Bodies which like to work under pressure
Page 52
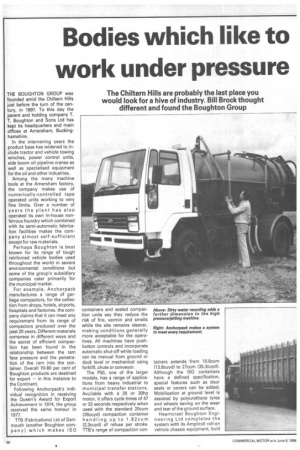
Page 53
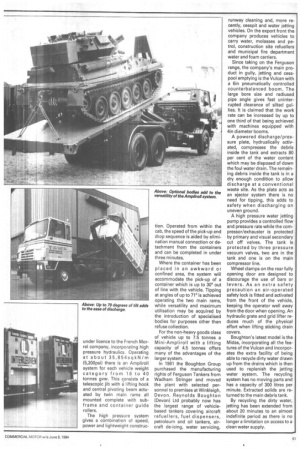
If you've noticed an error in this article please click here to report it so we can fix it.
THE BOUGHTON GROUP was founded amid the Chiltern Hills just before the turn of the century, in 1897. To this day the parent and holding company T. T. Boughton and Sons Ltd has kept its headquarters and main offices at Amersham, Buckinghamshire.
In the intervening years the product base has widened to include tractor and vehicle towing winches, power control units, side boom oil pipeline cranes as well as specialised equipment for the oil and other industries.
Among the many machine tools at the Amersham factory, the company makes use of numerically-controlled tape operated units working to very fine limits. Over a number of years the plant has also operated its own in-house nonferrous foundry which combined with its semi-automatic fabrication facilities makes the company almost self-sufficient except for raw materials.
Perhaps Boughton is best known for its range of tough reinforced vehicle bodies used throughout the world in severe environmental conditions but some of the group's subsidiary companies cater primarily for the municipal market.
For example, Anchorpack manufactures a range of garbage compactors, for the collection from shops, hotels, airports, hospitals and factories, the company claims that it can meet any requirement from its range of compactors produced over the past 20 years. Different materials compress in different ways and the secret of efficient compaction has been found in the relationship between the ram face pressure and the penetration of the ram into the container. Overall 70-80 per cent of Boughton products are destined for export — in this instance to the Continent.
Following Anchorpack's individual recognition in receiving the Queen's Award for Export Achievement in 1974, the group received the same honour in 1977.
TTB (Fabrications) Ltd of Dartmouth (another Boughton company) which makes ISO containers and sealed compaction units say they reduce the risk of fire, vermin and smells while the site remains cleaner, making conditions generally more acceptable for the operatives. All machines have pushbutton controls and incorporate automatic shut-off while loading can be manual from ground or dock level or mechanical using forklift, chute or conveyor.
The P50, one of the larger models, has a range of applications from heavy industrial to municipal transfer stations. Avzilable with a 20 or 30hp motor, it offers cycle times of 47 or 32 seconds respectively when used with the standard 20cum (26cuyd) compaction container handling up to 1.8 2cum (2.3cuyd) of refuse per stroke. TTB's range of compaction con tainers extends from 10.6cum (13.8cuyd) to 27cum (35.3cuyd). Although the ISO containers have a defined specification, special features such as door seals or covers can be added. Mobilisation at ground level is assisted by polyurethane tyres and wheels saving on the wear and tear of the ground surface.
Hearncrest Boughton Engi neering Ltd completes the system with its Ampliroll roll-on vehicle chassis equipment, built under licence to the French Morrel company, incorporating high pressure hydraulics. Operating at about 35,854 sqkN/m (5,200psi) there is an Ampliroll system for each vehicle weight category from 1.6 to 40 tonnes gvw. This consists of a telescopic jib with a lifting hook and central pivoting beam actuated by twin main rams all mounted complete with subframe and container guide rollers.
The high pressure system gives a combination of speed, power and lightweight construc tion. Operated from within the cab, the speed of the pick-up and drop sequence is aided by elimination manual connection or detachment from the containers and can be completed in under three minutes.
Where the container has been placed in an awkward or confined area, the system will accommodate the pick-up of a container which is up to 30° out of line with the vehicle. Tipping at angles of up to 71° is achieved operating the two main rams, while versatility and maximum utilisation may be acquired by the introduction of specialised bodies for purposes other than refuse collection.
For the non-heavy goods class of vehicle up to 7.5 tonnes a Mini-Ampliroll with a lifting capacity of 4.5 tonnes offers many of the advantages of the larger system.
In 1981 the Boughton Group purchased the manufacturing rights of Ferguson Tankers from Wadham Stringer and moved the plant with selected personnel to premises at Winkleigh, Devon. Reynolds Boughton (Devon) Ltd probably now has the largest range of vehiclebased tankers covering aircraft refuellers, fuel dispensers, petroleum and oil tankers, aircraft de-icing, water servicing,
runway cleaning and, more recently, cesspit and water jetting vehicles. On the export front the company produces vehicles to carry water, molasses and petrol, construction site refuellers and municipal fire department water and foam carriers.
Since taking on the Ferguson range, the company's main product in gully, jetting and cesspool emptying is the Vulcan with a 6in pneumatically controlled counterbalanced boom. The large bore size and radiused pipe angle gives fast uninterrupted clearance of silted gullies. It is claimed that the work rate can be increased by up to one third of that being achieved with machines equipped with 4in diameter booms.
A powered discharge/pressure plate, hydrualically activated, compresses the debris inside the tank and extracts 80 per cent of the water content which may be disposed of down the foul water drain. The remaining debris inside the tank is in a dry enough condition to allow discharge at a conventional waste site. As the plate acts as an ejector system there is no need for tipping, this adds to safety when discharging on uneven ground.
A high pressure water jetting pump provides a controlled flow and pressure rate while the compressor/exhauster is protected by primary and visual secondary cut off valves. The tank is protected by three pressure vacuum valves, two are in the tank and one is on the main compressor line.
Wheel clamps on the rear fully opening door are designed to discourage the use of bars or levers. As an extra safety precaution an air-operated safety lock is fitted and activated from the front of the vehicle, keeping the operator well away from the door when opening. An hydraulic grate and grid lifter reduces much of the physical effort when lifting sticking drain covers.
Boughton's latest model is the Midas, incorporating all the features of the Vulcan and incorporates the extra facility of being able to recycle dirty water drawn up from the drains which is then used to replenish the jetting water system. The recycling system has no moving parts and has a capacity of 300 litres per minute. Extracted solids are returned to the main debris tank.
By recycling the dirty water, jetting has been extended from about 20 minutes to an almost indefinite period as there is no longer a limitation on access to a clean water supply.