MAKING MATERIALS MATTER
Page 54
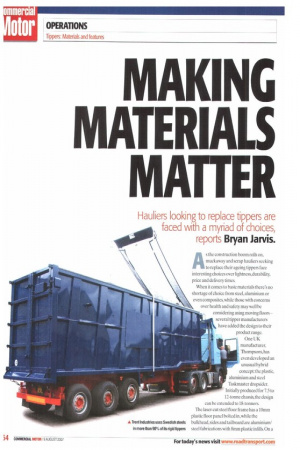
Page 55
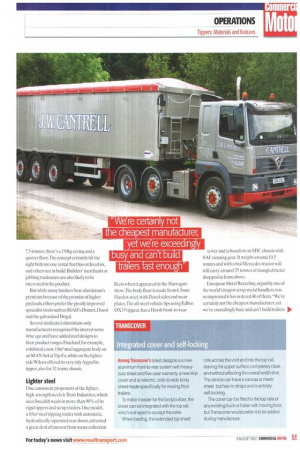
Page 56
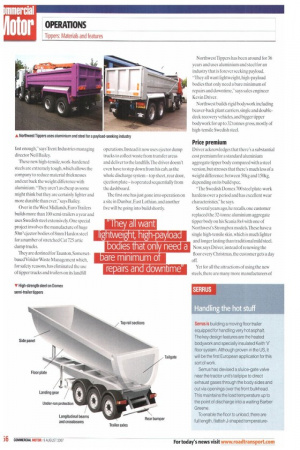
Page 57
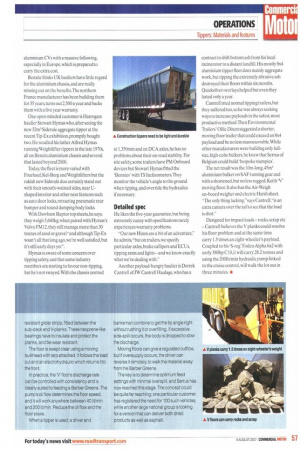
If you've noticed an error in this article please click here to report it so we can fix it.
Hauliers looking to replace tippers are faced with a myriad of choices,
reports Bryan Jarvis.
As the construction boom rolls on, muckaway and scrap hauliers seeking to replace their ageing tippers face interesting choices over lightness, durability, price and delivery times.
When it comes to basic materials there's no shortage of choice from steel, aluminium or even composites, while those with concerns over health and safety may well be considering using moving floors — several tipper manufacturers have added the design to their product range.
\ One UK manufacturer. Thompsons, has even developed an unusual hybrid concept: the plastic, aluminium and steel Taskmaster dropsider. Initially produced for 7.5 to 12-tonne chassis, the design can be extended to 18-tonners.
The laser-cut steel floor frame has a lOmm plastic floor panel bolted in, while the A Trent Industries uses Swedish steels bulkhead, sides and tailboard are aluminium/ in more than 90% of its rigid tippers steel fabrications with 8mm plastic infills. On a 7.5-tonner, there's a 150kg saving and a quieter floor.The concept certainly hit the right buttons: one rental fleet has ordered six, and others are in build. Builders' merchants or jobbing tradesmen are also likely to be interested in the product.
But while many hauliers bear aluminium's premium because of the promise of higher payloads, others prefer the greatly improved specialist steels such as SSAB's Domex,Docol and the galvanised Dogal.
Several dedicated aluminium-only manufacturers recognised the interest some time ago and have added steel designs to their product ranges. Fruehauf, for example, exhibited a new 15m3steel aggregate body on an MAN 8x4 at Tip-Ex,while on the lighter side Wilcox offered its very tidy Aggrelite tipper, also for 32-tonne chassis.
Lighter steel One consistent proponent of the lighter, high-strength steels is Trent Industries, which uses Swedish steels in more than 90% of its rigid tippers and scrap trailers. One model, a 65m3 steel tipping trailer with automatic, hydraulically-operated rear doors, attracted a great deal of interest from waste collection fleets when it appeared at the Harrogate show. The body floor is made from 6.5mm Hardox steel, with Docol sides and wear plates.The all-steel vehicle tips using Edbro DX19 tipgear, has a Harsh front-to-rear cover and is based on an SDC chassis with SAF running gear. It weighs around 10.5 tonnes and with a 6x4 Mercedes tractor will still carry around 25 tonnes or mangled metal dropped in from above.
European Metal Recycling, arguably one of the world's largest scrap-metal handlers, was so impressed it has ordered 40 of them,"We're certainly not the cheapest manufacturer, yet we're exceedingly busy and can't build trailers fast enough:. •Li■ s.lrent Industries managing director Neil Bailey.
These new high-tensile, work-hardened steels are extremely tough, which allows the company to reduce material thicknesses and cut back the weight difference with aluminium. "They aren't as cheap as some might think but they are certainly lighter and more durable than ever," says Bailey.
