Operator CPC Part 19 Welcome to Part 19 of our
Page 17
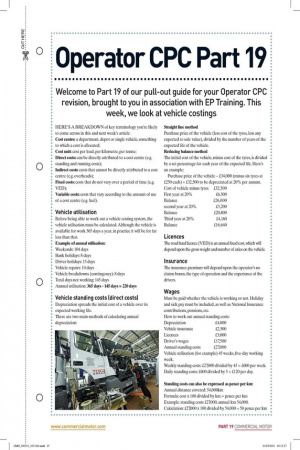
Page 18
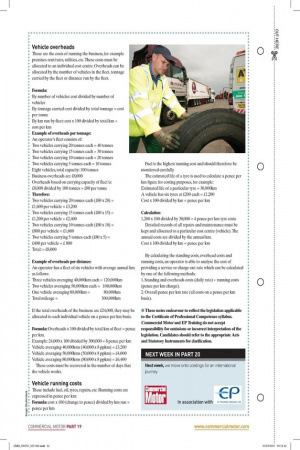
If you've noticed an error in this article please click here to report it so we can fix it.
pull-out guide for your Operator CPC revision, brought to you in association with EP Training. This week, we look at vehicle costings HERE'S A BREAKDOWN of key terminology you're likely to come across in this and next week's article: Cost centre: a department, depot or single vehicle, something to which a cost is allocated; Cost unit cost per load, per kilometre, per tonne; Direct costs: can be directly attributed to a cost centre (e.g. standing and running costs); Indirect costs: costs that cannot be directly attributed to a cost centre (e.g. overheads); Fixed costs: costs that do not vary over a period of time (e.g. VED); Variable costs: costs that vary according to the amount of use of a cost centre (e.g. fuel).
Vehicle utilisation Before being able to work out a vehicle costing system, the vehicle utilisation must be calculated. Although the vehicle is available for work 365 days a year, in practice it will be for far less than that.
Example of annual utilisation: Weekends: 104 days Bank holidays: 8 days Driver holidays: 15 days Vehicle repairs: 10 days Vehicle breakdowns (contingency): 8 days Total days not working: 145 days Annual utilisation: 365 days 145 days = 220 days Vehicle standing costs (direct costs) Depreciation spreads the initial cost of a vehicle over its expected working life.
There are two main methods of calculating annual depreciation: Straight line method Purchase price of the vehicle (less cost of the tyres, less any expected re-sale value), divided by the number of years of the expected life of the vehicle.
Reducing balance method The initial cost of the vehicle, minus cost of the tyres, is divided by a set percentage for each year of the expected life. Here's an example: Purchase price of the vehicle —£34,000 (minus six tyres at £250 each) = £32,500 to be depreciated at 20% per annum.
Cost of vehicle minus tyres £32,500 First year at 20% £6,500 Balance £26,000 second year at 20% £5,200 Balance £20,800 Third year at 20% £4,160 Balance £16,640 Licences The road fund licence (VED) is an annual fixed cost, which will depend upon the gross weight and number of axles on the vehicle.
Insurance The insurance premium will depend upon the operator's no claims bonus, the type of operation and the experience of the drivers.
Wages Must be paid whether the vehicle is working or not. Holiday and sick pay must be included, as well as National Insurance contributions, pensions, etc.
How to work out annual standing costs: Depreciation £4,000 Vehicle insurance £2,500 Licences £3,000 Driver's wages £17,500 Annual standing costs £27,000 Vehicle utilisation (for example) 45 weeks, five-day working week.
Weekly standing costs: £27,000 divided by 45 = £600 per week. Daily standing costs: £600 divided by 5 = £120 per day.
Standing costs can also be expressed as pence per km: Annual distance covered: 54,000km Formula: cost x 100 divided by km = pence per km Example: standing costs £27,000, annual km 54,000.
Calculation: £27,000 x 100 divided by 54,000 = 50 pence per km Vehicle overheads These are the costs of running the business, for example premises rent/rates, utilities, etc. These costs must be allocated to an individual cost centre. Overheads can be allocated by the number of vehicles in the fleet, tonnage carried by the fleet or distance run by the fleet.
Formula: By number of vehicles: cost divided by number of vehicles By tonnage carried: cost divided by total tonnage = cost per tonne By km run by fleet: cost x 100 divided by total km = cost per km Example of overheads per tonnage: An operator's fleet consists of: Two vehicles carrying 20 tonnes each = 40 tonnes Two vehicles carrying 15 tonnes each = 30 tonnes Two vehicles carrying 10 tonnes each = 20 tonnes Two vehicles carrying 5 tonnes each = 10 tonnes Eight vehicles, total capacity: 100 tonnes Business overheads are £8,000 Overheads based on carrying capacity of fleet is: £8,000 divided by 100 tonnes = £80 per tonne Therefore: Two vehicles carrying 20 tonnes each (£80 x 20) = £1,600 per vehicle = £3,200 Two vehicles carrying 15 tonnes each (£80 x 15) = £1,200 per vehicle = £2,400 Two vehicles carrying 10 tonnes each (£80 x 10) = £800 per vehicle = £1,600 Two vehicles carrying 5 tonnes each (£80 x 5) = £400 per vehicle = £ 800 Total: = £8,000 Example of overheads per distance: An operator has a fleet of six vehicles with average annual km as follows: Three vehicles averaging 40,000km each = 120,000km Two vehicles averaging 50,000km each = 100,000km One vehicle averaging 80,000km = 80,000km Total mileage = 300,000km If the total overheads of the business are £24,000, they may be allocated to each individual vehicle on a pence per km basis.
Formula: Overheads x 100 divided by total km of fleet = pence per km.
Example: 24,000 x 100 divided by 300,000 = 8 pence per km Vehicle averaging 40,000kms (40,000 x 8 ppkm) = £3,200 Vehicle averaging 50,000kms (50,000 x 8 ppkm) = £4,000 Vehicle averaging 80,000kms (80,000 x 8 ppkm) = £6,400 These costs must be recovered in the number of days that the vehicle works.
Vehicle running costs These include fuel, oil, tyres, repairs, etc. Running costs are expressed in pence per km: Formula: cost x 100 (change to pence) divided by km run = pence per km Fuel is the highest running cost and should therefore be monitored carefully.
The estimated life of a tyre is used to calculate a pence per km figure for costing purposes, for example: Estimated life of a particular tyre = 30,000km A vehicle has six tyres at £200 each = £1,200 Cost x 100 divided by km = pence per km Calculation: 1,200 x 100 divided by 30,000 =4 pence per km tyre costs Detailed records of all repairs and maintenance must be kept and allocated to a particular cost centre (vehicle). The annual costs are divided by the annual km.
Cost x 100 divided by km = pence per km By calculating the standing costs, overhead costs and running costs, an operator is able to analyse the cost of providing a service or charge-out rate which can be calculated by one of the following methods: 1. Standing and overheads costs (daily rate) + running costs (pence per km charge).
2. Overall pence per km rate (all costs on a pence per km basis).
• These notes endeavour to reflect the legislation applicable to the Certificate of Professional Competence syllabus. Commercial Motor and EP Training do not accept responsibility for omissions or incorrect interpretation of the legislation. Candidates should refer to the appropriate Acts and Statutory Instruments for clarification.