2. The swop-body concept
Page 78
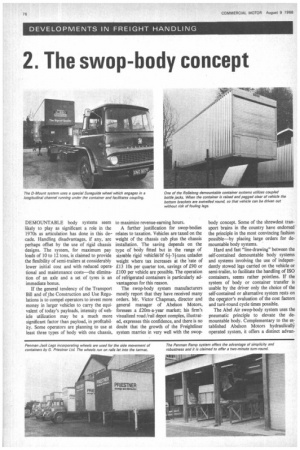
Page 79

Page 80
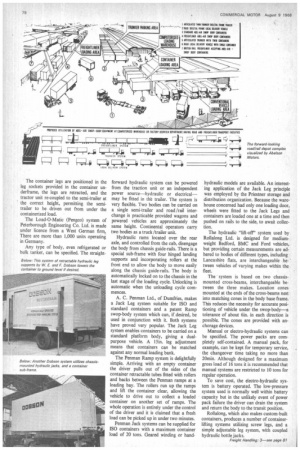
If you've noticed an error in this article please click here to report it so we can fix it.
DEMOUNTABLE body systems seem likely to play as significant a role in the 1970s as articulation has done in this decade. Handling disadvantages, if any, are perhaps offset by the use of rigid chassis designs. The system, for maximum pay loads of 10 to 12 tons, is claimed to provide the flexibility of semi-trailers at considerably lower initial cost and with reduced operational and maintenance costs—the elimination of an axle and a set of tyres is an immediate bonus.
If the general tendency of the Transport Bill and of the Construction and Use Regulations is to compel operators to invest more money in larger vehicles to carry the equivalent of today's payloads, intensity of vehicle utilization may be a much more significant factor than payload, in profitability. Some operators are planning to use at least three types of body with one chassis. to maximize revenue-earning hours.
A further justification for swop-bodies relates to taxation. Vehicles are taxed on the weight of the chassis cab plus the chassis installation. The saving depends on the type of body fitted but in the range of sizeable rigid vehicles-Of 6+-7+tons unladen weight where tax increases at the -rate of £13 lOs per quarter ton, savings of £90 or £100 per vehicle are possible. The operation of refrigerated containers is particularly advantageous for this reason.
The swop-body system manufacturers mostly report that they have received many orders. Mr. Victor Chapman, director and general manager of Abelson Motors, foresees a £20m-a-year market: his firm's visualized road/rail depot complex, illustrated, expresses this confidence, and there is no doubt that the growth of the Freightliner system marries in very well with the swop
body concept. Some of the shrewdest transport brains in the country have endorsed the principle in the most convincing fashion possible—by placing large orders for demountable body systems.
Hard and fast "line-drawing" between the self-contained demountable body systems and systems involving the use of independently stowed legs carried on the vehicle or semi-trailer, to facilitate the handling of ISO containers, seems rather pointless. If the system of body or container transfer is usable by the driver only the choice of the self-contained or alternative system rests on the opervator's evaluation of the cost factors and turn-round cycle times possible.
The Abel Air swop-body system uses the pneumatic principle to elevate the demountable body. Complementary to the established Abelson Motors hydraulically operated system, it offers a distinct advan tage in that independent inflation of the pneumatic raising units by any 100lb p.s.i. air line is possible.
A further design feature is that BR Freightliner locating cones and base corner locking blocks are incorporated into all Abel Air swop-body frames, so that by the addition of grappler slots, air clamps and a container or other appropriate body the units are suitable for Freightliner movement.
A special articulated skeletal trunker trailer has been developed by Abelson for the multiple movement of Abel Air containers. After the trunk movement the containers can be left free-standing at a suitable height for self-remounting on to single unit vehicles for local delivery.
The D-Mount system made by Hazlernere Motor Co. (Waltham Abbey) Ltd. was primarily designed for high-volume furniture traffic but it is readily adaptable for other body types. Coupling is facilitated by a special "Sureguide" wheel engaging in a longitudinal channel running under the container, locating the rear. The chassis is steered under the container until the front posts of the sub-frame engage in locating forks on the container bulkhead. Hightensile steel pins automatically engage to firmly locate the container and when mounting bolts have been tightened the vehicle is roadworthy.
The D-Mount device uses a skeletal subframe attached to the chassis with outrigged mounting points for the body. The container body underframe incorporates two box-section cross-members and drive shafts in which screw lifting-jacks are inserted. The jack drive is transmitted by the drive shafts across the body, so that the two front and rear jacks are lifted simultaneously.
