Quick, easy-clean discharge for cement tankers
Page 42
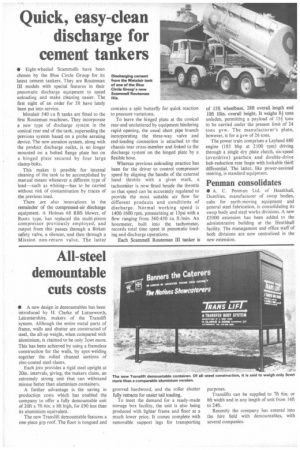
If you've noticed an error in this article please click here to report it so we can fix it.
• Eight-wheeled Scammells have been chosen by the Blue Circle Group for its latest cement tankers. They are Routeman III models with special features in their pneumatic discharge equipment to speed unloading and make cleaning easier. The first eight of an order for 58 have lately been put into service.
Metalair 540 cu ft tanks are fitted to the first Routeman machines. They incorporate a new type of discharge system in the conical rear end of the tank, superseding the previous system based on a probe aerating device. The new aeration system, along with the product discharge outlet, is no longer mounted on a bolted flange plate but on a hinged plate secured by four large clamp-bolts.
This makes it possible for internal cleaning of the tank to be accomplished by manual means whenever a different type of load—such as whiting—has to be carried without risk of contamination by traces of the previous load.
There are also innovations in the remainder of the compressed-air discharge equipment. A Holmes 68 RBS blower, of Roots type, has replaced the multi-piston compressor previously employed, and output from this passes through a Birkett safety valve, a silencer, and then through a Mission non-return valve. The latter contains a split butterfly for quick reaction to pressure variations.
To leave the hinged plate at the conical rear-end uncluttered by equipment hindering rapid opening, the usual short pipe branch incorporating the three-way valve and end-loading connection is attached to .the chassis rear cross-member and linked to the discharge system on the hinged plate by a flexible hose.
Whereas previous unloading practice has been for the driver to control compressor speed by aligning the handle of the external hand throttle with a given mark, a tachomiter is now fitted beside the throttle so that speed can be accurately regulated to provide the most suitable air flow for different products and conditions of discharge. Normal working speed is 1400-1600 rpm, pressurizing at 13psi with a flow ranging from 360-450 cu ft /min. An hourmeter, built into the tachometer, records total time spent in pneumatic loading and discharge operations.
Each Seammell Routeman Ill tanker is of 15ft wheelbase, 28ft overall length and 10ft 10in, overall height. It weighs 81 tons unladen, permitting a payload of 151 tons to be carried under the present limit of 24 tons gvw. The manufacturer's plate, however, is for a gvw of 26 tons.
The power train comprises a Leyland 680 engine (185 bhp at 2100 rpm) driving through a single dry plate clutch, six-speed (overdrive) gearbox and double-drive hub-reduction rear bogie with lockable third differential. The latter, like power-assisted steering, is standard equipment.
Penman consolidates
• A. C. Penman Ltd, of Heathhall, Dumfries, manufacturer of swop bodies, cabs for earth-moving equipment and general steel fabrication, is consolidating its swop body and steel works divisions. A new £5000 extension has been added to the administrative building at the Heathhall facility. The management and office staff of both divisions are now centralized in the new extension.