Know-how 4 slack rope tell-tale
Page 42
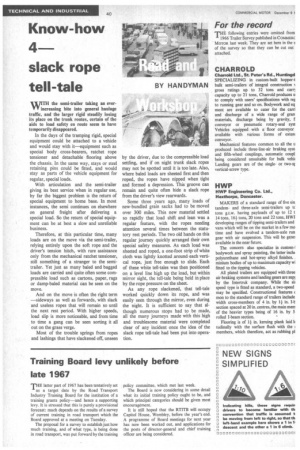
If you've noticed an error in this article please click here to report it so we can fix it.
the semi-trailer taking an ever increasing bite into general haulage traffic, and the larger rigid steadily losing its place on the trunk routes, certain of the aids to load safety en route seem to have temporarily disappeared.
In the days of the tramping rigid, special equipment could be attached to a vehicle and would stay with it—equipment such as special body cross-bearers, ratchet rope tensioner and detachable flooring above the chassis. In the same way, stays or steel retaining pins could be fitted, and would stay as parts of the vehicle equipment for regular, special loads.
With articulation and the semi-trailer giving its best service when in regular use, by far the biggest problem is the return of special equipment to home base. In most instances, the semi continues on elsewhere on general freight after delivering a special load. So the return of special equipment can be at best a slow and unreliable business.
Therefore, at this particular time, many loads are on the move via the semi-trailer, relying entirely upon the soft rope and the driver's tension hitch, with rare assistance only from the mechanical ratchet tensioner, still something of a stranger to the semitrailer. Yet just as many baled and bagged loads are carried and quite often some compressible load such as cartons, paper, rags or damp-baled material can be seen on the move.
And on the move is often the right term —sideways as well as forwards, with slack and useless ropes that will remain so until the next rest period. With higher speeds, load slip is more noticeable, and from time to time a gang can be seen sorting it all out on the grass verge.
Most of the trouble springs from ropes and lashings that have slackened off, unseen by the driver, due to the compressible load settling, and if on night trunk slack ropes may not be spotted until it is too late. Also, where baled loads are sheeted first and then roped, the ropes have nipped when tight and formed a depression. This groove can remain and quite often hide a slack rope from the driver's view rearwards.
Some three years ago, many loads of new-bundled grain sacks had to be moved over 300 miles. This new material settled so rapidly that load shift and lean was a regular feature, with the ropes needing attention several times between the statutory rest periods. The two old hands on this regular journey quickly arranged their own special safety measures. As each load was sheeted and roped, a one-foot strip of white cloth was lightly knotted around each vertical rope, just free enough to slide. Each of these white tell-tales was then positioned on a level line high up the load, but within mirror sight, the tell-tale being held in place by the rope pressure on the sheet.
As any rope slackened, that tell-tale worked quickly down its rope, and was easily seen through the mirror, even during the night. It is sufficient to say that although numerous stops had to be made, all the many journeys made with this high and troublesome material were completed clear of any incident once the idea of the slack rope tell-tale had been put into operation.
For the record
THE following entries were omitted from
1966 Trailer Survey published in COMMER( MOTOR last week. They are set here in the s of the survey so that they can be cut out attached.
CHARROLD
Charrold Ltd., St. Peter's Rd., Huntingd SPECIALIZING in custom-built hopper-I bulk semi-trailers of integral construction gross ratings up to 32 tons and cam capacity up to 21 tons, Charrold produces u to comply with users' specifications with reE to running gear and so on. Bodywork and eq ment are available to cater for the care and discharge of a wide range of gran materials, discharge being by gravity, f conveyor or pneumatic rotary-seal sysi Vehicles equipped with a floor conveyor available with various forms of exterr conveyor.
Mechanical features common to all the u produced include three-fine-air braking syst and fifth-wheel couplings, automatic coupl being considered unsuitable for bulk vehii Landing gears are of the singleor two-sr vertical-screw type.
HWP
HWP Engineering Co. Ltd., Hexthorpe, Doncaster.
MAKERS of a standard range of five sin tandemand three-axle semi-trailers up tt tons g.t.w. having payloads of up to 12 t 14 tons, 16+ tons, 20 tons and 22 tons, HWE developing ranges of tipping semi-trailers and vans which will be on the market in a few mo time and have evolved a tandem-axle run gear with air suspension. This will be gene available in the near future.
The concern also specialize in custom-1 bodywork and spray painting, the latter inclu polyurethane and hot-spray alkyd finishes. minium bodies of up to maximum capacity wi fitted to the tipping vehicles.
All plated trailers are equipped with three air-braking systems and landing gears are sup] by the Intertruk company. While the sii speed type is fitted as standard, a two-speed may be specified. Constructional features r mon to the standard range of trailers include width cross-members of 4 in. by 1+ in. I-I section spaced at 20 in. centres, the main men: of the heavier types being of 16 in. by 5 rolled I-beam section.
Flooring is of 1+ in. keruing plank laid Ii tudinally with the surface flush with the 1 members, which therefore, act as rubbing pl