Finding where the money goes
Page 33
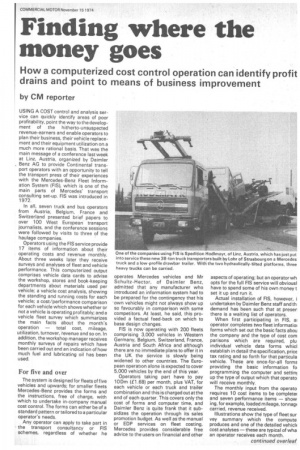
Page 34
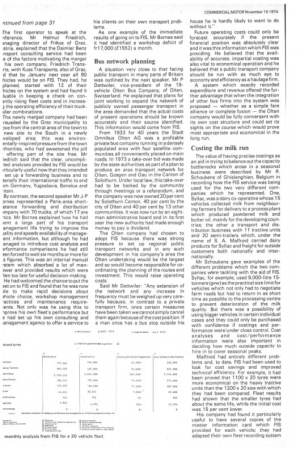
Page 35
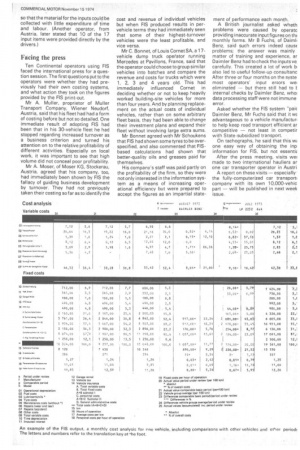
If you've noticed an error in this article please click here to report it so we can fix it.
How a computerized cost control operation can identify profit drains and point to means of business improvement
by CM reporter
USING A COST control and analysis service can quickly identify areas of poor profitability, point the way to the development of the hitherto-unsuspected revenue-earners and enable operators to plan their business, their vehicle replacement and their equipment utilization on a much more rational basis. That was the main message of a conference last week at Linz, Austria, organized by Daimler Benz AG to provide Continental transport operators with an opportunity to tell the transport press of their experiences with the Mercedes-Benz Fleet Information System (RS), which is one of the main parts of Mercedes transport consulting set-up. FIS was introduced in 1972.
In all, seven truck and bus operators from Austria, Belgium, France and Switzerland presented brief papers to over 100 West European transport journalists, and the conference sessions were followed by visits to three of the haulage companies.
Operators using the FIS service provide 17 items of information about their operating costs and revenue monthly. About three weeks later they receive surveys and analyses of fleet and vehicle performance. This computerized output comprises vehicle data cards to advise the workshop, stores and book-keeping departments about materials used per vehicle; a vehicle cost analysis, showing the standing and running costs for each vehicle; a cost/performance comparison for each vehicle which shows whether or not a vehicle is operating profitably; and a vehicle fleet survey which summarizes the main facts about the month's operation — total cost, mileage, utilization, turnover, revenue and so on. In addition, the workshop manager receives monthly surveys of repairs which have been carried out and an indication of how much fuel and lubricating oil has been used.
For five and over
The system is designed for fleets of five vehicles and upwards: for smaller fleets Mercedes-Benz provides the forms and the instructions, free of charge, with which to undertake in-company manual cost control. The forms can either be of a standard pattern or tailored to a particular operator's needs.
Any operator can apply to take part in • the transport consultancy or FIS schemes, regardless of whether he
operates Mercedes vehicles and Mr Schultz-Hector, of Daimler Benz, admitted that any manufacturer who introduced an information system had to be prepared for the contingency that his -own vehicles might not always show up so favourably in comparison with some competitors. At least, he said, this provided a factual feed-back on which to base design changes.
FIS is now operating with 200 fleets comprising 3,000 vehicles in Western Germany, Belgium, Switzerland, France, Austria and South Africa and although there are no immediate plans to offer it in the UK the service is slowly being widened to other countries. The European operation alone is expected to cover 5,000 vehicles by the end of this year.
Operators taking part have to pay 10 Dm (E1.68) per month, plus VAT, for each vehicle or each truck and trailer combination and this is charged out at the end of each quarter. This covers only the cost of forms and computer time, and Daimler Benz is quite frank that it subsidizes the operation through its sales promotion budget. As well as the manual or EDP services on fleet costing, Mercedes provides considerable free advice to the users on financial and other aspects of operating; but an operator wh opts for the full AS service will obviousl have to spend some of his own money t set it up and run it.
Actual installation of FIS, however, i undertaken by Daimler Benz staff and th demand has been such that at preser there is a waiting list of operators.
