SIMPLE MECHANIC
Page 104
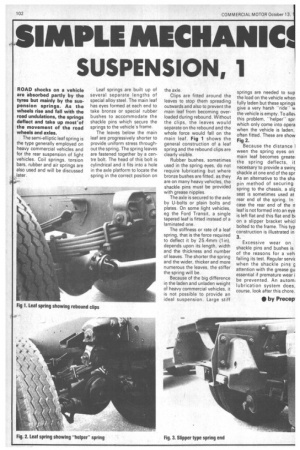
If you've noticed an error in this article please click here to report it so we can fix it.
SUSPENSION, 1
ROAD shocks on a vehicle are absorbed partly by the tyres but mainly by the suspension springs. As the wheels rise and fall with the road undulations, the springs deflect and take up most'of the movement of the road wheels and axles.
The semi-elliptic leaf spring is the type generally employed on heavy commercial vehicles and for the rear suspension of light vehicles. Coil springs, torsion bars, rubber and air springs are also used and will be discussed later. Leaf springs are built up of several separate lengths of special alloy steel. The main leaf has eyes formed at each end to take bronze or special rubber bushes to accommodate the shackle pins which secure the springs to the vehicle's frame.
The leaves below the main leaf are progressively shorter to provide uniform stress throughout the spring. The spring leaves are fastened together by a centre bolt. The head of this bolt is cylindrical and it fits into a hole in the axle platform to locate the spring in the correct position on the axle.
Clips are fitted around the leaves to stop them spreading outwards and also to prevent the main leaf from becoming overloaded during rebound. Without the clips, the leaves would separate on the rebound and the whole force would fall on the main leaf. Fig 1 shows the general construction of a leaf spring and the rebound clips are clearly visible.
Rubber bushes, sometimes used in the spring eyes, do not require lubricating but where bronze bushes are fitted, as they are on many heavy vehicles, the shackle pins must be provided with grease nipples.
The axle is secured to the axle by U-bolts or plain bolts and plates. On some light vehicles, eg the Ford Transit, a single tapered leaf is fitted instead of a laminated one.
The stiffness or rate of a leaf spring, that is the force required to deflect it by 25.4mm (1 in), depends upon its length, width and the thickness and number of leaves. The shorter the spring and the wider, thicker and more numerous the leaves, the stiffer the spring will be.
Because of the big difference in the laden and unladen weight of heavy commercial vehicles, it is not possible to provide an ideal suspension. Large stiff springs are needed to sup the load on the vehicle when fully laden but these springs give a very harsh "ride" w the vehicle is empty. To alleN, this problem, "helper" spr which only come into opera when the vehicle is laden, often fitted. These are show Fig 2.
Because the distance I ween the spring eyes on main leaf becomes greate[ the spring deflects, it necesSarylo provide a swinc shackle at one end of the spr As an alternative to the sha pin method of securing spring to the chassis, a slit seat is sometimes used at rear end of the spring. In case the rear end of the rt. leaf is not formed into an eye is left flat and this flat end bi on a slipper bracket whicl bolted to the frame. This typ construction is illustrated in 3.
Excessive wear on shackle pins and bushes is of the reasons for a veh failing its test. Regular servic when the shackle pins g attention with the grease gu essential if premature wear i be prevented. An autorm lubrication system does, course, look after this chore.
• by Precep.