SCANIAS 16-TONNER
Page 52
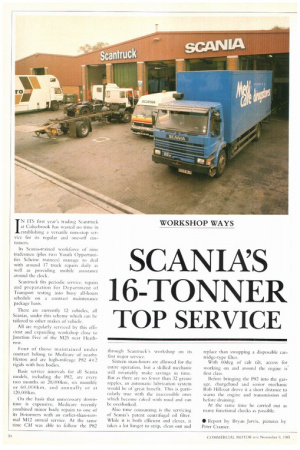
Page 53
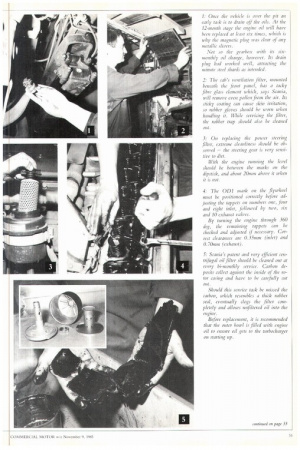
Page 55
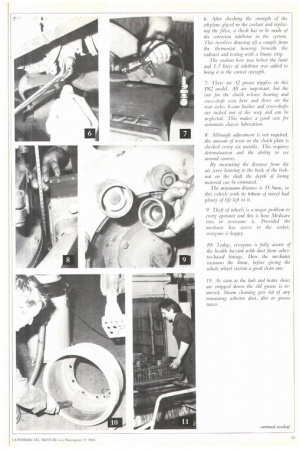
Page 56
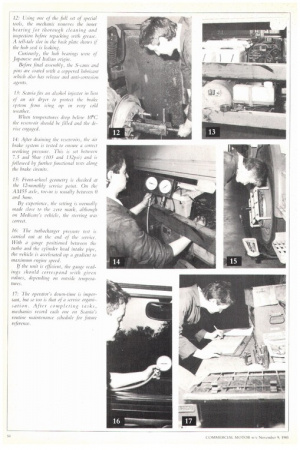
If you've noticed an error in this article please click here to report it so we can fix it.
TOP SERVICE
IN ITS first year's trading Scantruck at CoInebrook has wasted no time in establishing a versatile non-stop service for its regular and one-off customers.
Its Scania-trained workforce of nine tradesmen (plus two Youth Opportunities Scheme trainees) manage to deal with around 17 truck repairs daily as well as providing mobile assistance around the clock.
Scantruck tits periodic service, repairs and preparation for Department of Transport testing into busy all-hours schedule on a contract maintenance package basis.
There are currently 12 vehicles, all Scanias, under this scheme which can be tailored to other makes of vehicle.
All are regularly serviced by this efficient and expanding workshop close to Junction Five of the M25 near Heathrow.
Four of those maintained under contract belong to Medicare of nearby Heston and are high-mileage P82 4X2 rigids with box bodies.
Basic service intervals for all Scania models, including the P82, are every two months or 20,000km, six monthly or 60,000km, and annually or at 120,0(X)kin.
On the basis that unnecessary downtime is expensive, Medicare recently combined minor body repairs to one of its 16-tonners with an earlier-than-normal M12 annual service. At the same time CM was able to follow the 1>82 through Scantruck's workshop on its first major service.
Sixteen man-hours are allowed for the enure operation, but a skilled mechanic will invariably make savings in time. But as there are no fewer than 32 grease nipples, an automatic lubrication system would he of great benefit. This is particularly true with the inaccessible ones which become caked with mud and can be overlooked.
Also time consuming is the servicing of Scania's patent centrifugal oil filter. While it is both efficient and clever, it takes a lot longer to strip, clean out and replace than swopping a disposable cartridge-type filter. With 60deg of cab tilt, access for working on and around the engine is first class.
Before bringing the P82 into the garage, chargehand and senior mechanic Rob Ifillcoat drove it a short distance to warm the engine and transmission oil before draining.
At the same time he carried out as many functional checks as possible.
• Report by Bryan Jarvis, pictures by Peter Cramer,
1: Once the vehicle is over the pit an early task is to drain off the oils. At the 12-month stage the engine oil will have been replaced at least six times, which is why the magnetic plug was clear of any metallic slivers.
Not so the gearbox with its sixmonthly oil change, however. Its drain phtg had worked well, attracting the minute steel shards as intended.
