Brighter future for electric's?
Page 52
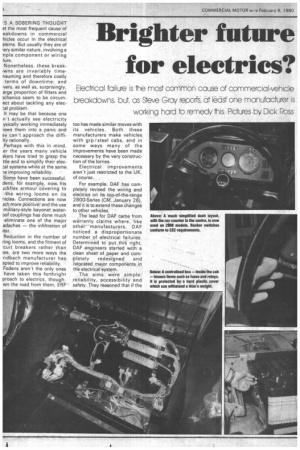
Page 53
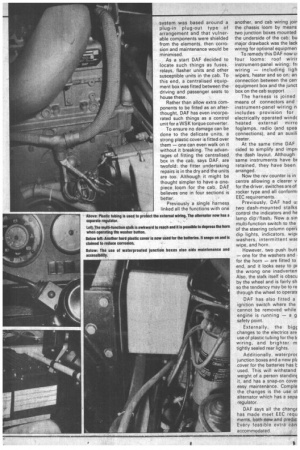
If you've noticed an error in this article please click here to report it so we can fix it.
Electrical failure is e most common cause of commercial-vehicle breakdowns, but as Steve Gray reports, cr least one manufacturer is working hero to remecy mis. Pictures by Dick Ross
'S A SOBERING THOUGHT at the most frequent cause of eakdowns in commercial hides occur in the electrical stems. But usually they are of fery similar nature, involving a rple component or wiring lure.
Nonetheless, these breakivyns are invariably timensuming and therefore costly terms of downtime; and vers, as well as, surprisingly, arge proportion of fitters and 3chanics seem to be circumect about tackling any eleca1 problem.
It may be that because one n't actually see electricity ysically working immediately -ows them into a panic and ey can't approach the diffiIty rationally.
Perhaps with this in mind, er the years many vehicle 3kers have tried to grasp the tile and to simplify their elecnl systems while at the same le improving reliability.
Some have been successful. dens, for example, now fits Jckflex armour covering to the wiring looms on its hides. Connections are now ich more positive, and the use military-style bayonet waterDof couplings has done much eliminate one of the major adaches — the infiltration of iter.
Reduction in the number of ring looms, and the fitment of .cuit breakers rather than ;es, are two more ways the ndbach manufacturer has apted to improve reliability. Fodens aren't the only ones have taken this forthright proach to electrics, though. wn the road from them, ERF too has made similar moves with its vehicles. Both these manufacturers make vehicles. with grp /steel cabs, and in some ways many of the improvements have been made necessary by the very construction of the lorries.
Electrical improvements aren't just restricted to the UK, of course.
For example, DAF has completely revised the wiring and electrics on its top-of-the-range 2800-Series (CM, January 26), and it is to extend these changes to other vehicles.
The lead for DAF came from warranty claims where, like other. manufacturers, DAF noticed a disproportionate number of electrical failures. Determined to put this right, DAF engineers started with a clean sheet of paper and com
pletely redesigned and relocated major components in the electrical system.
The aims were simple: reliability, accessibility and safety. They reasoned that if the system was based around a plug-in plug-out type of arrangement and that vulnerable components were shielded from the elements, then corrosion and maintenance would be minimised.
As a start DAF decided to locate such things as fuses, relays, flasher units and other susceptible units in the cab. To this end, a centralised equipment box was fitted between the driving and passenger seats to house these.
Rather than allow extra components to be fitted as an afterthought. DAF has even incorporated such things as a control unit for a WSK torque converter.
To ensure no damage can be done to the delicate units, a strong plastic cover is fitted over them — one can even walk on it without it breaking. The advantages of fitting the centralised box in the cab, says DAF, are twofold: the fitter undertaking repairs is in the dry and the units are too. Although it might be thought simpler to have a onepiece loom for the cab, DAF believes one in four sections is better.
Previously a single harness linked all the functions with one another, and cab wiring joir the chassis loom by means two junction boxes mounted the underside of the cab; bu major drawback was the lack wiring for optional equipmen To remedy this DAF now u! four looms: roof wirir
instrument-panel wiring; fr.( wiring — including ligh wipers, heater and so on; an connection between the cen. equipment box and the junct box on the cab support.
The harness is joined means of connectors and • instrument-panel wiring n includes provision for electrically operated windc heated external mirro foglamps, radio (and spea connections), and an auxili heater.
At the same time DAF cided to simplify and impri the dash layout. Although same instruments have bc retained, they have been arranged.
Now the rev counter is in centre allowing a clearer v for the driver, switches are of rocker type and all conform: EEC requirements.
Previously, DAF had Li! two dash-mounted stalks control the indicators and he lamp dip/flash. Now a sin multi-function switch to the of the steering column operE dip lights, indicators, wip( washers, intermittent waE wipe, and horn.
However, two push butt — one for the washers and for the horn — are fitted to end, and it looks easy to pr the wrong one inadverten Also, the stalk itself is obscu by the wheel and is fairly sh so the tendency may be to re through the wheel to operatE DAF has also fitted a ignition switch where the cannot be removed while engine is running — a g safety point.
Externally, the bigc changes to the electrics are use of plastic tubing for the k wiring, and brighter m tightly sealed rear lights.
Additionally, waterproc junction boxes and a new plE cover for the batteries has used. This will withstand weight of a person standinc it, and has a snap-on cover easy maintenance. Comple the changes is the use oi alternator which has a sepa regulator.
DAF says all the changc has made meet EEC requ ments, both now and predic Every feasible extra can accommodated.