Gating the Best Out of
Page 29
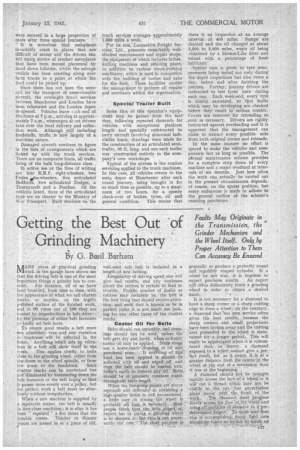
Page 30
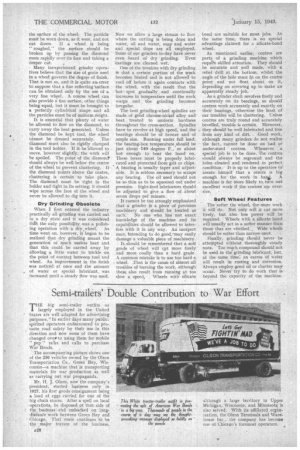
If you've noticed an error in this article please click here to report it so we can fix it.
Grinding Machinery
By G. Basil Barham
Faults May Originate in the Transmission, the Grinder Mechanism and the Wheel Itself. Onlyby Proper Attention to Them Can Accuracy Be Ensured
years of • practical grinding LVlwork in-the garage have showia me that the driving belt is one of the most important things a grinder has to con sider. For instance, all of us have been-troubled, from time to time, with the appearance of what we call chatter marks, or mottles, on the highly polished surface of the finished work, and in 99 times out of 100 they are cauSed by imperfections in belt drive— by the presence of either belt fasteners cc badly set 'belt laces.
To ensure good results a belt must run absolutely true and any variation in thickness will be reflected in the finish. Anything 'which sets up vibration in a belt will show itself in the work. This applies chiefly to belts close to the grinding wheel, either from the drum to the wheel spindle, or from
the drum td the headstock. Such chatter marks can be minimized but not eliminated by hammering down the belt fasteners or the belt laqing so that it passes more evenly over a pulley, but for -perfect work a belt must be absolutely without irregularities.
When a new machine is supplied by a reputable maker, the belt is usually in first-class condition ; it is after it has been " repaired ", a few times that the trouble comes. Thicker or thinner peces are joined in or a piece of old, well-used soft belt is included in a length ;of new -belting.
Irregalarity of driving speed also will give bad results, and any weakness about the centres is certain to lead to trouble; Prohfic. souraes of faults as centres may certainly be, the belt is the first thing that should receive attention, and until that is known to be' in perfect order it is not much use looking for any other cause of the chatter marks.
Castor OH for Belts
Belts should run smootj-ily, and dressings should not be used, unless. the belt gets dry and harsh, when ordinary castor oil may be applied. Solite shops use a home-made dressing of Oil and powdered resin. If anYttiing ef this' kind has been applied it should 6e softened with oil and wiped. off, and then the belt should be coated with fuller's earth to remove any oil,Belts should be of precisely constant .width throughout their. length. When the foregoing points are above . reproach and difficulty in obtaining a high-quality finish is. still encountered, a little care in truing.the ,wheel is probably all 'that is necessary. _Most -* people think that the, only. ,object as expert has in truing a.. grinding wheel is to sharpen it, rest this is not fleece sarilv the case. ptl=pr4 .. _
generally to produce a perfectly round an regularly shaped cylinder. If a wheel be not true, it is hopeless to expect precision results. An expert will often deliberately blunt a grinding wheel in order to obtain a desired finish. s •
It is not necessary for a diamond to have a sharp corner or a sharp cutting edge to dress a wheel; on the contrary, a diamond that 'has seen service-often gives the best results, because the sharp corners and small projections have been broken away and the cutting , _ 'area presented to the wheel is maintained fcir a -longerperiod. This will easily be appreciated when it is remembered that, in -theory, a diamond exixised to a wheel .canaot give a perfeet result,, for, as it wears, it is at a greater distance from the cent:To of the wheel at the end of 'a revolution than it was at the beginning.'
A diamond, should not be brought rapidly across the face-of 'a wheel or it will cut .a thread. which May not be visible to the, eye; but nevertheless plays' havoc with". the finish . of the
work,. The .cliarnond must progress
sloWly across the f of the -wheel and bring all„partieles. of abrasive to q-pre . _ , . determined height. To make sure that this is accomplished., many light .cuts sh91.4d.be taken so as,.flort9,_!.fg.alcup
the surface of the wheel. The particle muSt be worn down, as it were, and not cut down. If a wheel is being " roughed," the surface should be broken up by passing the diamond more rapidly over its face and taking a deeper cut.