Over in the West Midlands, EuroTrailers builds more than 100 semi-trailers a year and uses Swedish steel extensively. One special project involves the manufacture of huge 50m3 ejectorbodies of 8mm Hardox steel for a number of stretched Cat 725 artic dump trucks.
They are destined for Taunton,Somersetbased Viridor Waste Management which, for safety reasons, has eliminated the use of tipper trucks and trailers on its landfill operations. Instead it now uses ejector dump trucks to collect waste from transfer areas and deliver to the landfills.The driver doesn't even have to step down from his cab, as the whole discharge system— top sheet, rear door, ejection plate — is operated sequentially from the dashboard.
The first one has j ust gone into operation on a site in Dunbar, East Lothian. and another five will be going into build shortly. Northwest Tippers has been around for 36 years and uses aluminium and steel for an industry that is forever seeking payload. They all want lightweight, high-payload bodies that only need a bare minimum of repairs and downtime," says sales engineer Kevin Driver.
Northwest builds rigid bodywork including beaver-back plant carriers, single and doubledeck recovery vehicles, and bigger tipper bodywork for up to 32 tonnes gross,mostly of high-tensile Swedish steel.
Price premium Driver acknowledges that there's a substantial cost premium for a standard aluminium aggregate tipper body compared with a steel version, but stresses that there's much less of a weight difference: between 50kg and 150kg, depending on its build spec.
"The Swedish Domex 700 steel plate-work hardens over a period and has excellent wear characteristics," he says.
Several years ago, he recalls, one customer replaced the 32-tonne aluminium aggregate tipper body on his Scania 8x4 with one of Northwest's Strongbox models.These have a single high-tensile skin, which is much lighter and longer lasting than traditional mild steel. Now, says Driver, instead of renewing the floor every Christmas, the customer gets a day off.
Yet for all the attractions of using the new steels, there are many more manufacturers of aluminium CVs with a massive following, especially in Europe, which is prepared to carry the extra cost.
Benalu thinks UK hauliers have little regard for the aluminium chassis, and are really missing out on the benefits.The northern France manufacturer has been building them for 35 years, turns out 2,500 a year and backs them with a five year warranty.
One open-minded customer is Harrogate haulier Stewart Hymas who, after seeing the new 32m3Siderale aggregate tipper at the recent Tip-Ex exhibition, promptly bought two. He recalled his father Alfred Hymas running Weightlifter tippers in the late 1970s, all on Benalu aluminium chassis and several that lasted beyond 2000.
Today, the fleet is more varied with Fruehauf,Kel-Berg and Weightlifters but the rakish new Siderale duo certainly stand out with their smooth-waisted sides, near Ushaped interior and other neat features such as auto door locks, retracting pneumatic rear bumper and sound damping body locks.
With Dawbarn Raptor top sheets, he says, they weigh 5,640kg; when paired with Hymas's Volvo FM12, they still manage more than 30 tonnes of sand or gravel and althoughTip-Ex wasn't all that long ago, we're well satisfied.but it's still early days yet".
Hymas is aware of some concern over tipping safety, and that some industry members are starting to favour non-tipping, but he not swayed. With the chassis centred at 1,350mm and on DCA axles, he has no problems about their on-road stability. For site safety, some trailers have PM Onboard devices but Stewart Hymas fitted the `Bennies' with TS Inclinometers.They monitor the vehicle's angle to the ground when tipping, and override the hydraulics if necessary.
Detailed spec
He likes the five-year guarantee, but being extremely canny with specifications rarely experiences warranty problems.
"Our new Hinos are a bit of an adventure,he admits,"but on trailers, we specify particular axles, brake callipers and ECUs, tipping rams and lights and we know exactly what we're dealing with."
Another payload-hungry haulier is Derrek Cantrell of JW Cantrell Haulage, who has a contract to shift bottom ash from his local incinerator to a distant landfill. His mostly 8x4 aluminium tipper fleet does mainly aggregate work, but tipping the extremely abrasive ash destroyed their floors within six months. Quicksilver overlays helped but even they lasted only a year.
Cantrell tried normal tipping trailers, but they suffered too, so he was always seeking ways to increase payloads in the safest, most productive method.Then Environmental Trailers' 011ie Dixon suggested a shorter, moving floor trailer that could exceed an 8x4 payload and be no less manoeuvrable.While other manufacturers were building only fullsize, high-cube bulkers, he knew that Serrus of Belgium could build 'bespoke stumpies'.
The net result was the lOrn-long, 45m3 aluminium bulker on SAF running gear and with a shortened, but no less rugged, Keith 'V' moving floor. It also has the Air-Weigh on-board weigher and electric Harsh sheet. "The only thing lacking," says Cantrell,-is an extra camera over the tail to see that the load is shot."
Designed for impact loads rocks, scrap etc Cantrell believes the V planks could resolve his floor problem and at the same time carry 1.5 times an eight-wheeler's payload. Coupled to his 'S-reg' Foden Alpha 6x2 with early 380hp C10, it will carry 28.2 tonnes and using the 2001itimin hydraulic pump linked to the cruise control, will walk the lot out in three minutes. •