IRUCKS S (
Page 40
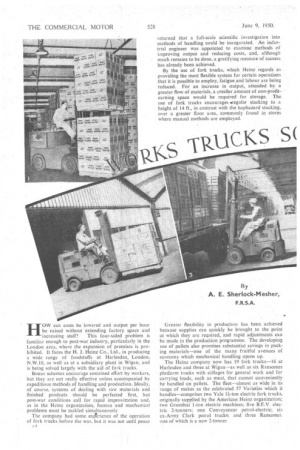
Page 41
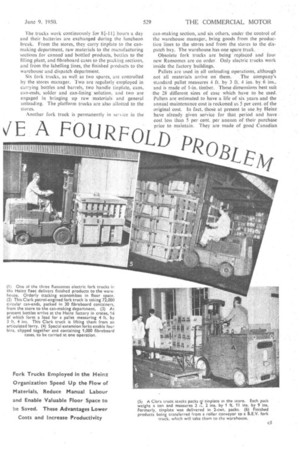
Page 42
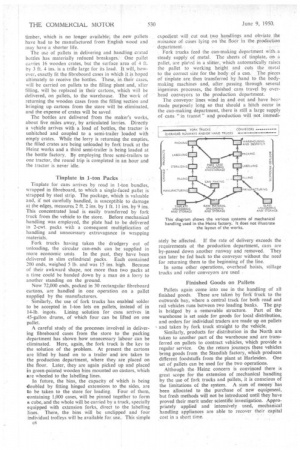
If you've noticed an error in this article please click here to report it so we can fix it.
VE A FOURFOLD
fly A. E. Sherlock-Mesher, F.R.S.A. returned that a full-scale scientific investigation into methods of handling could beinaugurated. An industrial engineer was appointed to examine methods of iinproving output and reducing costs, and, although much remains to be done, a gratifying measure of success has already been achieved.
By the use of fork trucks, which Heinz regards as providing the most flexible system for certain operations that it is possible to employ, fatigue and labour are being reduced. For an increase in output, attended by a greater flow of materials, a smaller amount of non-profitearning space would be required for storage. The use of fork trucks encourages .regular stacking to a height of 14 ft., in contrast with the haphazard stacking, over a greater floor area, commonly found in stores where manual methods are employed.
How can costs be lowered and output per hour be raised without extending factory space and increasing staff? This four-sided problem is familiar enough to post-war industry, particularly in the London area, where the expansion of premises is prohibited. It faces the H. J. Heinz Co., Ltd., in producing a wide range of foodstuffs at Harlesden, London, N.W.10, as well as at a subsidiary plant in Wigan, and is being solved largely with the aid of fork trucks.
Bonus schemes encourage sustained effort by workers, but they are not really effective unless accompanied by expeditious methods of handling and production. Ideally, of course, systems of dealing with raw materials and finished products should be perfected first, but post-war conditions call for rapid improvization and, as in the Heinz organization, human and mechanical problems must be tackled simultaneously The company had some experience of the operation of fork trucks before the war, but it was not until peace Greater flexibility in production has been achieved because supplies can quickly be brought to the point at which they are required, and rapid adjustments can be made in the production programme. The developing use of pallets also promises substantial savings in packing materials—one of the many fruitful avenues of economy which mechanical handling opens up.
The Heinz company now has 19 fork trucks-16 at Harlesden and three at Wigan—as well as six Ransomes platform trucks with stillages for general work and for carrying loads, such as meat, that cannot conveniently be handled on pallets. The fleet—almost as wide in its range of makes as the celebrated 57 Varieties which it handles—comprises two Yale li-ton electric fork trucks, originally supplied by the American Heinz organization; two Greenbat 1-ton electric machines; five B.E.V. electric 2-tonners; one Conveyancer petrol-electric; six ex-Army Clark petrol trucks: and three RansomeS. one of which is a new 2-tonner.
The trucks work continuously for 8141.1 hours a day and their batteries are exchanged during the luncheon break. From the stores, they carry tinplate to the canmaking department, raw materials to the manufacturing sections for canned and bottled products, bottles to the filling plant, and fibreboard cases to the packing sections, and from the labelling lines, the finished products to the warehouse and dispatch department.
Six fork trucks, as well as two spares, are controlled by the stores manager. Two are regularly employed in carrying bottles and barrels, two handle tinplate, cans, can-ends, solder and can-lining solution, and two are engaged in bringing up raw materials and general unloading. The platform trucks are also allotted to the stores.
Another fork truck is permanently in service in the can-making section, and six others, under the control of the warehouse manager, bring goods from the production lines to the stores and from the stores to the dispatch bay. The warehouse has one spare truck, •
Obsolete fork trucks are beingreplaced and four new Ransomes are on order. Only electric trucks work inside the factory buildings.
Pallets are used. in all unloading operations, although
not all materials arrive on them. The company's standard pallet 'measures 4 ft. by 3 ft. 4 ins. by 6 ins., and is made of l-in. timber. .These dimensions best suit the 28 different sizes of case which have to be used. Pallets are.estirnated.to have a life of six years and the annual maintenance cost is reckoned 165 per, cent. of the original cost. In fact, those at present in use by Heinz have already given sei'vice for that period and have cost less than 5 per cent. per annum of their purchase price to maintain. They are made of good Canadian
timber, which is no longer available; the new •pallets have had to be manufactured from English wood and may have a shorter life.