When first participating in FIS, al operator completes two fleet informatioi forms which set out the basic facts abou the company and the type of cost corn parisons which are required, plu individual vehicle data forms whicl establish in detail the specification, price tax rating and so forth for that particula vehicle. These are once-for-all forms providing the basic information fo programming the computer and settini up the type of output which that operato will receive monthly.
The monthly input from the operato requires 10 cost items to be complete( and seven performance items — show ing, for example, loaded mileage, tonnagE carried, revenue received.
Illustrations show the type of fleet sur vey summary which the compute produces and one of the detailed vehick cost analyses — these are typical of wha an operator receives each month.
continued overleaf ihe first operator to speak at the nference, Mr Helmut Friedrich, tnaging director of Frikus of Graz, stria, explained that the Daimler Benz insport consulting service had been e of the factors motivating the merger his own company, Friedrich Transrts, with Kuss Transports, also of Graz, d that by January next year all 90 hides would be on FIS. They had, he plained, started with 12 of their hicles op the system and had found it luable in keeping a check on con3ntly rising fleet costs and in increas] the operating efficiency of their truckiiler combinations.
The newly merged company had been rsuaded by the Graz municipality to 3ve from the central area of the town to new site to the South in a newly !veloped area; this was environentally-inspired pressure from the town thorities, who had sweetened the pill offering part of the site free. Mr iedrich said that the clear, uncomplited analyses provided by FIS would be irticularly useful now that they intended set up a forwarding business and to tensify their international traffic to and lm Germany, Yugoslavia, Benelux and By contrast, the second speaker MrJ-P )rnes represented a Paris-area shortstance forwarding and distributionimpany with 70 trucks, of which 17 are 'tics. Mr Barnes explained how he had ient a large part of his transport anagement life trying to improve the iality and speedy availability of manageent information, but although he had anaged to introduce cost analysis and ?rformance comparisons he had still )en forced to wait six months or more for s figures. This was an internal manual stem which absorbed a lot of man)wer and provided results which were ten too late for useful decision-making. He had welcomed the chance to put the ?,et on to FIS and found that he was now )le to make rapid decisions about .hicle choice, workshop management .actices and maintenance require'ems. Not only was he using this to iprove his own fleet's performance but
had set up his own consulting and ianagement agency to offer a service to his clients on their own transport problems.
As one example of the immediate results of going on to FIS, Mr Bornes said it had identified a workshop deficit of fr17,000 (f 1552) a month.
Bus network planning
A situation very close to that facing public transport in many parts of Britain was outlined by the next speaker, Mr P Dettvviler, vice-president of the 19vehicle Olten Bus Company, of Often, Switzerland, He explained that plans for joint working to expand the network of publicly owned passenger transport in the area demanded that the actual costs of present operations should be known accurately and their source identified. This information would come from FIS.
From 1933 for 40 years the Stadt Omnibus Olten AG was a profitable private bus company running in a densely populated area with four satellite communities all conveniently placed on main roads. In 1973 a take-over bid was made by the state authorities as part of a plan to produce an area transport network for Olten, Gosgen and Gau in the Canton of Solothurn. Under local law, this take-over had to be backed by the community through meetings or a referendum, and the company was now owned 20 per cent by Solothurn Canton, 40 per cent by the city of Olten and 40 per cent by 13 other communities. It was now run by an eightman administrative board and in its first year the new authority had made enough money to pay a dividend.
The Olten company had chosen to adopt HS because there was strong pressure to set up regional public transport networks and in any such development in his company's area the Often undertaking would be the largest and so would become responsible for coordinating the planning of the routes and investment. This would raise operating costs.
Said Mr Dettwiler "Any extension of the network and any increase in frequency must be weighed up very carefully because, in contrast to a private transport firm, once certain measures have been taken we cannot simply cancel them again because of the cost position. If a man once has a bus stop outside his
house he is hardly likely to want to do without it.
Future operating costs could only be forecast accurately if the present financial position was absolutely clear and it wasthis information which FIS was providing. He believed that the availability of accurate, impartial costing was also vital to economical operation and he believed that a public transport company should be run with as much eye to economy and efficiency as a haulagefirm.
A system which exactly recorded expenditure and revenue offered the further advantage that when the integration of other bus firms into the system was proposed — whether as a simple fare alliance or complete fusion — the Olten company would be fully conversant with its own cost structure and could set its sights on the course which would prove most appropriate and economical in the long run.