Many inexperienced grinder operas tives believe that the size of grain used in a wheel governs the degree of finish. That is not so, and it is quite ats error to suppose that a fine reflecting 'surface can be obtained only by the use of a very fine wheel, A coarse wheel can also provide a fine surface, other things being equal, but it must be brought to a perfectly cylindrical shape. and all the particles must he of uniform height.
It is essential that plenty of water be allowed to flow on the diamond, to carry away the beat generated. Unless the diamond be kept 'cool, the wheel cannot he dressed accurately, The diamond must also he rigidly clamped in the tool holder. if it be 'allowed to move, however slightly, the work will he spoiled. The point of the diamond' should always be well below the centre of the wheel to prevent chattering. If the diamond points above the centre,. chattering is certain to take place. The diamond must be tight in the holder and tight in its setting; it should wipe across the face Of the wheel and never be allowed to dig into it.
Dry Grinding Obsolete When I first eritered the industry practically all grinding was carried out in a dry state and it was considered tbh the only possibility was a polishing operation with a dry wheel. As time went on, however, it began to be realized that dry grinding meant the generation of 'much useless heat and that this could be carried away by allowing a little water to trickle 'on the point of contact between tool hnd wheel. An improv'ement in the finish was noticed at once and he amount of water or special lubricant. was increased until a steady flow was used. Now we allow a large stream to flow where the cutting is being done 'and water, oil and water, soap and water and special dope are all employed. Some of our grinders to-day have never even heard of dry grinding. Even castings are cleaned wet.
One of the troubles with dry grinding. is that a certain portion of the work becomes heated and is not allowed to cool off before it again contacts with the wheel, with the result that the hot • spot gradually and continually increases in temperature until the work warps and• the grinding becomes irregular.
The best grinding-wheel spindles are made of good chrome-nickel alloy and heat treated to uniform hardness throughout the cross-section. Spindles have to revolve at high speed, and the hearings should he of bronze and of ample size. Running under, full load, the bearing-box temperature.should be just about -140 degrees F., or about hot enough to bear the hand on. These boxes must be properly lubricated and protected from grit or chips. A bearing isusually taper and adjustable. It is seldom necessary to scrape any bearing. The oil used should not be so thin as to be squeezed out under pressure. Sight-feed lubricators sliould he adjusted to give a flow of about seven drops pet minute.
It cannot he too strongly emphasized that a grinder is a piece of precision machinery and should be treated as such. No one who has not exact knowledge of the machine and its capabilities should be allowed to inter., fere with it in any way. An inexpert man, Intending to do good,-may easily damage-a valuable piece of machinery. It.should be remembered that a soft grade of wheel will cut more freely and more coolly than a. hard grade. A common mistake is to use too hard a -wheel. .That is the cause of almost all troubles of burning the work, although these also result from running at too
slow a speed, Wheels with Silicate bond are suitable for most jobs. At the same time, there is no special advantage claimed for a silicate-bond wheel.
As mentioned earlier, centres are parts of a grinding machine which regale skilled attention. They should be accurate and well made, with a relief 'drill at the bottom, whilst the angle of the hole must fit on the centre point and not float about on it, depending on screwing up to make an apparently steady job.
As a grinder shaft revolves freely and accurately on its bearings, so should centres work accurately and exactly on their hearings, -otherwise the least of our troubles will be chattering. Unless centres are truly round and accurately bevelled, trouble is certain. Mbreover, • they should be well lubricated and free from any kind of dirt. . Good work, although many grinders do not realize
• the fact, cannot be done on bad_ ot under-sized centres. . Whenever a special job is to be done. The centres should always be reground and the boles cleaned and rendered in perfect condition.It is up to the operative to' assure himself that a centre is .big. enough for the work in liana. A machine is far More likely to, turn out excellent work if he centres are over
size. • Soft Wheel Features
, The softer the wheel, the more work it will do. Not only will it cut more freely, but also less power will be required. • Wheels with a silicate bond will usually act in a softer manner than those that are vitrified.'s Wide wheels
should be softer than narrow caws'. • Finally, grinding should never be attenripted without' thoroughly steady rests. Too much compound should not be used in the grinding lubricant, but, at the same time', an excess of water will result in rusting and corrosion. Always employ good oil or chatter may occur. Never try to do work that is beyond the capacity of the machine.