40-seater Body Knocks Down to 350 Cubic Ft.
Page 50
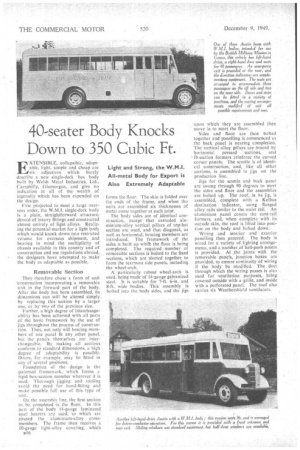
Page 51
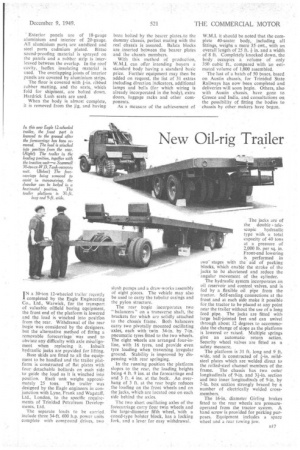
If you've noticed an error in this article please click here to report it so we can fix it.
Light and Strong, the W,M.I. All-metal Body for Export is Also Extremely Adaptable
F, 4XTENS1BLE, collapsible, adaptable, light, simple and cheap are
six adjectives which barely describe a new single-deck bus body built by Welsh Metal Industries, Ltd., Caerphilly, Glamorgan, and give no indication at all of the wealth of ingenuity which has been expended on the design. .
First .projected to meet a large overseas order, the W.M.I. single-deck body is a plain, -straightforward structure,' devoid of luxury fittings and constructed almost entirely of light alloys. Realizing the potential market for a light body which would knock down into restricted volume for overseas shipment, and bearing in mind the multiplicity of chassis available in this country and of construction and use regulations abroad, the designers have attempted to make the body as adaptable as possible. ,
Removable Section
They therefore chose a form of unit 'construction incorporating a removable unit in the forward part of the body. After the body has been assembled, its dimensions can stilt be altered simply by replacing this section by a larger one, or by two of the previous size.
Further, a high degree of interchangeability has been achieved with all parts of the basic framework by the use of jigs throughout the process of construction. Thus, not only will bracing members of one panel fit any other panel, but the panels themselves are interchangeable. By making all sections conform to standard dimensions, a high degree of adaptability is possible. Doors, for example, may be fitted in any of several positions.
Foundation of the design is the patented framework, which forms a rigid box-section member wherever it is used. Thorough jigging and tooling avoid the need for hand-fitting and make possible full use of this type of unit.
On the assembly line, the first section to. he completed .is the floor. In this part of the body 14-gauge laminated steel bearers are used. to which arc riveted the aluminium-alloy crossmembers. The frame then receives a 10-gauge light-alloy covering, which B16 forms the floor. The skin is folded over the ends of the frame, and when the units are assembled six thicknesses of metal come together at each joint.
The body sides are of identical construction, except that extruded aluminium-alloy vertical pillars of top-hat section are used, and that diagonal, as well as horizontal, bracing members are introduced. The framework of the sides is built up whir the floor is being completed. The required number of removable sections is bolted to the fixed sections, which are riveted together to form the rearmost side panels, including the wheel-arch.
A particularly robust wheel-arch is used, being made of 14-gauge galvanized steel. It is suitable for 7-ft. 6-in. and 8-ft. wide bodies. This assembly is bolted into the body sides, and the jigs upon which they are assembled then move in to meet the floor.
Sides and floor are then bolted together and panelling is commenced as the back panel is nearing completion. The vertical alloy pillars are braced by horizontal pressed sections, and 1)-section formers reinforce the curved corner panels. The scuttle is of identical construction, and, like all other sections, is assembled in jigs on the production line.
Jigs for the scuttle and back panel are swung through 90 degrees to meet the sides and floor and the assemblies are bolted up. The roof, in its jig, is assembled, complete with a Kelbus destination indicator, using flanged alloy rails similar to the waist rail. An aluminium panel covers the cant-rail formers, and, when complete with its outside skin, the roof is lifted into position on the body and bolted down.
Wiring and interior and exterior panelling then proceed. The body is wired for a variety of lighting arrangements, and a number of bell-push points is provided. At the joints with the removable panels, junction boxes are provided, to ensure continuity of wiring if the body be modified. The duct through which the wiring passes is also used for ventilation purposes, being covered outside with a grille, and inside with a perforated panel. The roof also carries six Weathersbietcl ventilators. • Exterior panels are of 18-gauge aluminium and interior of 20-gauge. All aluminium parts are anodized and steel parts cadmium plated. Bittac sound-proofing material is sprayed on the panels and a rubber strip is interleaved between the overlap, in the roof cavity, Isotlex insulating material is used. The overlapping joints of interior panels are covered by aluminium strips.
The floor is covered with fin, ribbed rubber matting, and the seats,, which fold for shipment, are bolted down. liardrick Lush seats are used.
When the body is almost complete, it is removed from the jig, and having
been bolted by the bearer plates,.to the dummy chassis, perfect mating with the real chassis is assured. Balata blocks are inserted between the bearer plates and the chassis members.
With this method of production, W.M.I. can offer intending buyers a standard body having a standard basic price. Further equipment may then be added on request, the list of 31 extras including direction indicators, additional lamps and bells (for which wiring is already incorporated in the body), extra doors, luggage racks and other components.
As a measure of the achievement of W.M.I. it should be noted that the complete 40-seater body, including all fittings, weighs a mere 35 cwt., with art overall length of 25 ft. in. and a width of 8 ft, Completely knocked down, the body occupies a volume of only 350 cubic, ft., compared with an estimated volume of 1,800 assembled.
The last of a batch of 50 buses, based on Austin chassis, for Trinidad State Railways has now been completed and deliveries will soon begin. Others, also with Austin chassis, have gone to Greece and India, and consultations on the possibility of fitting the bodies to chassis by other makers have begun.