ARTICULATIOP
Page 60
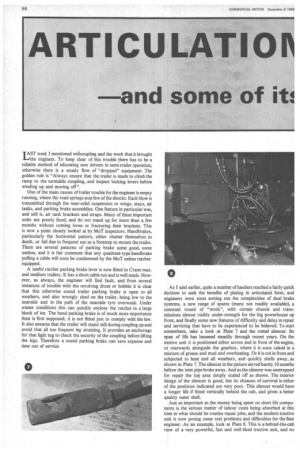
Page 61
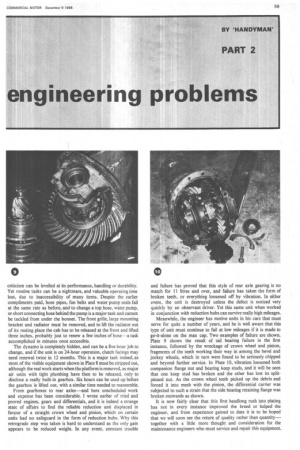
If you've noticed an error in this article please click here to report it so we can fix it.
and some of engineering problems
TAST week I mentioned migcoupling and the work that it brought
the engineer. To keep clear of this trouble there has to be a reliable method of educating new drivers in semi-trailer operation, otherwise there is a steady flow of "dropped" equipment. The golden rule is "Always ensure that the trailer is made to climb the ramp to the turntable coupling, and inspect locking levers before winding up and moving off".
One of the main causes of trailer trouble for the engineer is empty running, where the road springs stop few of the shocks. Each blow is transmitted through the near-solid suspension to wings, stays, air tanks, and parking brake assemblies. One feature in particular was, and still is, air tank brackets and straps. Many of these important units are poorly fixed, and do not stand up for more than a few months without coming loose or fracturing their brackets. This is now a point closely looked at by MoT inspectors. Handbrakes, particularly the horizontal pattern, either chatter themselves to death, or fail due to frequent use as a footstep to mount the trailer. There are several patterns of parking brake some good, some useless, and it is fair comment that any quadrant-type handbrake pulling a cable will soon be condemned by the MoT unless ratchet equipped.
A useful ratchet parking brake lever is now fitted to Crane max. and medium trailers. It has a short cable run and is well made. However, as always, the engineer will find fault, and from several instances of trouble with the revolving drum or bobbin it is clear that this otherwise sound trailer parking brake is open to all weathers, and also wrongly sited on the trailer, being low to the nearside and in the path of the nearside tyre overwash. Under winter conditions this can quickly enclose the ratchet in a large block of ice. The hand parking brake is of much more importance than is first supposed; it is not fitted just to comply with the law. It also ensures that the trailer will stand still during coupling up and avoid that all too frequent leg straining. It provides an anchorage for that light tug to check the security of the coupling before lifting the legs. Therefore a sound parking brake can save expense and time out of service. As I said earlier, quite a number of hauliers reached a fairly quick decision to seek the benefits of plating in articulated form, and engineers were soon sorting out the complexities of dual brake systems, a new range of spares (many not readily available), a constant round of "mods", with certain chassis and transmissions almost visibly under-strength for the big powerhouse up front, and finally some new features of difficulty and delay in repair and servicing that have to be experienced to be believed. To start somewhere, take a look at Plate 7 and the rotted silencer. Its span of life has lessened steadily through recent years. On the motive unit it is positioned either across and in front of the engine, or rearwards alongside the gearbox, where it is soon caked in a mixture of grease and mud and overheating. Or it is out in front and subjected to heat and all weathers, and quickly shells away, as shown in Plate 7. The silencer in the picture served barely 10 months before the inlet pipe broke away. And as the silencer was unstrapped for repair the top area simply scaled off as shown. The interior design of the silencer is good, but its chances of survival in either of the positions indicated are very poor. This silencer would have a longer life if fitted vertically behind the cab, and given a better quality outer shell.
Just as important as the money being spent on short life components is the serious matter of labour costs being absorbed at this time in what should be routine repair jobs, and the modern tractive unit is now posing some real problems and difficulties for the fleet engineer. As an example, look at Plate 8. This is a behind-the-cab view of a very powerful, fast and well-liked tractive unit, and no criticism can be levelled at its performance, handling or durability. Yet routine tasks can be a nightmare, and valuable operating time lost, due to inaccessibility of many items. Despite the earlier compliments paid, hose pipes, fan belts and water pump seals fail at the same rate as before, and to change a top hose, water pump, or short connecting hose behind the pump is a major task and cannot be tackled from under the bonnet. The front grille, large mounting bracket and radiator must be removed, and to lift the radiator out of its resting place the cab has to be released at the front and lifted three inches, probably just to renew a few inches of hose—a task accomplished in minutes once accessible.
The dynamo is completely hidden, and can be a five-hour job to change, and if the unit is on 24-hour operation, clutch facings may need renewal twice in 12 months. This is a major task indeed, as most of the visible equipment shown in Plate 8 must be stripped out, although the real work starts when the platform is removed, as major air units with tight plumbing have then to be released, only to disclose a really built-in gearbox. Six hours can be used up before the gearbox is lifted out, with a similar time needed to reassemble.
From gearboxes to rear axles—and here unscheduled work and expense has been considerable. I wrote earlier of tried and proved engines, gears and differentials, and it is indeed a strange state of affairs to find the reliable reduction unit displaced in favour of a straight crown wheel and pinion, which on certain units had no safeguard in the form of reduction hubs. Why this retrograde step was taken is hard to understand as the only gain appears to be reduced weight. In any event, constant trouble
and failure has proved that this style of rear axle gearing is no match for 11 litres and over, and failure has taken the form of broken teeth, or everything loosened off by vibration. In either event, the unit is destroyed unless the defect is noticed very quickly by an observant driver. Yet this same unit when worked in conjunction with reduction hubs can survive really high mileages.
Meanwhile, the engineer has motive units in his care that must serve for quite a number of years, and he is well aware that this type of unit must continue to fail at low mileages if it is made to go-it-alone on the max cap. Two examples of failure are shown. Plate 9 shows the result of tail bearing failure in the first instance, followed by the wreckage of crown wheel and pinion, fragments of the teeth working their way in among the bevel and jockey wheels, which in turn were found to be seriously chipped and beyond further service. In Plate 10, vibration loosened both companion flange nut and bearing keep studs, and it will be seen that one keep stud has broken and the other has lost its splitpinned nut. As the crown wheel teeth picked up the debris and forced it into mesh with the pinion, the differential carrier was subjected to such a strain that the side bearing retaining flange was broken outwards as shown.
It is now fairly clear that this first headlong rush into plating has not in every instance improved the breed or helped the engineer, and from experience gained to date it is to be hoped that we will soon see the return of quality rather than quantity— together with a little more thought and consideration for the maintenance engineers who must service and repair this equipment.