transatlantic bodybuilding
Page 53
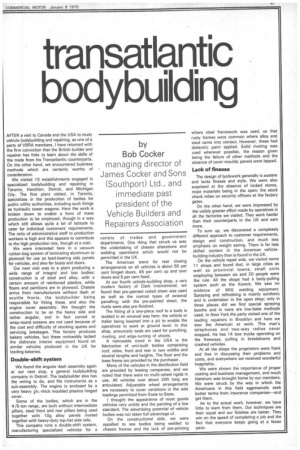
If you've noticed an error in this article please click here to report it so we can fix it.
AFTER a visit to Canada and the USA to study vehicle bodybuilding and repairing, as one of a party of VBRA members, I have returned with the firm conviction that the British builder and repairer has little to learn about the skills of the trade from his Transatlantic counterparts. On the other hand, we encountered business methods which are certainly worthy of consideration.
We visited 15 establishments engaged in specialized bodybuilding and repairing in Toronto, Hamilton, Detroit, and Michigan City. The first plant visited, in Toronto, specializes in the production of bodies for public utility authorities, including such things as hydraulic tower wagons. Here the work is broken down to enable a form of mass production to be employed, though in a way which still allows quite a lot of latitude to cater for individual customers' requirements. The ratio of administrative staff to production workers is high and this appears to contribute to the high production rate, though at a cost.
We were interested here in a vacuum rubber-bag system of laminating aluminium to plywood for use as load-bearing side panels for vehicles, and also for boats and doors.
Our next visit was to a plant producing a wide range of integral and box bodies; construction is of steel and alloy, with a certain amount of reinforced plastics, while floors and partitions are in plywood. Chassis arrive from manufacturers without dash or scuttle fronts, the bodybuilder being responsible for fitting these, and also the engine cover assembly. We thought the construction to be on the heavy side and rather angular, and in fact curved or wrap-round screens are not used because of the cost and difficulty of stocking spares and servicing breakages. This factory produces bakery vehicles, but these noticeably lacked the elaborate interior equipment found on similar vehicles produced in the UK for leading bakeries.
Double-shift system
We found the angular dash assembly again at our next stop, a general bodybuilding company in Detroit. The bodybuilder also has the wiring to do, and fits instruments as a sub-assembly. The engine is enclosed by a very heavy .in.-thick moulded plastics hinged cover.
Some of the bodies, which are in the 4 /5-ton range, are built without intermediate pillars, steel front and rear pillars being used together with lOg alloy panels riveted together with heavy-duty top-hat side rails.
This company runs a double-shift system, manufacturing specialized vehicles for a variety of trades and government departments. One thing that struck us was the undertaking of chassis alterations and welding operations which would not be permitted in the UK.
The American trend for rear closing arrangements on all vehicles is about 50 per cent hinged doors, 45 per cent up and over doors and 5 per cent fixed.
At our fourth vehicle-building shop, a very modern factory of Clark International, we found that pre-painted coiled sheet was used as well as the normal types of external panelling; with the pre-painted sheet, the rivets were also pre-finished.
The fitting of a one-piece roof to a body is tackled in an unusual way here, the vehicle or trailer being lowered into a pit to enable the operatives to work at ground level. In this shop, pneumatic tools are used for punching, riveting, and edge-turning of sheets.
A noticeable trend in the USA is the fabrication of unit-built bodies comprising roof, sides, front and rear in two widths and several lengths and heights. The floor and the base frame are provided by the purchaser.
Many of the vehicles in the distribution field are provided by leasing companies, and we noted that there were no multi-wheel rigids in use. All vehicles over about 20ft long are articulated. Adjustable wheel arrangements are necessary to cover variations in the axle loadings permitted from State to State.
I thought the appearance of most goods vehicles very untidy and the painting of a low standard. The advertising potential of vehicle bodies was not taken full advantage of.
On the constructional side, we were appalled to see bodies being welded to chassis frames and the lack of pre-priming where steel framework was used, so that rusty frames were common where alloy and steel came into contact. However, these had dielectric paint applied. Solid riveting was used wherever possible, the reason given being the failure of other methods and the absence of cover moulds; panels were lapped.
Lack of finesse
The design of bodywork generally is austere and lacks finesse and style. We were also surprised at the absence of locked stores, most materials being in the open; the stock check relies on security officers at the factory gates.
On the other hand, we were impressed by the visibly greater effort made by operatives in all the factories we visited. They work harder than their counterparts in the UK and earn more.
To sum up, we discovered a completely different approach to customer requirements, design and construction, and much less emphasis on weight saving. There is far less skilled content in the American vehiclebuilding industry than is found in the UK.
On the vehicle repair side, we visited some 11 shops and found that, in large cities as well as provincial towns, small units employing between six and 20 people were the rule. All the shops had a body-pulling system such as the Koreck. We saw no evidence of MIG welding equipment. Spraying and refinishing is mainly synthetic and is undertaken in the open shop; only in three places did we find special spraying booths and in none are low-bake methods used. In New York the party visited one of the leading repairers in Brooklyn and here we saw the American at work. This man's telephones and two-way radios never stopped. He has 14 tow trucks operating on the freeways, pulling in breakdowns and crashed vehicles.
At all the shops the proprietors were frank and free in discussing their problems and costs, and everywhere we received wonderful hospitality.
We were shown the importance of proper costing and business management, and much literature was brought home by our members. We were struck by the way in which the Americans in this field aggressively seek better terms from insurance companies—and get them.
As to the actual work, however, we have little to learn from them. Our techniques are their equal and our finishes are better. They win on the speed of completing a job and the fact that everyone keeps going at a faster pace.