Works Trucks • Aid Textile Rehabilitation
Page 38
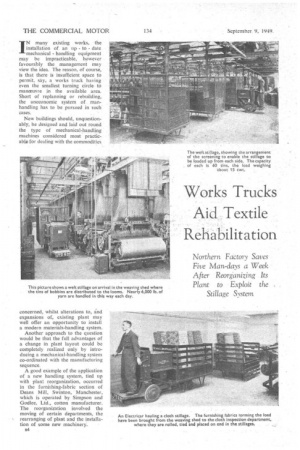
Page 39
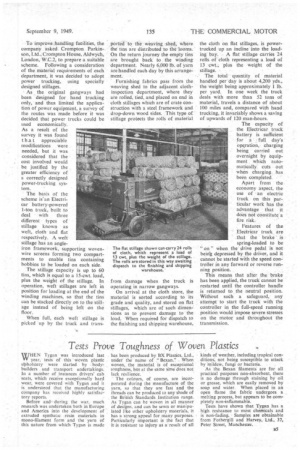
If you've noticed an error in this article please click here to report it so we can fix it.
Northern Factory Saves Five Man-days a Week After Reorkanizing Its Plant to Exploit the
Stillage System
IN many existing works, the installation of an up to date mechanical handling equipment may be impracticable, however favourably the management may view the idea. The reason. of course, is that there is insufficient space to permit, say, a works truck having even the smallest turning circle to manceuvre in the available area. Short of replanning or rebuilding, the uneconomic system of. manhandling has to be pursued in such cases.
New buildings should, unquestionably, be designed and laid out round the type of mechanical-handling machines considered most practicable for dealing with the commodities concerned, whilst alterations to, and expansions of, existing plant may well offer an opportunity to install a modern materials-handling system.
Another approach to the question would be that the full advantages of a change in plant layout could be completely realized only by introducing a mechanical-handling system co-ordinated with the manufacturing sequence.
A good example of the application of a new handling system, tied up with plant reorganization, occurred in the furnishing-fabric section of Deans Mill, Swinton, Manchester, which is operated by Simpson and Godlee, Ltd., cotton manufacturer. The reorganization involved the moving of certain departments, the rearranging of plant and the installation of some new machinery.
n4 To improve .handling facilities, the company asked Crompton Parkin son, Ltd., Crompton House, Aldwych, London, W.C.2, to prepare a suitable scheme. Following a consideration of the:material requirements of each department, it was decided to adopt power trucking, using specially designed stillages.
As the original gangways had been designed for hand trucking only, and thus limited the applica tion of power equipment, a survey of the routes was made before it was decided that power trucks could be used economically. As a result of the survey it was found t hat appreciable modifications were needed, but it was considered that the cost involved would be justified by the greater efficiency of a correctly designed power-trucking system, The basis of the scheme is'an Electri car battery-powered 1-ton truck, built to deal with three different types of stillage known as weft, cloth and flat respectively. A weft stillage has an angleiron framework, supporting woven wire screens forming two compartments to enable tins containing bobbins to be loaded on each side.
The stillage capacity is up to 60 tins, which is equal to a 15-cwt. load, plus the weight of the stillage. In operation, weft stillages are left in position for loading at the end of the
winding machines, so that the tins can be stacked directly on to the still-age instead of being left on the floor.
When full, each weft stillage is picked up by the truck and tram ported to the weaving, shed, where the tins are distributed to the looms. On the return journey the empty tins are brought back to the winding department. Nearly 6,000 1.13. of yarn are handled each day by this arrangement.
Furnishing fabrics pass from the weaving shed to the adjacent clothinspection department, where they are rolled, tied, and placed on end in cloth stillages which are of crate construction with a steel framework and drop-down wood sides. This type of stillage protects the rolls of material from damage when the truck is operating in narrow gangways.
On arrival at the cloth store, the material is sorted according to its grade and quality, and stored on flat
stillages, which are of such dimensions as to prevent damage to the load. When required for dispatch to the finishing and shipping warehouse, the cloth on flat stillages, is powertrucked up an incline into the load ing bay. A flat stillage carries 24 rolls of cloth representing a load of 13 cwt., plus the weight of the stillage.
The total quantity of material handled per day is about 4,200 yds., the weight being approximately 1 lb. per yard. In one week the truck deals with more than 52 tons of material, travels a distance of about WO miles and, compared With hand trucking, it invariably shows a saving of upwards of 120 man-hours.
The capacity of the Electricar truck battery is sufficient for a full day's operation, charging being carried out overnight by equipment which automatically' cuts Out when charginghas•
been completed.
Apart from the. economy aspect, the use of an electric truck on this particular work has the advantage that it does not constitute 'a fire risk.
Features of the Electricar truck are that the brake is
• spring-loaded to be "on ' when the drive pedal is not being depressed by the driver, and it cannot be started with the speed controller in any forward or reverse running position.
This means that after the brake has been applied, the truck cannot be restarted until the controller handle is returned to , the neutral position. Without such a safeguard, any attempt to start the truck with the controller in the full-speed running position would impose severe Stresses on the motor and throughout the transmission.