2: The cab's ventilation .filter, in beneath. the .front panel, has a tacky _fibre glass element which., says Scan ia, will remove even pollen from the air. Its sticky coating can cause skin irritation, so rubber gloves should be worn when handling it. While servicing the filter, the rubber trap should also be cleaned Out.
3: On replacing the power steering filter, extreme cleanliness should be observed — the steering gear is very sensitive to dirt.
With the engine running the level should be between the marks on the dipstick, and about 20mm above it when it is not.
4: The 001 mark on the flywheel must be positioned correctly before adjusting the lappets on numbers one, four and eight inlet, followed by two, six and 10 exhaust valves.
By turning the engine through 360 deg, the remaining tappets can be checked and adjusted if necessary. Correct clearances are 0.35mm (inlet) and 0.70mm (exhaust).
5: Scania's patent and very efficient centrifugal oil filter should be cleaned out at every hi-monthly service. Carbon deposits collect against the inside of the rotor casing and have to he carefully cut out.
Should this service task be missed the carbon, which resembles a thick rubber seal, eventually clogs the _filter completely and allows unfiltered oil into the engine.
Before replacement, it is recommended that the outer bowl is filled with engine oil to ensure oil gets to the turbocharger on starting up. 6: After checking the siren ylt of the ethylene.glycol in the coolant and replacing the .filter, a check has to be made of the corrosion nrhibitor in the system. This involves dratviv off a sample front the thennostat housing beneath the radiator and testing with a litmus strip.
The coolant here was below the limit mvi 1,5 litres of inhibitor was added to bring it to the correct stymy!).
• There are 32 grease nipples oil this
• me model. All are important, but the one for the clutch release bearing and cross-shaft seen here and those on the rear axles S-Calli bushes and cross-shafts are !Inked out of the way and can be vi: leer This makes a .Q0 011 1.115C for automatic chassis lubrication.
8: Although adjustment is not required, the amount of wear on the clutch plate is checked every six months. This requires determination and the ability to see around corners.
By Medsuring the distance from the air servo housing to the back of the lothnot on the shaft the depth of lining material can be estimated.
The tninimmit distance is .33,5fmn, so this vehicle with its 64mm of travel had plenty of tile left in it.
9: Thcft of wheels is a major problem to every operator and this is how Medicare tries to overcome it. Provided the mechanic has af OSS to the socket, everyone is happy.
10: Today, everyone is jilny aware of the health hazard with dust ,h; om asbestos-based linings. Here the Mechanic vacuums the drum, bcfiwe ,Oving the whole ivitecl station a good clean out.
II: As soon as the hub and brake shoes are stripped down the old grease is removed. Steam cleaning gets rid of any remaining asbestos dust, dirt or grease traces,
12: Using one of die set of special tools, the mechanic removes the inner bearing for thorough cleaning and inspection bq-ore repacking with grease. A tell-tale slot in the back plate shows if the hub seal is leak*.
Curiously, the hub hearings were of Japanese and Italian origin.
Before final assoinbly, the Scams and pifIS are coated with a coppered lubricant n,hich also has release and anti-corroshm agents.
13: Scania.fits an alcohol in in lieu of an air dryer to protect the brake systein "'Win Ong up in very cold weather.
11/h(71 temp crib drop below UPC the reservoir should be _tilled and the device engaged.
14: Auer draining the reservoirs, the air brakr system is tested to ensure a correct working pressure. This is set between 7.5 and 9/tar (103 and 1.32psi) and is follolf,ed by _further _functional tests aloni; the brake circuits.
15: Front-wheel geometry is checked at the 12-monthly service point. On aw A A455 axle, toe-in is iusually between and Junn.
By experience, the setting is normally inade close to the zero 'nark, although on Medicare's vehicle, the steering was Correct.
16: The turbocharger pressure test is carried out at the end of the service. With a gauge positioned between the turbo and the cylinder It coil intake pipe, the 1,elticle is accelerated op a gradient to maximum engine speed.
If the unit is efficient, the gauge readings should correspond with given values, depending on outside temperahires.
17: The operator's down-lime is important, but so too is That of a service organisation. After co itiji let i ni tasks, mechanics record each one on Samba's routine maintenance schedule for .filtrere reference.