• A Latin American blast of Gloria Estephan fills the
Page 60
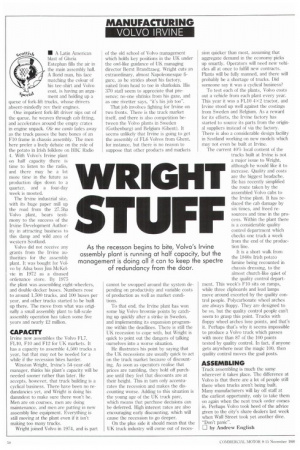
If you've noticed an error in this article please click here to report it so we can fix it.
air in the main assembly hall. A florid man, his face matching the colour of his tee-shirt and Volvo coat, is having an argu ment and holding up a queue of fork-lift trucks, whose drivers absent-mindedly rev their engines.
One impatient fork-lift driver nips out of the queue. he weaves through cab fitting, and accelerates around the empty crates in engine unpack. Ole me canto fades away as the truck passes the bare bones of an Fit) frame in chassis assembly. The men here prefer a lively debate on the role of the potato in Irish folklore on BBC Radio 4. With Volvo's Irvine plant on half capacity there is time to listen to the radio, and there may he a lot more time in the future as production dips down to a quarter, and a four-day week is mooted.
The Irvine industrial site. with its huge paper mill up the road from the 27.5ha Volvo plant, bears testimony to the success of the Irvine Development Authority in attracting business to this damp and wild area of western Scotland.
Volvo did not receive any grants from the Irvine authorities for the assembly plant. It was bought for Volvo by Ailsa boss Jim McKelvie in 1972 as a disused ordenance store. By 1975 the plant was assembling eight-wheelers, and double-decker buses. Numbers rose to around 1,500 trucks, and 100 buses per year, and other trucks started to be built up there. The move from what was originally a small assembly plant to full-scale assembly operation has taken some five years and nearly million.
CAPACITY
Irvine now assembles the Volvo FL7, ELK FIO and F12 for UK markets. It has a capacity to assemble 4,500 trucks a year, but that may not be needed for a while if the recession bites harder.
Winston Wright, Irvine's 54-year-old manager, thinks his plant's capacity will be needed sooner rather than later. He accepts, however, that truck building is a cyclical business. There have been no redundancies yet, and Wright is doing his damndest to make sure there won't be. Men are on courses, men are doing maintenance, and men are putting in new assembly line equipment. Everything is still moving at the plant even if it isn't making too many trucks.
Wright joined Volvo in 1974, and is part of the old school of Volvo management which holds key positions in the UK under the owl-like guidance of UK managing director Bernt Brandtzaeg. Wright cuts an extraordinary, almost Napoleonesque figure, as he strides about his factory, suited from head to toe in sharkskin. His 370 staff seem to appreciate that presence; no-one shrinks from his gaze, and as one rivetter says, "it's his job too".
That job involves fighting for Irvine on two fronts. There is the truck market itself, and there is also competition between the Volvo plants in Sweden (Gothenburg) and Belgium (Ghent). It seems unlikely that Irvine is going to get the assembly of Fiji Volvos from Ghent, for instance, but there is no reason to suppose that other products and markets cannot be swopped around the system depending on productivity and variable costs of production as well as market conditions.
To that end, the Irvine plant has won some big Volvo brownie points by catching up quickly after a strike in Sweden, and implementing its expansion programme within the deadlines. There is still the UK recession to cope with, but Wright is quick to point out the dangers of talking ourselves into a worse situation.
He illustrates his point by saying that the UK recessions are usually quick to act on the truck market because of discounting. As soon as operators realise that prices are tumbling, they hold off purchase until they feel that discounts are at their height. This in turn only accenturates the recession and makes the discounting worse. Adding to this situation is the young age of the UK truck parc, which means that purchase decisions can be deferred. High interest rates are also encouraging early discounting, which will cause the recession to go deeper.
On the plus side it should mean that the UK truck industry will come out of reces sion quicker than most, assuming that aggregate demand in the economy picks up smartly. Operators will need new vehicles all at once to fulfill new contracts. Plants will be fully manned, and there will probably be a shortage of trucks. Did someone say it was a cyclical business?
To test each of the plants, Volvo costs out a vehicle from each plant every year. This year it was a FL10 4x2 tractor. and Irvine stood up well against the costings from Sweden and Belgium. As a reward for its efforts, the Irvine factory has started to source its parts from the original suppliers instead of via the factory. There is also a considerable design facility in Scotland working on new models which may not even be built at Irvine.
The current 40% local content of the trucks built at Irvine is not a major issue to Wright, although he would like it to increase. Quality and costs are the biggest headache. He has recently simplified the route taken by the assembled Volvo cabs to the Irvine plant. It has reduced the cab damage by six times, and freed resources and time in the process. Within the plant there is a considerable quality control department which checks one truck a week from the end of the production line.
It is a short walk from the 1840s Irish potato famine being recounted in chassis dressing, to the almost church-like quiet of the quality control department. This week's F10 sits on ramps, while three clipboards and lead lamps move around escorted by the quality control people. Polycarbonate wheel arches are always floppy. They are designed to be so, but the quality control people can't seem to grasp this point. Trucks with floppy wheel arches lose points, and that's it. Perhaps that's why it seems impossible to produce a Volvo truck which passes with more than 87 of the 100 points tested by quality control. In fact, if anyone gets anywhere near the magic 100, then quality control moves the goal posts.
HT
ASSEMBLING
Truck assembling is much the same wherever it takes place. The difference at Volvo is that there are a lot of people still there when trucks aren't being built. Many manufacturers will lay off staff at the earliest opportunity, only to take them on again when the next truck order comes in. Perhaps Volvo took heed of the advice given to the city's share dealers last week when Wall Street took yet another dive. "Don't panic".
0 by Andrew English