained: "There are a 400-plus bodybuild ers in the country and there are ,three ways to get the business: be cheaper, have a reasonable price and give backhanders, or offer a high technology product with a weight advantage and longer life. We chose the third course."
The Econolite-bodied Ford Cargo shown in the photographs is a good example to illustrate the weights. The 3.725 (12ft 2in) wheelbase 0811 has an unladen weight of 3.76 tonnes (3 tons 14 cwts) and this is complete with spare wheel, full fuel tank, deflector air dam and Zepro tail lift Windfoil claims that a standard Econolite 5x2.5m (16ft 5inx8ft 21/2in) body, but without the tail lift and deflector equipment, can permit a payload of over four tonnes on the same 7.5 tonne gvw cargo.
Michael Rawlings summed up the company's philosophy towards modern bodybuilding. "No longer are we going to use material of the 1890s for bodies and then downspec to save weight. The technology is avail
able now. There is no need to sacrifice quality for weight."
Like most other companies in the grp skinned panel business, Windfoil is looking at structural foam as a replacement for the wooden core. It is still a very expensive alternative however, and they are not sure of the structural integrity for large panels at this stage.
As mentioned earlier, Windfoil began in the air deflector business and these devices still have a very important part to play in the company's attempts to improve the overall efficiency of a vehicle.
Three different sizes of cabroof mounted deflector are marketed at the moment. The smallest is suitable for the Transit, Sherpa, CF end of the market, while the other two are for the larger box vans and artics, with the use of medium or large being dependent upon the height of the body above the cab.
The deflector can be mounted by means of a subframe or via the gutter. The former is rivetted to the cab roof and does not need any large holes drilled or even removal of the headlining, All are made in grp unless requested otherwise. For example, Kevlar has been asked for, which is a woven glass cloth made by Dupont and perhaps better known in the motor racing world. It is an ararmid fibre halfway between carbon fibre and glass fibre and its advantage is a far greater resistance to in pact.
Windfoil also makes air darr for mounting under the front the cab. These are individual designed for each type of vehic as an integral bumper/dal made in grp. This replaces standard steel bumper and givE a weight saving great enough allow the addition of a roof de lector for no weight penalty.
Windfall tries to sell a con pieta aerodynamic packag rather than just the odd defle tor. But it can be hard work. Michael Longe explained: "Ti problem is in trying to teach al rodynamics to people who haN, been in the transport busine: longer than we have. It's the 'di vil you know' syndrome."