Costing the milk run
The value of having precise costings as an aid in trying to balance out the capacity bottlenecks which arose in a seasonal business were described by Mr R. Schoukens of Ghislenghien, Belgium in recording how the FIS service was being used for the two very different companies which he represented. One, Syllac, was a dairy co-operative whose 15 vehicles collected milk from neighbouring farmers far delivery to a process plant which produced powdered milk and butter oil, mainly for the developing countries; the other a transport and distribution business with 11 tractive units and 20 semi-trailers which, under the name of S. A. Malfroid carried dairy products for Syllac and freight for outside customers both nationally and internationally.
Mr Schoukens gave examples of the different problems which the two companies were tackling with the aid of FIS. Syllac, for example, used 9,000-litre 15tonners (gvw)as the practical size limit for vehicles which not only had to negotiate farm roads but had to return in as short time as possible to the processing centre to prevent deterioration of the milk quality. But there was a possibility of using bigger vehicles in certain individual cases and they could only be purchased with confidence if costings and performance were`under close control. Cost analyses and cost/performance information were also important in deciding how much outside capacity to hire in to cover seasonal peaks.
Malfroid had entirely different problems and, to date, RS had been used to look for cost savings and improved technical efficiency. For example, it had been proved that 1100 x 20 tyres were more economical on the heavy tractive units than the 1200 x 20 size with which they had been compared. Fleet results had shown that the smaller tyres had about the same life, while the initial cost was 1 5 per cent lower.
His company had found it particularly useful to have several copies of the master information card which FIS provided for each vehicle; they had adapted their own fleet recording system so that the material for the inputs could be collected with little expenditure of time and labour, (Another operator, from Austria, later stated that 10 of the 17 input items were provided directly by the drivers.)
Faring the press
Ten Continental operators using FIS faced the international press for a question session. The first questions put to the operators were whether they had previously had their own costing systems, and what action they took on the figures provided by the FIS print-out.
Mr A. Muller, proprietor of Muller Transport Company, Wiener Nem:fort Austria, said that his fleet had had a form of costing before but not so detailed. One immediate result of adopting FIS had been that in his 30-vehicle fleet he had stopped regarding increased turnover as a business criterion and turned his attention on to the relative profitability of different activities. Especially on local work, it was important to see that high volume did not conceal poor profitability.
Mr A. Moser, of Moser KG, Stockerau, Austria, agreed that his company, too, had immediately been shown by FIS the fallacy of guiding business development by turnover. They had not previously taken their costing so far as to identify the cost and revenue of individual vehicles but when FIS produced results in pervehicle terms they had immediately seen that some of their highest-turnover vehicles were the least profitable, and vice versa.
Mr C. Bonnet, of Louis Cornet SA, a 17vehicle dump truck operator running Mercedes at Pavilions, France, said that the operator could choose to group similar vehicles into batches and compare the revenue and costs for trucks which were 1, 2, 3 and 4 years old. This had immediately influenced Cornet in deciding whether or not to keep heavily worked building-site vehicles for more than four years. And by planning replacement on the actual costs of individual vehicles, rather than on some arbitrary fleet basis, they had been able to change their investment plans and expand their fleet without involving large extra sums.
Mr Bonnet agreed with Mr Schoukens that FIS had shown some tyres to be overspecified, and also commented that FISbased calculations had shown that better-quality oils and greases paid for themselves.
His company's staff was paid partly on the profitability of the firm, so they were not only interested in the information system as a means of increasing operational efficiency but were prepared to accept the figures as an impartial state
ment of performance each month, A British journalist asked wheth problems were caused by operate providing inaccurate input figures on thi monthly forms. Mr B Fuchs, of Daimli Benz, said such errors indeed causE problems; the answer was mainly matter of training and experience, ar Daimler Benz had to check the inputs ve carefully. This created a lot of work b also led to useful follow-up consultanc After three or four months on the syste most operators input errors wei eliminated but there still had to t internal checks by Daimler Benz, who data processing staff were not immune error.
Asked whether the FIS system "pair Daimler Benz, Mr Fuchs said that it wk advantageous to a vehicle manufactur. to help keep road transport efficient ar competitive not least in competir with State-subsidized transport.
On tachographs, he said that this wi one easy way of obtaining the inp information for FIS, but not essentik After the press meeting, visits wei made to two international hauliers ar one car transporter operator in Austri A report on these visits especially • the fully-computerized car transport, company with its own 10,000-vehic part will be published in next week issue.