INTEGRAL CONSTRUCTION SAVES 1,000 lb.
Page 64
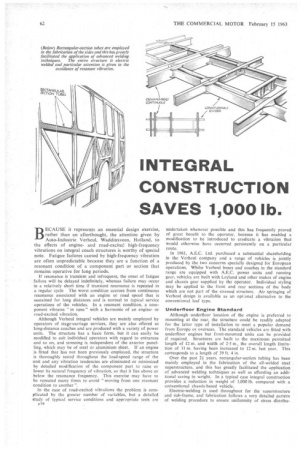
Page 65
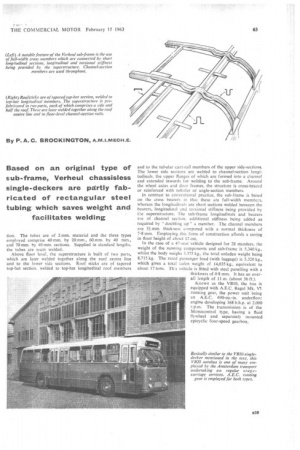
If you've noticed an error in this article please click here to report it so we can fix it.
BECAUSE it represents an essential design exercise, rather than an afterthought, the attention given by Auto-Industrie Verheul. Waddinxveert, Holland, to the effects of engineand road-excited high-frequency vibrations on integral coach structures is worthy of special note. Fatigue failures caused by high-frequency vibration are often unpredictable because they are a function of a resonant condition of a component part or section that
remains operative for long periods.
If resonance is transient and infrequent, the onset of fatigue failure will be delayed indefinitely, whereas failure may occur in a relatively short time if transient resonance is repeated in a regular cycle The worst condition accrues from continuous resonance associated with an engine or road speed that is sustained for long distances and is normal to typical service operations of the vehicles. In a resonant condition, a component vibrates "in tune" with a harmonic of an engineor road-excited vibration.
Although Verheul integral vehicles are mainly employed by operators of stage-carriage services, they are also offered as long-distance coaches and are produced with a variety of power units. The structure has a basic form, but it can easily be modified to suit individual operators with regard to entrances and so on, and stressing is independent of the exterior panelling, which may he of steel or aluminium sheet. If an engine is fitted that has not been previously employed, the structure is thoroughly tested throughout the load-speed range of the unit and any vibration tendencies are eliminated or minimized by detailed modification of the component part to raise or lower its natural frequency of vibration, so that it lies above or below the resonance frequency. This exercise may have to be repeated many times to avoid "moving from one resonant condition to another ".
In the case of road-excited vibrations the problem is complicated by the greater number of variables, but a detailed study of typical service conditions and appropriate tests are
F.1 R undertaken whenever possible and this has frequently proved of great benefit to the operator, because it has enabled a modification to be introduced to eradicate a vibration that would otherwise have occurred persistently on a particular route.
In 1961, A.E.C. Ltd. purchased a substantial shareholding in the Verheul company and a range of vehicles is jointly produced by the two concerns specially designed for European operations. Whilst Verheul buses and coaches in the standard range are equipped with A.E.C. power units and running gear, vehicles are built with Leyland and other makes of engine and chassis gear supplied by the operator.• Individual styling may be applied to the front and rear sections of the body which are not part of the stressed structure. Air springing of Verheul design is available as an opt:onal alternative to the conventional leaf type.
Underfloor Engine Standard
Although underfloor location of the engine is preferred to mounting at the roar, the structure could be readily adapted for the latter type of installation to meet a popular demand from Europe or overseas. The standard vehicles are fitted with underfloor engines but front-mounted units can be provided if required, Structures are built to the maximum permitted length of 12 m. and width of 2.5 m., the overall length limitation of 11 m. having been increased to 12 m. last year. This corresponds to a length of 39 ft. 4 in.
Over the past 2+ years, rectangular-section tubing has been mainly employed in the fabrication of the all-welded steel superstructure, and this has greatly facilitated the application of advanced welding techniques as well as affording an additional saving in weight. In a typical case integral construction provides a reduction in weight of 1,000 lb. compared with a conventional chassis-based vehicle.
Electric-welding is used throughout for the superstructure and Sub-frame, and fabrication follows a very detailed pattern of welding procedure to ensure uniformity of stress distribu
tion. The tubes are of 2mm. material and the three types employed comprise 40 mm. by 20 mm., 60 mm. by 40 mm., and 70mm. by 40 mm. sections. Supplied in standard lengths. the tubes are seam welded, Above floor level. the superstructure is built of two parts, which are later welded together along the roof centre line and to the lower side sections. Roof sticks are of tapered top-hat section. welded to top-hat longitudinal roof members and to the tubular cant-rail members of the upper side-sections. The lower side sections are welded to channel-section longitudinals, the upper flanges of which are formed into a channel and extended inwards for welding to the sub-frame. Around the wheel axles and door frames, the structure is cross-braced or reinforced with tubular or angle-section members.
In contrast to conventional practice, the sub-frame is based on the cross bearers in that these are full-width members, whereas the longitudinals are short sections welded between the hearers, longitudinal and torsional stiffness being provided by the superstructure. The sub-frame longitudinals and bearers are of channel section, additional stiffness being added as required by "doubling up a member. The channel members are 3+ mm. thickness compared with a normal thickness of 7-8 mm. Employing this form of construction affords a saving in floor height of about 12 cm.
In the case of a 47-seat vehicle designed for 28 standees, the weight of the running components and sUb-frame is 5,340 kg., whilst the body weighs 3.375 kg., the total unladen weight being 8,715 kg. The rated passenger load (with luggage) is 5,320 kg., which gives a total laden weight of 14,035 kg., equivalent to about 17 tons. Th:s vehicle is fitted with steel panelling with a thickness of 0-8 mm. It has an overall length of 11 in. (about 36 ft.).
Known as the V1310, the bus is equipped with A.E.C. Regal Mk. VI running gear, the power unit being an A.E.C. 690-cu.-in. underfloor engine developing 168 b.h.p. at 2,000 r.p.m. The transmission is of the Monocontrol type, having a fluid flywheel and separately mounted epicyclic four-speed gearbox.