The use of pallets in delivering and handling crated bottles has materially reduced breakages. One pallet carries 16 wooden crates, but the surface area of 4 ft. by 3 ft. 4 ins. is a trifle large for its load. It will, however, exactly lit the fibreboard cases in which it is hoped ultimately to receive the bottles. These, in their cases, will be carried on pallets to the filling plant and, after filling, will be replaced in their cartons, which will be delivered, on pallets, to the warehouse. The work of returning the wooden cases from the filling section and bringing up cartons from the store will be eliminated, and the expense of crates will be saved The bottles are delivered from the maker's works, about five miles away, by articulated lorries. Directly a vehicle arrives with a load of bottles, the tractor is unhitched and coupled to a semi-trailer loaded with empty crates. While the lorry is returning the empties, the filled crates are being unloaded by fork truck at the Heinz works and a third semi-trailer is being loaded at the bottle factory. By employing three semi-trailers to one tractor, the round trip is completed in an hour and the tractor is never idle.
Tinplate in 1-ton Packs Tinplate for cans arrives by road in 1-ton bundles, wrapped in fibreboard, to which a single-faced pallet is strapped by steel strip. The package, which is valuable and, if not carefully handled, is susceptible to damage at the edges, measures. 2 ft. 2 ins. by 1 ft. 11 ins. by 9 ins. This concentrated load is easily transferred by fork truck from the vehicle to the store. Before mechanical handling was employed, the plate had to be delivered in 2-cwt. packs with a consequent multiplication of handling and unnecessary extravagance in wrapping materials.
Fork trucks having taken the drudgery out of unloading, the circular can-ends can be supplied in more economic units. In the past, they have been
delivered in slim cylindrical packs. Each contained 200 ends, weighed 5 lb. and was 15 ins. high. Because of their awkward shape, not more than two packs at a time could be handed down by a man on a lorry to another standing on the ground.
Now 72,000 ends, packed in 30 rectangular fibreboard cartons, are handled in one operation on a pallet supplied by the manufacturers.
Similarly, the use of fork trucks has enabled solder to be accepted in 1-ton lots on pallets, instead of in 14-lb. ingots. Lining solution for cans arrives in 45-gallon drums, of which four can be lifted on one pallet.
A careful study of the processes involved in delivering fibreboard cases from the store to the picking department has shown how unnecessary labour can be eliminated. Here, again, the fork truck is the key to the solution of the problem. At present the cartons are lifted by hand on to a trailer and are taken to the production department, where they are placed on the floor. Later, they are again picked up and placed in green-painted wooden bins mounted on castors, which are wheeled to the labelling lines. In future, the bins, the capacity of which is being doubled by fitting hinged extensions to the sides, are to be taken to the store for loading. Four of them, containing 1,000 cases, will be pinned together to form is cube, and the whole will be carried by a truck, specially equipped with extension forks, direct to the labelling lines. There, the bins will be unclipped and four individual trolleys will be available for. use.. This simple
c6
expedient will cut out two handlings and obviate the nuisance of cases lying on the TIOOr in the production department. Fork trucks feed the can-making department with a steady supply of metal. The sheets of tinplate, on a pallet, are plated in a slitter, which automatically raises the pallet to working height and cuts the metal to the correct size for the body of a can. The pieces of tinplate are then transferred by hand to the bodymaking machines and, after_ passing through several ingenious processes, the finished cans travel by overhead conveyors to the production department. The conveyor lines wind in and out and have bee, made purposely long so that should a hitch occur in the can-making department, there is still a large supply of cans "in transit" and production will not imn-iedi ately be affected. If the rate of delivery exceeds the requirements ot the production department, cans are by-passed down another runway and removed. They can later be fed back to the conveyor without the need for returning them to the beginning of the line.
In some other operations, overhead hoists, stillage trucks and roller conveyors are used
Finished Goods on Pallets Pallets again come into use in the handling of all finished goods. These are taken by fork truck to the outwards bay, where a central track for both road and rail vehicles runs between two loading banks. The gap is bridged by a removable structure. Part of the warehouse is set aside for goods for local distribution, and orders for individual traders are made up on pallets and taken by fork truck straight to the vehicle.
Similarly, products for distribution in the North are taken to another part of the warehouse and are transferred on pallets to contract vehicles, which provide a regular service. On the return journeys these vehicles bring goods from the Standish factory, which produces different foodstuffs from the plant at Harleiden. One set of pallets can be used for the two operations.
Although the Heinz concern is convinced there is great scope for the extension of mechanical handling by the use of fork trucks and pallets, it is conscious of the limitations of the system. A sum of money has been allocated to the purchase of new equipment, but fresh methods will not be introduced until they have proved their merit under scientific investigation. Appropriately applied and intensively used, mechanical handling appliances are able -to recover their capital .cost in a short time,