Centralized Lubrication.
Page 52
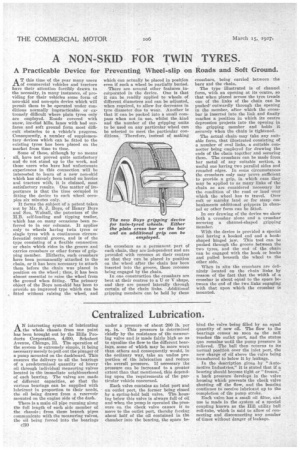
If you've noticed an error in this article please click here to report it so we can fix it.
AN interesting system of lubricating the whole chassis from one point has been brought out by the Hills Products Corporation, 4,600, Schubert Avenue, Chicago, Ill. The operation of the system is extremely simple, it being necessary merely to pull out the plunger of a pump mounted on the dashboard. This ensures the delivery to all the beatings of a predetermined quantity of heavy oil through individual measuring valves located in the immediate neighbourhood of each bearing. The valves are made of different capacities, so that the various bearings can be supplied with lubricant in proportion to their needs, the oil being drawn from a reservoir mounted on the engine side of the dash.
There is a main oil pipe running along the full length of each side member of the chassis; from these branch pipes communicate with the measuring valves, the oil being forced into the hearings C30 under a pressure of about 200 lb. per sq. in. This pressure is determined chiefly by the resistance of the measuring valve and is made fairly high so as to equalize the flow to the different bearings, some of which may be more worn than others and consequently would, in the ordinary way, take an undue proportion of the lubrication and reduce the overall pressure. If necessary the pressure can be increased to a greater extent than that mentioned, this depending upon the requirements of the particular vehicle concerned.
Each valve contains an inlet port and an outlet port, the former being closed by a spring-held ball valve. The housing below this valve is always full of oil and when the pump is operated the pressure on the check valve causes it to move to the outlet port, thereby forcing about half of the oil contained in the chamber into the bearing, the space be
hind the valve being filled by an equal quantity of new oil. The flow to the bearings ceases so soon as the Pall reaches the outlet port, and the status quo remains until the pump pressure is relieved. The ball then returns to its normal position over the inlet port, the new charge of oil above the valve being transferred to below it by leakage.
In the description given by "Automotive Industries," it is stated that if a bearing should become tight or "frozen," a back pressure develops in the valve housing which prevents the cheek valve shutting off the flow, and the bearing continues to receive lubricant up to the completion of the pump stroke.
Each valve has a small oil filter, and use is made in the system of a special coupling known as the Hill utility ball roll-tube, which is said to allow of connecting and disconnecting any number of times without danger of leakage.