Benchwise: power tool safeguards
Page 41
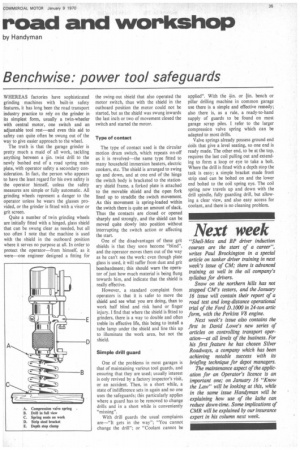
If you've noticed an error in this article please click here to report it so we can fix it.
WHEREAS factories have sophisticated grinding machines with built-in safety features, it has long been the road transport industry practice to rely on the grinder in its simplest form, usually a twin-wheeler with central motor, one switch and an adjustable tool rest—and even this aid to safety can quite often be swung out of the way to give easier approach to the wheel.
The truth is that the garage grinder is pretty much a maid of all work, tackling anything between a -kin. twist drill to the newly bushed end of a road spring main plate, with operator safety a secondary consideration. In fact, the person who appears to have the least regard for his own safety is the operator himself, unless the safety measures are simple or fully automatic. All grinding wheels represent a danger to the operator unless he wears the glasses provided, or the grinder is fitted with a visor or grit screen.
Quite a number of twin grinding wheels are initially fitted with a hinged, glass shield that can be swung clear as needed, but all too often I note that the machine is used with the shield in the outboard position where it serves no purpose at all. In order to protect the operator—from himself, as it were—one engineer designed a fitting for the swing-out shield that also operated the motor switch, thus with the shield in the outboard position the motor could not be started, but as the shield was swung inwards the last inch or two of movement closed the switch and started the motor.
Type of contact
The type of contact used is the circular motion drum switch, which repeats on-off as it is revolved—the same type fitted to many household immersion heaters, electric cookers. etc. The shield is arranged to swing up and down, and at one end of the hinge the switch body is bracketed to the stationary shield frame, a forked plate is attached to the movable shield and the open fork lined up to straddle the switch movement. As this movement is spring-loaded within the switch there is quite an amount of slack. Thus the contacts are closed or opened sharply and strongly, and the shield can be moved quite slowly into position without interrupting the switch action or affecting the start.
One of the disadvantages of these grit shields is that they soon become "blind", and the operator moves them out of the way as he can't see the work: even though plate glass is used, it will suffer from dust and grit bombardment; this should warn the operator of just how much material is being flung towards him, and indicate that the shield is really effective.
However, a standard complaint from operators is that it is safer to move the shield and see what you are doing, than to work half blind and risk hand or finger injury. I find that where the shield is fitted to grinders, there is a way to double and often treble its effective life, this being to install a tube lamp under the shield and line this up to illuminate the work area. but not the shield.
Simple drill guard
One of the problems in most garages is that of maintaining various tool guards. and ensuring that they are used; usually interest is only revived by a factory inspector's visit, or an accident. Then, in a short while, a state of indifference sets in again and no one uses the safeguards: this particularly applies where a guard has to be removed to change drills and in a short while is conveniently "missing-.
With drill guards the usual complaints are—"It gets in the way"; "You cannot change the drill"; or "Coolant cannot be
applied-. With the 4in. or -lin. bench or pillar drilling machine in common garage use there is a simple and effective remedy; also there is, as a rule, a ready-to-hand supply of guards to be found on most garage scrap piles. I refer to the larger compression valve spring which can be adapted to most drills.
Valve springs already possess ground end coils that give a level seating, so one end is ready made. The other end, to be at the top, requires the last coil pulling out and extending to form a loop or eye to take a bolt. Where the drill is fitted with a depth stop the task is easy; a simple bracket made frorrl strip steel can be bolted on and the lower end bolted to the coil spring eye. The coil spring now travels up and down with the drill spindle, fully guarding drill, but allowing a clear view, and also easy access for coolant, and there is no cleaning problem.