Lifting jacks are inserted and drive shafts coupled at journey's end, the body being released from the sub-frame by unscrewing four large mounting bolts and swinging them clear. Winding the jacks some 4-5in, lifts the body clear of the sub-frame, engages the Sureguide wheel and enables the chassis to be driven away. Tubular stay rods are then secured.
A relative newcomer to the swop-body field is W. E. and F. Dobson, of the Dobson Harwick Group, whose expertize in the manufacture of steel pit props has been useful in developing hydraulic container support legs. One of the Dobson systems incorporates hydraulic leg supports which retract after use into a recess built into the container body. This method enables the container to be lowered to ground level, making it suitable for use as a mobile office, stores, workshop, first-aid centre, library, etc.
The Owen organization's Highway container off-loading system utilizes container legs carried in a special rack beneath the semi-trailer. When the air-actuated hydraulic leg gear is operated the rams descend to the ground. A booster valve on the control box of the legs is operated so that the weight of the semi-trailer is partially removed from the tractor unit. The fifth-wheel of the tractor unit is uncoupled with the air line still connected, and, the booster valve of the leg gear is again operated, raising the semitrailer about 3in. from the ground. The container legs are positioned in the leg sockets provided in the container underframe, the legs are retracted, and the tractor unit re-coupled to the semi-trailer at the correct height, permitting the semitrailer to be driven out from under the containerized load.
The Load-O-Matic (Pengco) system of Peterborough Engineering Co. Ltd. is made under licence from a West German firm. There are more than 1,000 units operating in Germany.
Any type of body, even refrigerated or bulk tanker, can be specified. The straight forward hydraulic system can be powered from the traction unit or an independent power source—hydraulic or electrical— may be fitted in the trailer. The system is very flexible. Two bodies can be carried on a single semi-trailer and road/rail interchange is practicable provided wagons and powered vehicles are approximately the same height. Continental operators carry two bodies as a truck /trailer unit.
Hydraulic rams located over the rear axle, and controlled from the cab, disengage the body from chassis guide-rails. There is a special sub-frame with four hinged landing supports and incorporating rollers at the front end to allow the body to move easily along the chassis guide-rails. The body is automatically locked on to the chassis in the last stage of the loading cycle. Unlocking is automatic when the unloading cycle commences.
A. C. Penman Ltd., of Dumfries, makes a Jack Leg system suitable for ISO and standard containers and a patent Ramp swop-body system which can, if desired, be used in conjunction with it. Both systems have proved very popular. The Jack Leg system enables containers to be carried on a standard platform body, giving a dualpurpose vehicle. A 15in. leg adjustment means that containers can be matched against any normal loading bank.
The Penman Ramp system is delightfully simple. Arriving with an empty container the driver pulls out of the sides of the container retractable tubes fitted with rollers and backs between the Penman ramps at a loading bay. The rollers run up the ramps and lift the container clear, allowing the vehicle to drive out to collect a loaded container on another set of ramps. The whole operation is entirely under the control of the driver and it is claimed that a fresh load can be picked up in under two minutes.
Penman Jack systems can be supplied for ISO containers with a maximum container load of 20 tons. Geared winding or hand
hydraulic models are available. An interesting application of the Jack Leg principle was employed by the Priestner storage and distribution organization. Because the warehouse concerned had only one loading door, wheels were fitted to the Jack Legs and containers are loaded one at a time and then pushed on rails to the side, to await collection.
The hydraulic "lift-off" system used by Rollalong Ltd. is designed for medium weight Bedford, BMC and Ford vehicles, but providing certain measurements are adhered to bodies of different types, including Lancashire flats, are interchangeable between vehicles of varying makes within the fleet.
The system is based on two chassismounted cross-beams, interchangeable be tween the three makes. Location cones mounted at the ends of the cross-beams nest into matching cones in the body base frame.
This reduces the necessity for accurate positioning of vehicle under the swop-body—a tolerance of about 6in. in each direction is possible. The cones are provided with anchorage devices.
Manual or electro-hydraulic systems can be specified. The power packs are com pletely self-contained. A manual pack, for example, can be kept for temporary service, the changeover time taking no more than 20min. Although designed for a maximum gross load of 16 tons it is recommended that manual systems are restricted to 10 tons for regular operation.
To save cost, the electro-hydraulic system is battery operated. The low-pressure system used is normally well within battery capacity but in the unlikely event of power pack failure the driver can drain the system and return the body to the transit position.
Rollalong, which also makes custom-built containers, produces a number of container lifting systems utilizing screw legs, and a simple adjustable leg system, with coupled hydraulic bottle jacks.