Unbending a bent National
Page 41
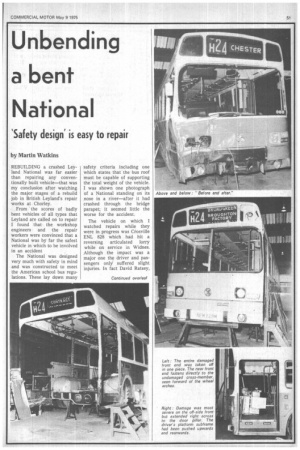
Page 42
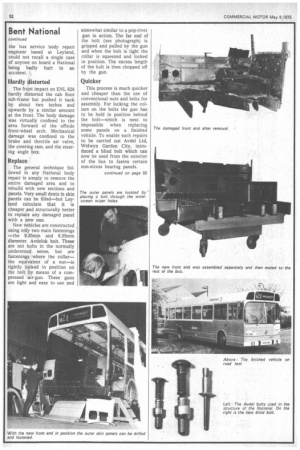
Page 45
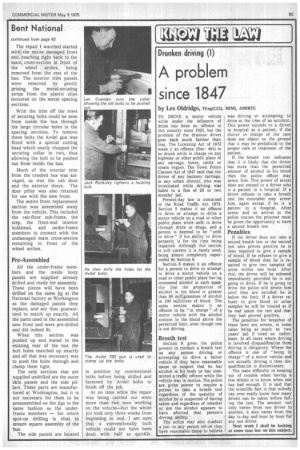
If you've noticed an error in this article please click here to report it so we can fix it.
'Safety design' is easy to repair
by Martin Watkins
REBUILDING a crashed Leyland National was far easier than repairing any conventionally built vehicle—that was my conclusion after watching the major stages of a rebuild job in British Leyland's repair works at Chorley.
From the scores of badly bent vehicles of all types that Leyland are called on to repair I found that the workshop engineers and the repair workers were convinced that a National was by far the safest vehicle in which to be involved in an accident The National was designed very much with safety in mind and was constructed to meet the American school bus regulations. These lay down many safety criteria including one which states that the bus roof must be capable of supporting the total weight of the vehicle. I was shown one photograph of a National standing on its nose in a river—after it had crashed through the bridge parapet; it seemed little the worse for the accident.
The vehicle on which I watched repairs while they were in progress was Crosville ENL 828 which had hit a reversing articulated lorry while on service in Widnes. Although the impact was a major one the driver and passengers only suffered slight injuries. In fact David Ratsey,
the bus service body repair engineer based at Leyland, could not recall a single case of anyone on board a National being badly hurt in an accident. ,
Hardly distorted
The front impact on ENL 828 hardly distorted the cab floor sub-frame but pushed it back by about two inches and upwards by a similar amount at the front. The body damage was virtually confined to the area forward of the offside front-wheel arch. Mechanical damage was confined to the brake and throttle air valve, the steering ram, and the steering angle box.
Replace
The general technique followed in any National body repair is simply to remove the entire damaged area and to rebuild with new sections and panels. Very small dents in skin panels can be filled—but Leyland calculate that it is cheaper and structurally better to replace any damaged panel with a new one.
New vehicles are constructed using only two main fastenings —the 9.35mm and 6.35mm diameter. Avdelok bolt. These are not bolts in the normally understood sense, but are fastenings where the collar— the equivalent of a nut—is tightly locked in position on the bolt by means of a compressed air-gun. These guns are light and easy to use and somewhat similar to a pop-rivet gun in action. The far end of the bolt (see photograph) is gripped and pulled by the gun and when the bolt is tight the collar is squeezed and locked in position. The excess length of the bolt is then chopped off by the gun.
Quicker
This process is much quicker and cheaper than the use of conventional nuts and bolts for assembly. For locking the collars on the bolts the gun has to be held in position behind the bolt—which is next to impossible when replacing some panels on a finished vehicle. To enable such repairs to be carried out Avdel Ltd, Welwyn Garden City, introduced a blind bolt which can now be used from the exterior of the bus to fasten certain non-stress bearing panels. The repair I watched started with the entire damaged front end, reaching right back to the main cross-section in front of the wheel arches, being removed from the rest of the bus. The interior trim panels were removed by gently prising the metal-securing strips from the plastic clips mounted on the metal spacing sections.
With the trim off the rows of securing bolts could be seen from inside the bus through the large circular holes in the spacing sections. To remove these bolts the Avdel gun was fitted with a special cutting head which neatly chopped the securing collar in two, thus allowing the bolt to be pushed out from inside the bus.
Much of the interior trim from the crashed bus was salvaged, as was the cab door and the exterior doors. The door pillar was also retained for use with the new front.
The entire front replacement section was assembled away from the vehicle. This included the cab-floor sub-frame, the step, the front-end interior bulkhead, and under-frame members to connect with the undamaged main cross-section remaining in front of the wheel arches.
Pre-Assembled
All the under-frame members and the inside body panels are supplied already drilled and ready for assembly. These pieces will have been drilled on the same jig at the National factory at Workington as the damaged panels they replace, and are thus guarantteed to match up exactly. All the parts used in the assembled new front end were pre-drilled and did indeed fit.
When this section was pushed up and mated to the existing rear of the bus the bolt holes matched up exactly and all that was necessary was to push the bolts through and clamp them tight.
The only sections that are supplied undrilled are the outer skin panels and the side pillars. These parts are manufactured at Workington, but it is not necessary for them to be preassembled on the jigs in the same fashion as the underframe members — for which spot-on drilling is vital to ensure square assembly of the bus.
The side panels are located in position by conventional bolts before being drilled and fastened by Avdel bolts to finish off the job.
At no time while the repair was being carried out were more than two men working on the vehicle—but the whole joi) took only three weeks from beginning to end. I am sure that a conventionally built vehicle could not have been dealt with half as quickly.