Aluminium Products in the Making
Page 48
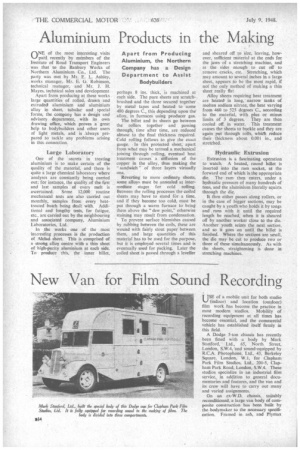
If you've noticed an error in this article please click here to report it so we can fix it.
Apart from Producing Aluminium, the Northern Company has a Design Department to Assist Bodybuilders
ONE of the most interesting visits paid recently by members of the Institute of Road Transport Engineers was that to the Banbury Works of Northern Aluminium Co., Ltd. The party was met by Mi. E. L. Ashley, works manager. Mr. E. U. Robinson, technical manager, and Mr. J. H. Mayes, technical sales and development
Apart from producing at these works large quantities of rolled, drawn and extruded aluminium and aluminium alloy in sheet, tubular and . special forms, the company has a design and advisory department, with its own drawing office, which proves a great help to bodybuilders and other users of light metals, and is .always prepared to tackle any problems arising in this connection.
Large Laboratory One of the secrets in treating aluminium is to make certain of the quality of the material, and there is quite a large chemical laboratory where analyses are constantly being carried out; for instance, the quality of the first and last samples of every melt is ascertained. Some 12,000 routine mechanical tests are also carried out monthly, samples from every heattreated batch being dealt with Additional and lengthy tests, for fatigue, etc., are carried out by the neighbouring and associated company, Aluminium Laboratories, Ltd.
In the works one of the most inwesting processes is the production of Alclad sheet. This is comprised of a strong alloy centre with a thin sheet of high-purity aluminium at each side. To produce this, the inner billet, perhaps 8 ins, thick, is machined at each side. The pure sheets are scratchbrushed and the three secured together by metal tapes and heated to some 480 degrees C., this depending upon the alloy, in furnaces using producer gas.
The billet and its sheets go between the rollers. together and passing through, time after time, are reduced almost to the final thickness required. Cold rolling follows to give he exact gauge. In this protected sheet; apart from what may be termed a mechanical joining through rolling, eventual heat treatment causes a diffusion of the copper in the alloy, thus making the "
sandwich" of three layers virtually One, Reverting to more ordinary sheets, some alloys must be annealed at intermediate stages for cold rolling. Between the rolling processes the coiled sheets may have to stand fOr a time, and if they become too cold, must be put through a warm furnace to bring them above the "dew point," otherwise staining may result from condensation. ' To prevent surface blemishes caused by rubbing between the coils, these are wound with fairly stout paper between them. and . large quantities of this material has to be used for the purpose, but it is employed several times and is eventually used for packing. Later the coiled sheet is passed through a leveller and sheared off to size, leaving, however, sufficient material at the ends for the jaws of a stretching machine, and at the sides enough to cut off to remove cracks, etc. Stretching, which may amount to several inches in a large sheet, appears to be the most rapid, if not the only method of making a thin sheet really flat
Alloy sheets requiring heat treatment are heated in long, narrow tanks of molten sodium nitrate, the heat varying from 460 to 525 degrees C., according to the matetial, with plus or minus limits of 3 degrees. They are then cooled off in water. This treatment causes the sheets to buckle and they are again Tint through rolls, whieh reduce their thickness about 0.001 in., and stretched.
Hydraulic Extrusion Extrusion is a fascinating operation to watch. A heated, round billet is inserted into the ram socket, at the forward end of which is the appropriate die. The ram then enters, under a hydraulic pressure of many hundreds of tons, and the aluminium literally squirts through the die,
It then either passes along rollers, or in the case of bigger sections, may be caught by a youth who holds it by tongs and runs with it until the required length be reached, when it is sheared off by another worker close to the die. Another youth seizes the next section, and so it goes on until the billet is finished. Where the sections are small, the die may be cut to produce two or three of these simultaneously. As with the sheets, straightening is done in stretching machines.