FOR LESS THAN £50 ANTI—LOCK
Page 40
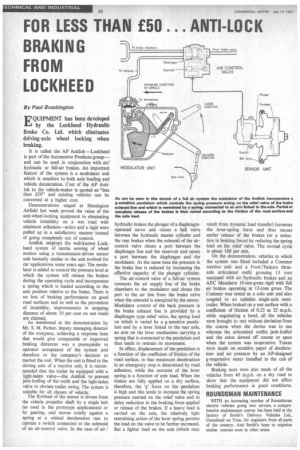
If you've noticed an error in this article please click here to report it so we can fix it.
BRAKING ')----bers FROM Air e,haust
LOCKHEED
By Paul Brockington
EQUIPMENT has been developed by the Lockheed Hydraulic Brake Co. Ltd. which eliminates driving-axle wheel locking when braking.
It is called the AP Antilok—Lockheed is part of the Automotive Products group— and can be used in conjunction with air/ hydraulic or full-air brakes. An important feature of the system is a modulator unit which is sensitive to both axle loading and vehicle deceleration. Cost of the AP Antilok to the vehicle-maker is quoted as "less than £50" and existing vehicles can be converted at a higher cost.
Demonstrations staged at Shenington Airfield last week proved the value of the anti-wheel-locking equipment in eliminating vehicle instability on a wet road with minimum adhesion—artics and a rigid were pulled up in a satisfactory manner instead of going completely out of control.
Antilok employs the well-known Lockheed system of inertia sensing of wheel motion using a transmission-driven sensor unit basically similar to the unit evolved for car applications some years ago. The modulator is added to control the pressure level at which the system will release the brakes during the operating cycle and incorporates a spring which is loaded according to the axle position relative to the frame. There is no loss of braking performance on good road surfaces and as well as the prevention of instability, improvements in stopping distance of about 10 per cent on wet roads are claimed.
As mentioned at the demonstration by Mr. S. M. Parker, deputy managing director of the company, achieving a response time that would give comparable or improved braking distances was a prerequisite to operator acceptance of the System and
therefore to the company's decision to market the unit. When the unit is fitted to the driving axle of a tractive unit, it is recommended that the trailer be equipped with a light-laden valve—the Antilok to prevent jack-knifing of the outfit and the light-laden valve to obviate trailer swing. The system is suitable for all classes of vehicle.
The flywheel of the sensor is driven from the vehicle propeller shaft by a single belt (as used in the prototype applications) or by gearing, and moves axially against a spring at a critical deceleration rate to operate a switch connected to the solenoid of an air-control valve. In the case of air /
hydraulic brakes the plunger of a diaphragmoperated servo unit closes a ball valve between the hydraulic master cylinder and the rear brakes when the solenoid of the aircontrol valve closes a port between the diaphragm line and the reservoir and opens a port between the diaphragm and the modulator. At the same time the pressure in the brake line is reduced by increasing the effective capacity of the plunger cylinder.
The air-control valve of a full-air system connects the air supply line of the brake chambers to the modulator and closes the port to the air line from the brake valve when the solenoid is energi2ed by the sensor. Modulator control of the back pressure in the brake exhaust line is provided by a diaphragm type relief valve, the spring load on which is varied by a g-sensitive pendulum and by a lever linked to the rear axle, an arm on the lever mechanism carrying a spring that is connected to the pendulum and thus tends to• restrain its movement.
In effect, displacement of the pendulum is a function of the coefficient of friction of the road surface, in that maximum deceleration in an emergency stop is determined by road adhesion, while the restraint of the lever spring is a function of axle load. When the brakes are fully applied on a dry surface, therefore, the 'g' force on the pendulum is high and this tends to increase the spring pressure exerted on the relief valve and to delay reduction in the braking force applied or release of the brakes. If a heavy load is carried on the axle, the relatively light restraining action of the lever spring permits the load on the valve to be further increased. But a lighter load on the axle (which may result from dynamic load transfer) increases the lever-spring force and thus causes earlier release of the brakes (or a reduction in braking force) by reducing the spring load on the relief valve. The normal cycle is about 180 per min.
On the demonstration, vehicles to which the system was fitted included a Comrner tractive unit and a Ford /Taskers threeaxle articulated outfit grossing 13 tons equipped with air /hydraulic brakes and an AEC Mandator 16-ton-gross rigid with full air brakes operating at 12-tons gross. The Commer was tested as a solo unit and also coupled to an unladen single-axle semitrailer. When braked on a wet surface with a coefficient of friction of 0.25 at 25 m.p.h, while negotiating a bend, all the vehicles were brought to rest without deviation from the course when the device was in use whereas the articulated outfits jack-knifed and the solos stewed off course or spun when the system was inoperative. Traces were made on sensitive paper of deceleration and air pressure by an AP-designed g-responsive meter installed in the cab of the vehicle.
Braking tests were also made of all the vehicles from 40 m.p.h. on a dry road to show that the equipment did not affect braking performance in good conditions.
ROUNDSMAN MAINTENANCE WITH an increasing number of aoundsman electric vehicles going into service, a comprehensive maintenance course has been held at the factory of Smith's Delivery Vehicles Ltd., Gateshead on Tyne, for engineers from all parts of the country. And Smith's hope to organize similar courses soon in other areas.